Подождите немного. Документ загружается.
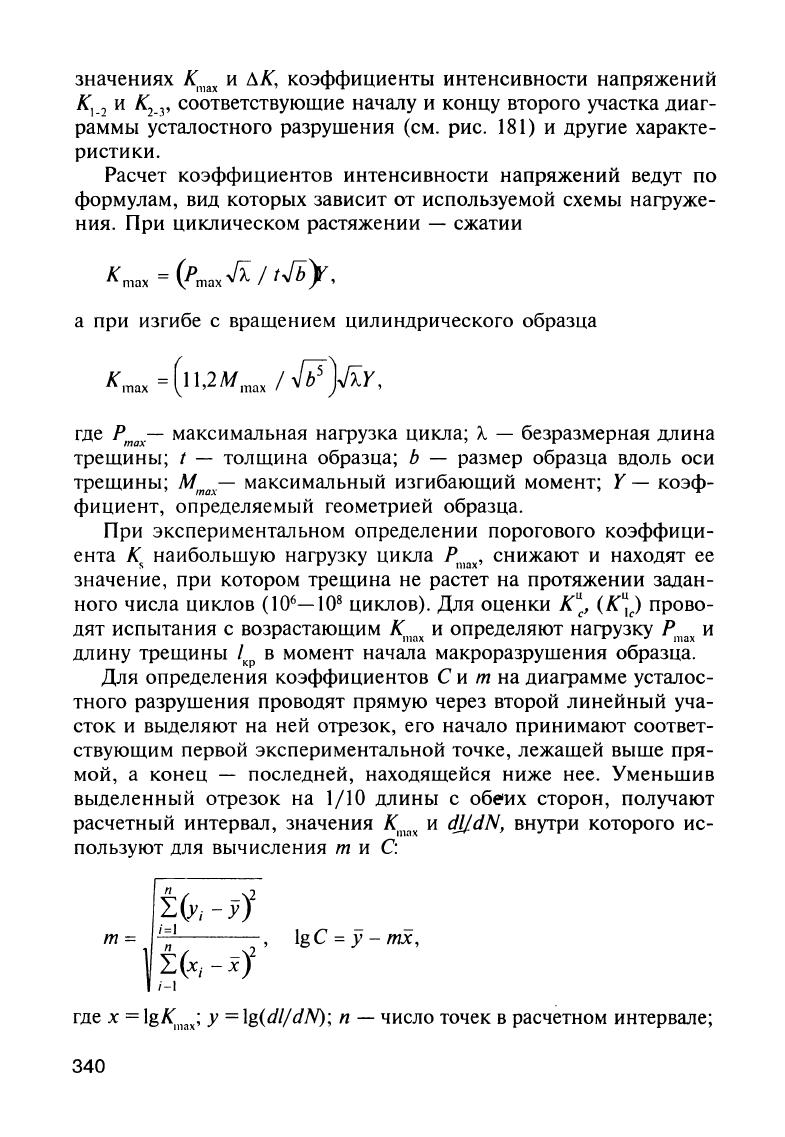
значениях
к'l1ах
И
I::!K,
коэффициенты
интенсивности
напряжений
К
l
_
2
и
К
2
_
З
'
соответствующие
началу
и
концу
второго
участка
диаг
раммы
усталостного
разрушения
(см.
рис.
181)
и
другие
характе
ристики.
Расчет
коэффициентов
интенсивности
напряжений
ведут
по
формулам,
вИд
которых
зависит
от
используемой
схемы
нагруже
ния.
При
циклическом
растяжении
-
сжатии
а
при
изгибе
с
вращением
цилиндрического
образца
где
Р
тох
-
максимальная
нагрузка
цикла;
л.
-
безразмерная
длина
трещины;
t -
толщина
образца;
Ь
-
размер
образца
вдоль
оси
трещины;
М
тох
-
максимальный
изгибающий
момент;
У
-
коэф
фициент,
определяемый
геометрией
образца.
При
экспериментальном
определении
порогового
коэффици
ента
к"
наибольшую
нагрузку
цикла
Р'l1.Х'
снижают
и
находят
ее
значение,
при
котором
трещина
не
растет
на
протяжении
задан
ного
числа
циклов
(106-108
циклов).
Для
оценки
K~,
(K~)
прово
дят
испытания
с
возрастающим
к'l1nХ
И
определяют
нагрузку
P'l1.X
и
длину
трещины
/кр
в
момент
начала
макроразрушения
образца.
