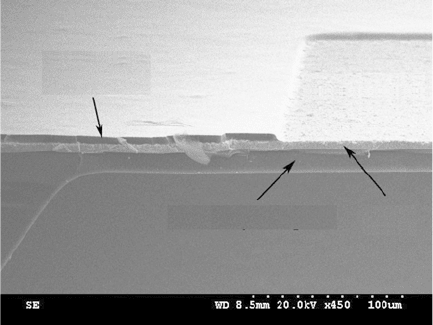
Handbook of dielectric, piezoelectric and ferroelectric materials740
Usually, the PZT film, especially the thin sol–gel film, tends to crack at
the edge of the bottom electrode. Electric short-circuit occurs when the
patterned top electrode interconnection passes across the edge of the bottom
electrode although this part is often designed to be covered by PZT film.
Therefore, making a good interconnection between the top electrode and its
electric contact pad is one of the challenges in pMUT fabrication. In our
design, a polyimide layer is utilized to cover the top of the PZT film at the
edge part to overcome this problem. Figure 24.14 shows that the smooth
surface and well-curved slope covered at the edge of PZT layer facilitate the
interconnection of the top electrode. In addition, the very dense polyimide
layer prevents the electric short-circuit at the edge part of the bottom electrode.
24.5.3 Etching of the PZT thick film
In general, there are two approaches to micromachine the PZT film: dry
etching and wet etching. Reactive ion etching (RIE), inductively coupled
plasma (ICP) and electron cyclotron resonance (ECR) excitation, have been
reported to etch PZT films. These studies are driven primarily by ferroelectric
memory applications, where the film thickness generally does not exceed
250nm. However, the dry PZT etching technique is not well developed
because there is no common halogenous gas that forms a volatile compound
with all three elements (Pb, Zr, Ti) to guarantee the residue-free removal of
the film. The volatility of the reactive products of individual Pb, Zr and Ti is
different. Heating the substrate or increasing the ion bombardment is often
Polyimide
Active area
Diaphragm
PZT
24.13
Top profile image of a fabricated pMUT diaphragm. Backside
silicon is wet etched by the KOH. The PZT film is 5µm in thickness
and the total thickness of the support layer is 13µm. The effective
top electrode area of the element is defined by an opened window
on polyimide layer.