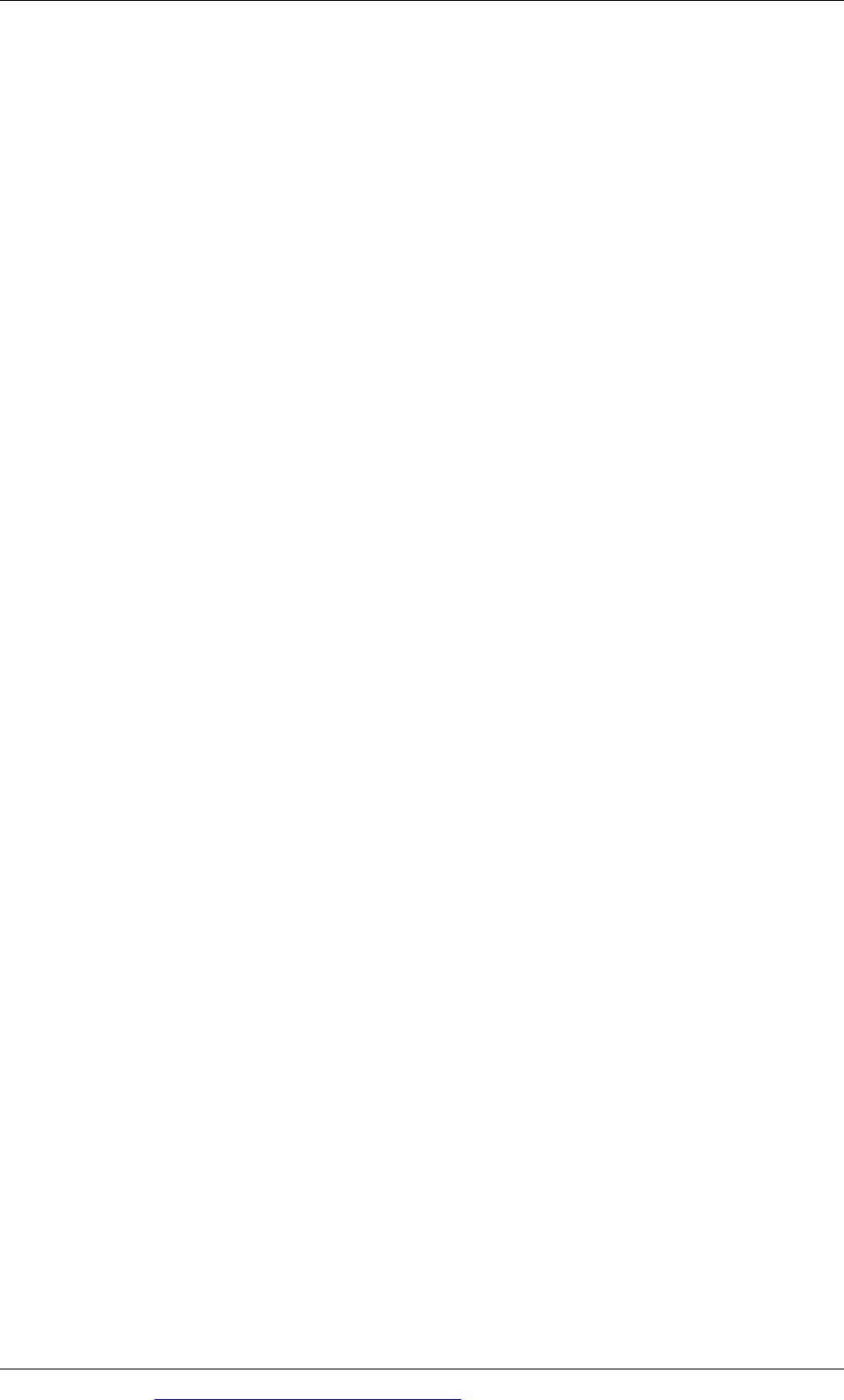
Practice questions
© EWP Go to www.emilewoolfpublishing.com for Q/As, Notes & Study Guides 485
49 Total quality
(a) List the key aspects of Total Quality Management (TQM).
(b)
What are quality-related costs? What is the TQM approach to quality-related
costs, and how does this differ from the more traditional approach to these
costs?
(c)
List the key aspects of just-in-time (JIT) management
(d)
Briefly explain the nature of activity based management (ABM).
50 Poole Company
Poole Company makes and sells a single product. The existing product
specifications are as follows:
Material X
8 square metres at $4 per square metre
Machine time 0.6 running hours
Other machine costs $40/hour
Selling price $100
Poole Company needs to fulfil orders for 5,000 units per period. There will be no
change in inventory level during the period.
The following Information is available about performance before the introduction of
a TQM programme:
(1) 5% of incoming material from suppliers is scrapped due to poor receipt and
storage.
(2) 4% of material input to the machine process is wasted in process.
(3) Inspection and storage of material cost $0.10 per metre.
(4) Inspection during the cycle costs $25,000 per period.
(5) Production is increased to allow for the downgrading of 12.5% of units at the
final inspection phase. Downgraded units are sold as ‘second quality’ units at
a discount of 30% of the final selling price.
(6) Production is increased to allow for returns from customers. These are
replaced free of charge. Returns are due to specification failure and account
for 5% of units initially delivered to customers. Replacement units incur a
delivery cost of $8 per unit. 80% of the returns from customers are rectified
using 0.2 hours of machine running time and are resold as ‘third quality’
products at a discount of 50% on the standard selling price. The remaining
returned units are sold as scrap for $5 per unit.
(7) Product liability claims are estimated at 3% of sales revenue from standard
product sales.
(8) Machine idle time is 20% of gross machine hours used.
(9) Sundry costs of administration, selling and distribution total $60,000 per
period.
(10) Poole Company is aware of these excess costs and currently spends $20,000
per period to prevent them from happening.