Для
определения
коэффициентов
С
и
т
на
диаграмме
усталос
тного
разрушения
проводят
прямую
через
второй
линейный
уча
сток
и
выделяют
на
ней
отрезок,
его
начало
принимают
соответ
ствующим
первой
экспериментальной
точке,
лежащей
выше
пря
мой,
а
конец
-
последней,
находящейся
ниже
нее.
Уменьшив
выделенный
отрезок на
1/10
длины
с
обе'ИХ
сторон,
получают
расчетный
интервал,
значения
к'l1ах
И
4JjdN,
внутри
которого
ис
пользуют
для
вычисления
т
и
С:
т=
t(X
j
-Х)'
IgC =
у
-
тХ,
;-1
где
Х
=
19к'l1.Х;
у
= Ig(d/jdN); n -
число
точек
в
расчетном
интервале;
340
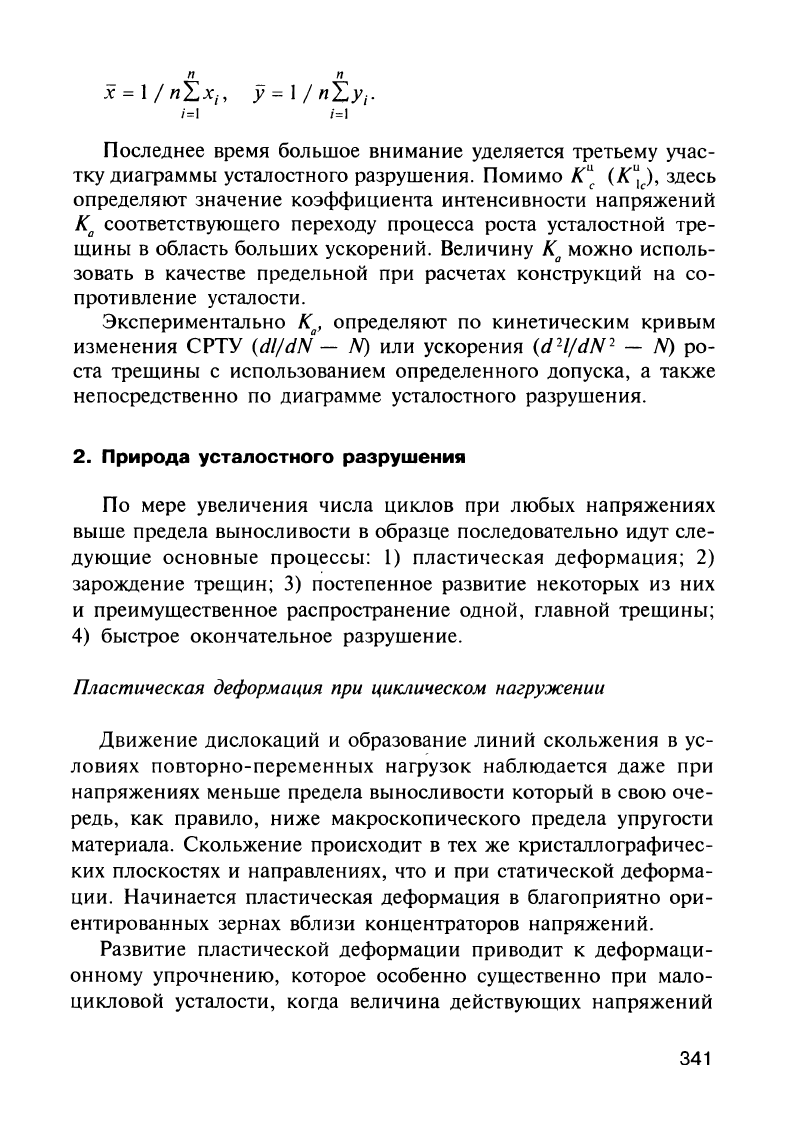
n
n
•
~
=
1/
nLx;,
у
=
1/
nLy;
.
i=1
i=1
Последнее
время
большое
внимание
уделяется
третьему
учас
тку
диаграммы
усталостного
разрушения.
Помимо
K~
(K~),
здесь
определяют
значение
коэффициента
интенсивности
напряжений
Ка
соответствующего
переходу
процесса
роста
усталостной
тре
щины
в
область
больших
ускорений.
Величину
Ка
можно
исполь
зовать
в
качестве
предельной
при
расчетах
конструкций
на
со
противление
усталости.
