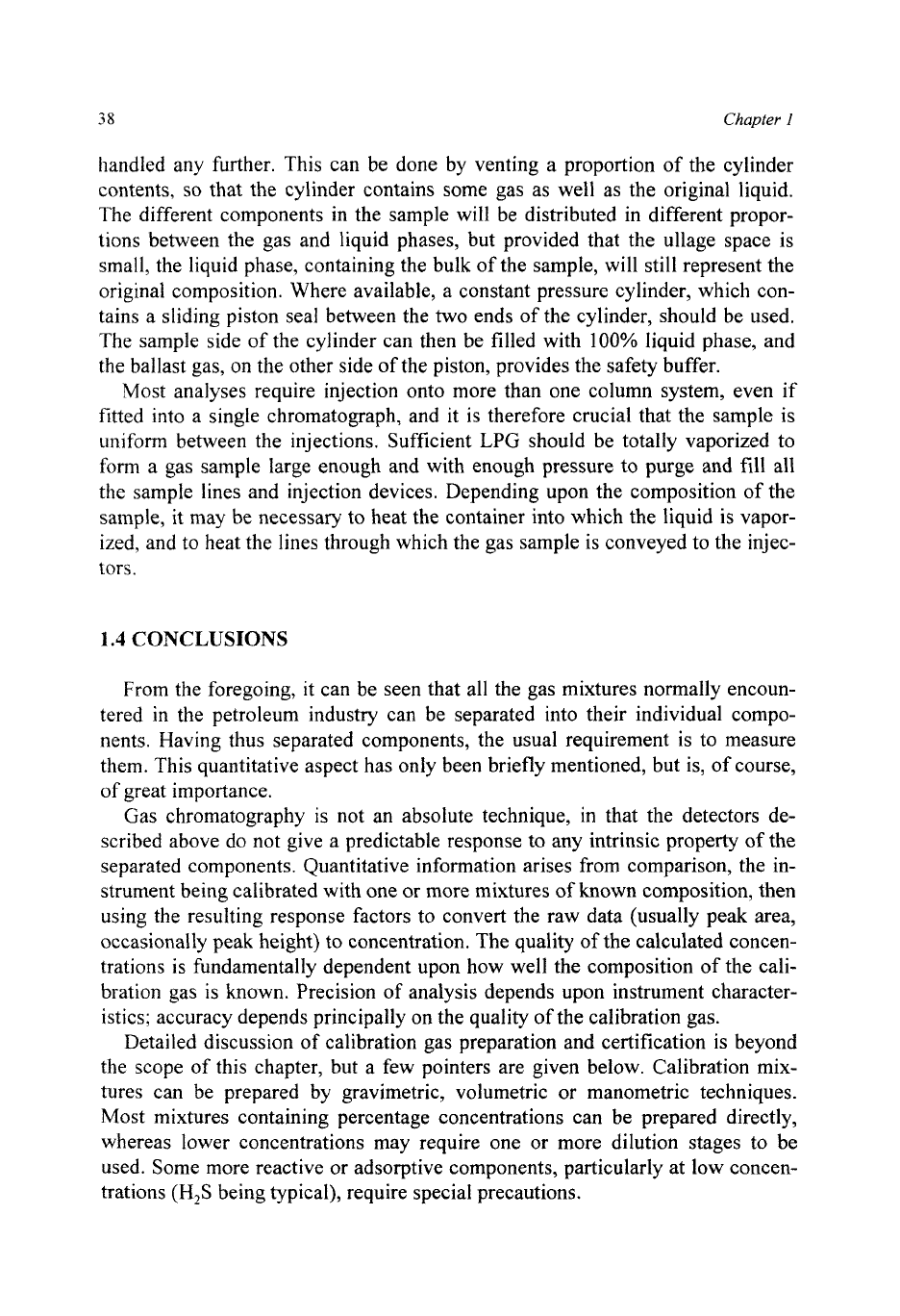
38
Chapter
I
handled any further. This can be done by venting a proportion of the cylinder
contents,
so
that the cylinder contains some gas as well as the original liquid.
The different components in the sample will be distributed in different propor-
tions between the gas and liquid phases, but provided that the ullage space is
small, the liquid phase, containing the bulk of the sample, will still represent the
original composition. Where available, a constant pressure cylinder, which con-
tains a sliding piston seal between the
two
ends of the cylinder, should be used.
The sample side
of
the cylinder can then be filled with
100%
liquid phase, and
the ballast gas, on the other side of the piston, provides the safety buffer.
Most analyses require injection onto more than one column system, even if
fitted into a single chromatograph, and it is therefore crucial that the sample is
uniform between the injections. Sufficient
LPG
should be totally vaporized to
form
a gas sample large enough and with enough pressure
to
purge and fill all
the sample lines and injection devices. Depending upon the composition of the
sample, it may be necessary to heat the container into which the liquid is vapor-
ized, and to heat the lines through which the gas sample is conveyed to the injec-
tors.
1.4
CONCLUSIONS
From the foregoing,
it
can be seen that all the gas mixtures normally encoun-
tered in the petroleum industry can be separated into their individual compo-
nents. Having thus separated components, the usual requirement is to measure
them. This quantitative aspect has only been briefly mentioned, but is, of course,
of great importance.
Gas chromatography is not an absolute technique, in that the detectors de-
scribed above do not give a predictable response to any intrinsic property
of
the
separated components. Quantitative information arises from comparison, the in-
strument being calibrated with one
or
more mixtures
of
known composition, then
using the resulting response factors to convert the raw data (usually peak area,
occasionally peak height) to concentration. The quality of the calculated concen-
trations is fundamentally dependent upon how well the composition of the cali-
bration gas is known. Precision of analysis depends upon instrument character-
istics; accuracy depends principally on the quality of the calibration gas.
Detailed discussion
of
calibration gas preparation and certification
is
beyond
the scope of this chapter, but a few pointers are given below. Calibration mix-
tures can be prepared by gravimetric, volumetric or manometric techniques.
Most mixtures containing percentage concentrations can be prepared directly,
whereas lower concentrations may require one
or
more dilution stages to be
used. Some more reactive
or
adsorptive components, particularly at
low
concen-
trations
(H,S
being typical), require special precautions.