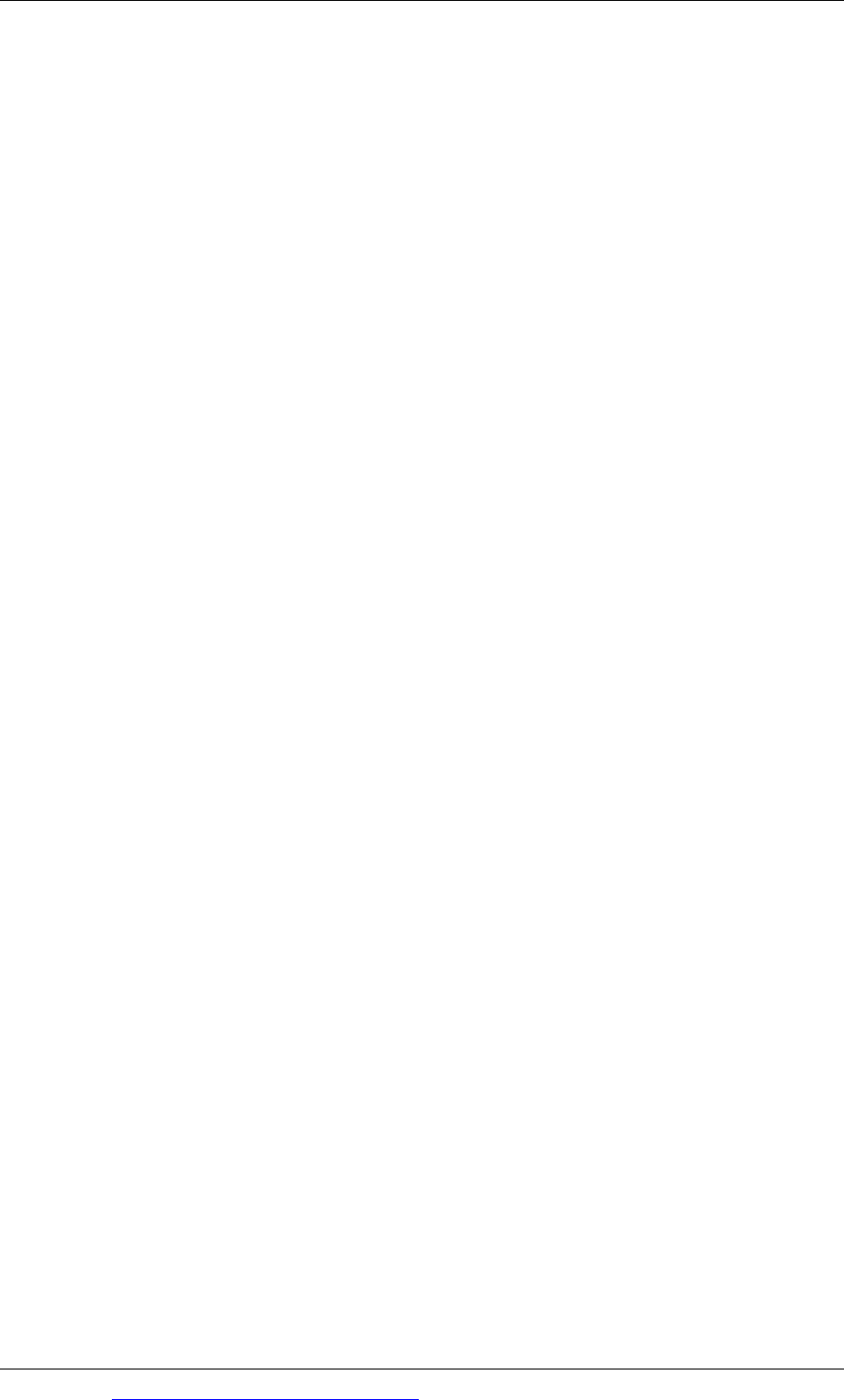
Paper P5: Advanced performance management
548 Go to www.emilewoolfpublishing.com for Q/As, Notes & Study Guides © EWP
(5) measures to improve production systems, such as minimising inventory
levels, minimising the movement of materials, minimising setup times:
all these take time and money but do not add any value.
(b)
Quality-related costs can be grouped into four categories:
(1) Prevention costs: these are costs incurred in preventing quality
problems. Important elements of prevention costs are costs of ensuring
good product design and costs of training employees.
(2) Appraisal costs: these are the costs of testing for quality, such as
inspection costs and quality control costs.
(3) Internal failure costs: these are the costs of faults and errors in
processing, such as costs of waste, scrap and re-working rejected items.
(4) External failure costs: these are the costs of quality problems after the
product (or service) has been delivered to the customer such as the cost
of handling customer complaints, and the loss of future business/sales.
In the traditional approach, the aim should be to minimise the total of quality-
related costs. At this cost-minimising level of quality, some errors will occur.
The TQM approach is that all errors should be avoided and sub-standard
work is unacceptable. External failure costs are under-estimated, and it is
worth spending money on prevention and appraisal costs to avoid internal
and external failure costs, which will be higher.
(c)
Key aspects of JIT management are:
(1) Hold no inventory. This requires just-in-time purchasing (to avoid raw
materials inventory) and just-in-time production (to avoid finished
goods inventory). Holding inventory is wasteful, and does not add
value.
(2) Just-in-time purchasing calls for close collaboration with key suppliers.
(3) Just-in-time production involves trying to produce items exactly in time
to meet customer needs for delivery: this calls for fast production times
and avoiding breakdowns and any hold-ups or bottleneck in
production.
(4) Production systems need to be flexible, to react to changes in demand
from customers.
(5) Avoid over-production (which results in finished goods inventory).
(6) Eliminate inefficiency and poor quality in production – eliminate waste,
minimise the movement of materials (which adds no value), minimise
waiting times, improve the layout of the factory floor (to minimise
movement of materials), reduce setup times (which do not add value)
and improve visibility in the work place (by using cards or other
signalling systems).
(d) Activity based management uses activity based costing to analyse the cost of
activities within an organisation. It focuses on the cost of activities and the
causes of these costs occuring (cost drivers). The aim of ABM should be to
improve the value obtained from the activities, eliminate activities that do not
add value or reduce the costs of activities.