Экспериментально
Ка'
определяют
по
кинетическим
кривым
изменения
срту
(d//dN - N)
или
ускорения
(d2f/dN2 - N)
ро
ста
трещины
с
использованием
определенного
допуска,
а
также
непосредственно
по
диаграмме
усталостного
разрушения.
2.
Природа
устаnостного
разруwения
По
мере
увеличения
числа
циклов
при
любых
напряжениях
выше
предела
выносливости
в
образце
последовательно
идут
сле
дующие
основные
процессы:
1)
пластическая
деформация;
2)
зарождение
трещин;
3)
постепенное
развитие
некоторых
из
них
и
преимущественное
распространение
одной,
главной
трещины;
4)
быстрое
окончательное
разрушение.
Пластическая
деформация
при
циклическом
нагружении
Движение
дислокаций
и
образов~ние
линий
скольжения
в
ус
ловиях
повторно-переменных
нагрузок
наблюдается
даже
при
напряжениях
меньше
предела
выносливости
который
в
свою
оче
редь,
как
правило,
ниже
макроскопического
предела
упругости
материала.
Скольжение
происходит
в тех
же
кристаллографичес
ких
плоскостях
и направлениях,
что
и
при
статической
деформа
ции.
Начинается
пластическая
деформация
в
благоприятно
ори
ентированных
зернах
вблизи
концентраторов
напряжений.
Развитие
пластической
деформации
при
водит
к
деформаци
онному
упрочнению,
которое
особенно
существенно
при
мало
цикловой
усталости,
когда
величина
действующих
напряжений
341
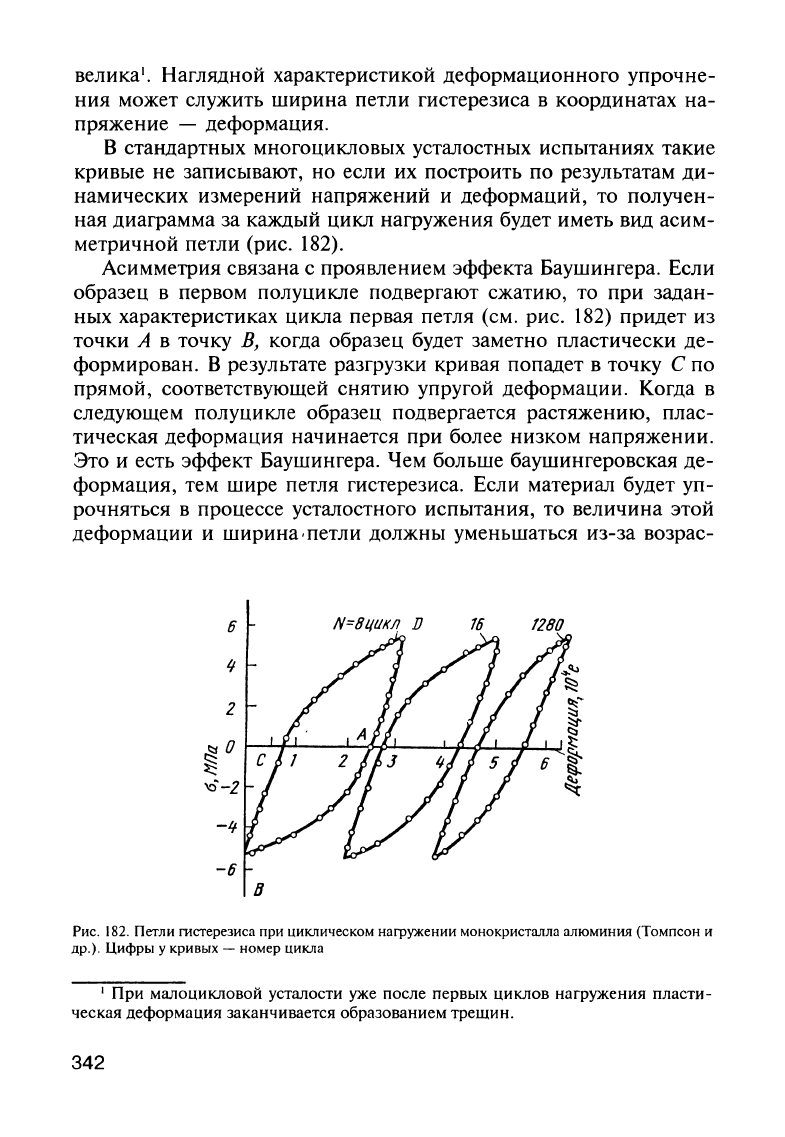
велика
l
•
Наглядной
характеристикой
деформационного
упрочне
ния
может
служить
ширина
петли
гистерезиса
в
координатах
на
пряжение
-
деформация.
