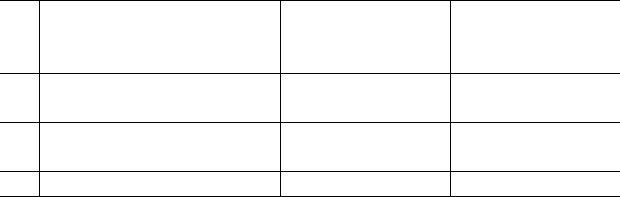
139
сколько ценных компонентов, причем полнота извлечения и исполь-
зования сырья – категория историческая и зависит от потребностей
общества и уровня развития техники. Так, например, в районах ин-
тенсивного развития цветной металлургии (Урал, Алтай, Норильск и
др.) ждут своего часа отвалы шлаков старых и действующих заводов,
содержащих большое количество ценных элементов (молибдена, ко-
бальта, кадмия, теллура, германия, рения и др.). Строительство и со-
держание отвалов требует затрат значительных средств. Например,
только за сутки работы ТЭС средней мощности сжигается около 10
тыс. т угля и образуется более 1000 т золы, под отвал которой высо-
той 8 м требуется площадь более 1 га в год. В то же время, эти шлаки
являются ценным сырьем для различных отраслей народного хозяй-
ства, например, промышленности строительных материалов. На
предприятиях черной металлургии в эпоху СССР из 600 млн. м
3
еже-
годного объема накапливаемых пород и шлаков использовалось
лишь 13 млн. м
3
. В отвалах накоплено более 440 млн. т доменных и
сталеплавильных шлаков. Ежегодно добавляется еще 26 млн. т шла-
ков и 25 млн. т отходов обогатительных фабрик. На предприятиях
цветной металлургии содержится в отвалах 455 млн. т неиспользо-
ванных шлаков и ежегодно образуется еще около 32 млн. т твердых
отходов. На сернокислотных заводах накоплено 28 млн. т пиритных
огарков, содержащих 39 % железа, и ежегодно к ним добавляется
еще 5.7 млн. т. Предприятиями, производящими калийное удобрение
сильвинит (KCl
⋅NaCl) накоплено 500 млн. т галитовых (солевых) от-
ходов. Это количество ежегодно увеличивается еще на 50 млн. т, в то
время как намечаемое их использование составляет всего 6.4 млн. т в
год. В отвалах заводов по производству фосфорной кислоты нахо-
дится около 120 млн. т фосфогипса. Лесозаготовительные предпри-
ятия накопили более млн. м
3
древесной коры, причем из 17 млн. м
3
,
образующихся ежегодно используется лишь 9 %.
Приведенный перечень свидетельствует, что проблема сущест-
вует и стоит достаточно остро. Беда в том, что предприятия, остав-
шиеся новым независимым государствам в наследство от СССР,
строились давно, без учета экологической ситуации. И этим предпри-
ятиям еще долго предстоит работать. Перевод действующих произ-
водств на замкнутый цикл сопряжен с решением сложных техниче-
ских проблем и затратой значительных средств. Видится единствен-
ный выход – довести отходы до уровня товарной продукции или ис-
пользовать их как сырье для своего производства или в других от-
раслях промышленности. Практическое осуществление этих задач
140
станет важнейшим фактором снижения загрязненности окружающей
среды. Сложность стоящей задачи определяется многотоннажностью
накопленных отходов и отсутствием, как правило, в местах их обра-
зования потребителей. В наибольшей степени эти трудности харак-
терны для отходов предприятий горнодобывающей промышленно-
сти.
При добыче полезных ископаемых образуются миллиарды
тонн отходов (отвалы при открытой добыче, порода при шахтной
добыче, хвосты обогатительных фабрик, шахтные воды и воды осу-
шения карьеров, газовые выбросы). На долю твердых отходов горно-
добывающих предприятий приходится 70–75 % общего объема про-
изводственных отходов. Твердые отходы могут найти применение
при производстве стройматериалов (цемента, строительного щебня,
кирпича, стекла, керамических изделий и др.), для закладки вырабо-
танного пространства, для извлечения ценных компонентов. Можно
привести и примеры эффективного использования твердых отходов.
Так, при обжиге железной, марганцевой и других руд образуется
много отходов, которые используют на предприятиях по производ-
ству щебня (от 1 до 8 млн. м
3
в год), цемента (3 млн. т), известковой
муки (1.5 – 7 млн. т), извести (0.3 млн. т). В ряде случаев стоимость
попутных материалов превышает стоимость основных. Например, на
Сафоновском месторождении Московского угольного бассейна
стоимость огнеупорной глины, входящей в состав добываемого сы-
рья, выше стоимости угля.
Анализ технико-экономических данных работы различных
предприятий, производящих щебень из отходов, и сравнение их с
данными производства из природных материалов показывают более
высокую эффективность использования отходов (табл. 3.6.).
Таблица 3.6. Сравнение показателей предприятий, производящих
щебень из отходов и природного сырья
№ Технико-экономический
показатель
Производство из
отходов
Производство из
природного
сырья
1 Себестоимость щебня,
усл. ед.
0.65–3.3 3.5–4.5
2 Удельные капитальные
затраты, усл. ед.
2.7–9.9 10–15
3 Срок окупаемости, лет 3 5–6