В
стандартных
многоцикловых
усталостных
испытаниях
такие
кривые
не
записывают,
но
если
их
построить
по
результатам
ди
намических
измерений
напряжений
и
деформаций,
то
получен
ная
диаграмма
за
каждый
цикл
нагружения
будет
иметь
вид
асим
метричной
петли
(рис.
182).
Асимметрия
связана
с
проявлением
эффекта
Баушингера.
Если
образец
в
первом
полуцикле
подвергают
сжатию,
то
при
задан
ных
характеристиках
цикла
первая
петля
(см.
рис.
182)
придет
из
точки
А
в
точку
В,
когда
образец
будет
заметно
пластически
де
формирован.
В
результате
разгрузки
кривая
попадет
в
точку
С
ПО
прямой,
соответствующей
снятию
упругой
деформации.
Когда
в
следующем
полуцикле
образец
подвергается
растяжению,
плас
тическая
деформация
начинается
при
более
низком
напряжении.
Это
и
есть
эффект
Баушингера.
Чем
больше
баушингеровская
де
формация,
тем
шире
петля
гистерезиса.
Если
материал
будет
уп
рочняться
в
процессе
усталостного
испытания,
то
величина
этой
деформации
и
ширина·петли
должны
уменьшаться
из-за
возрас-
5
N=8I/UКЛ
О
16
1280
-5
в
Рис.
182.
Петли
гистерезиса
при
циклическом
нагружении
монокристалла
алюминия
(Томпсон
и
др.).
Цифры
у
кривых
-
номер
цикла
I
При
малоцикловой
усталости
уже
после
первых
циклов
нагружения
пласти
ческая
деформация
заканчивается
образованием
трещин.
342
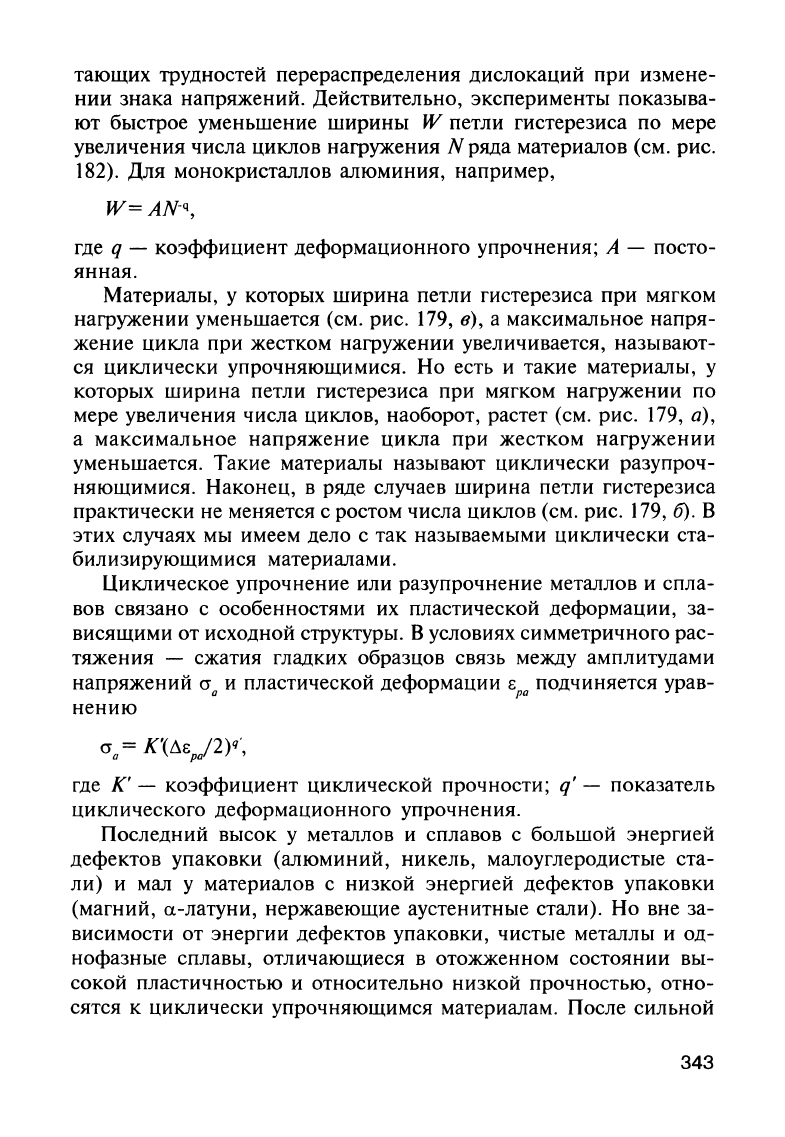
тающих
трудностей
перераспределения
дислокаций
при
измене
нии
знака
напряжений.
Действительно,
эксперименты
показыва
ют
быстрое
уменьшение
ширины
W
петли
гистерезиса
по
мере
увеличения
числа
циклов
нагружения
N
ряда
материалов
(см.
рис.
182).
Для
монокристаллов
алюминия,
например,
W=AN\
где
q -
коэффициент
деформационного
упрочнения;
А
-
посто
янная.
Материалы,
у
которых
ширина
петли
гистерезиса
при
мягком
нагружении
уменьшается
(см.
рис.
179,
в),
а
максимальное
напря
жение
цикла
при
жестком
нагружении
увеличивается,
называют
ся
циклически
упрочняющимися.
Но
есть
и
такие
материалы,
у
которых
ширина
петли
гистерезиса
при мягком
нагружении
по
мере
увеличения
числа
циклов,
наоборот,
растет
(см.
рис.
179,
а),
а
максимальное
напряжение
цикла
при
жестком
нагружении
уменьшается.
Такие
материалы
называют
циклически
разупроч
няющимися.
Наконец,
в
ряде
случаев
ширина
петли
гистерезиса
практически
не
меняется
с
ростом
числа
циклов
(см.
рис.
179,
6).
В
этих
случаях
мы
имеем
дело
с
так
называемыми
циклически
ста
билизирующимися
материалами.
Uиклическое
упрочнение
или
разупрочнение
металлов
и
спла
вов
связано
с
особенностями
их
пластической
деформации,
за
висящими
от
исходной
структуры.
В
условиях
симметричного
рас
тяжения
-
сжатия
гладких
образцов
связь
меЖдУ
амплитудами
напряжений
аа
и
пластической
деформации
Ера
подчиняется
урав
нению
аа
= K(!!E
p
/2)q·,
где
К'
-
коэффициент
циклической
прочности;
q'
-
показатель
циклического
деформационного
упрочнения.
Последний
высок
у
металлов
и
сплавов
с
большой
энергией
дефектов упаковки
(алюминий,
никель,
малоуглеродистые
ста
ли)
и
мал
у
материалов
с
низкой
энергией
дефектов
упаковки
(магний,
а-латуни,
нержавеющие
аустенитные
стали).
Но
вне
за
висимости
от
энергии
дефектов
упаковки,
чистые
металлы
и
од
нофазные
сплавы,
отличающиеся
в
отожженном
состоянии
вы
сокой
пластичностью
и
относительно
низкой
прочностью,
отно
сятся
К
циклически
упрочняющимся
материалам.
После
сильной
343
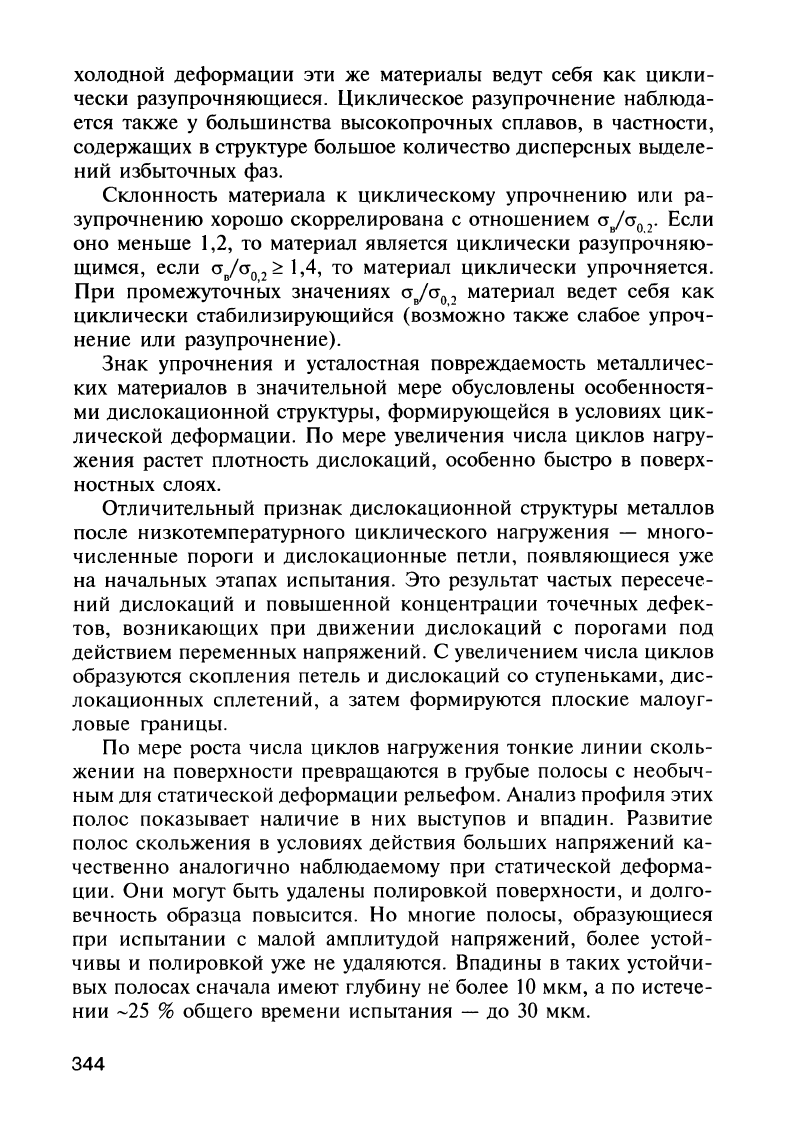
холодной
деформации
эти
же
материалы
ведут
себя
как
цикли
чески
разупрочняющиеся.
Циклическое
разупрочнение
наблюда
ется
также
у
большинства
высокопрочных
сплавов,
в
частности,
содержащих
в
структуре
большое
количество
дисперсных
вьщеле
ний
избыточных
фаз.
Склонность
материала
к
циклическому
упрочнению
или
ра
зупрочнению
хорошо
скоррелирована
с
отношением
aja
O
•
2
'
Если
оно
меньше
1,2,
то
материал
является
циклически
разупрочняю
щимся,
если
aja
o
,2;::
1,4,
то
материал
циклически
упрочняется.
При
промежуточных
значениях
aja
o
,
материал
ведет
себя
как
циклически
стабилизирующийся
(возможно
также
слабое
упроч
нение
или
разупрочнение).
Знак
упрочнения
и
усталостная
повреждаемость
металличес
ких
материалов
в
значительной
мере
обусловлены
особенностя
ми
дислокационной
структуры,
формирующейся
в
условиях
цик
лической
деформации.
По
мере
увеличения
числа
циклов
нагру
жения
растет
плотность
дислокаций,
особенно
быстро
в
поверх
ностных
слоях.
Отличительный
признак
дислокационной
структуры
металлов
после
низкотемпературного
циклического
нагружения
-
много
численные
пороги
и
дислокационные
петли,
появляющиеся
уже
на
начальных
этапах
испытания.
Это
результат
частых
пересече
ний
дислокаций
и
повышенной
концентрации точечных
дефек
тов,
возникающих
при
движении
дислокаций
с
порогами
под
действием
переменных
напряжений.
С
увеличением
числа
циклов
образуются
скопления
петель
и
дислокаций
со
ступеньками,
дис
локационных
сплетений,
а
затем
формируются
плоские
малоуг
ловые
границы.
По
мере
роста
числа
циклов
нагружения
тонкие
линии
сколь
жении
на
поверхности
превращаются
в
грубые
полосы
с
необыч
ным
для
статической
деформации
рельефом.
Анализ
профиля
этих
полос
показывает
наличие
в
них
выступов
и
впадин.
Развитие
полос
скольжения
в
условиях
действия
больших
напряжений
ка
чественно
аналогично
наблюдаемому
при
статической
деформа
ции.
Они
могут
быть
удалены
полировкой
поверхности,
и
долго
вечность
образца
повысится.
Но
многие
полосы,
образующиеся
при
испытании
с
малой
амплитудой
напряжений,
более
устой
чивы
и
полировкой
уже
не
удаляются.
Впадины
в
таких устойчи
вых
полосах
сначала
имеют
глубину
не'
более
10
мкм,
а
по
истече
нии
-25
%
общего
времени
испытания
-
до
30
мкм.
344
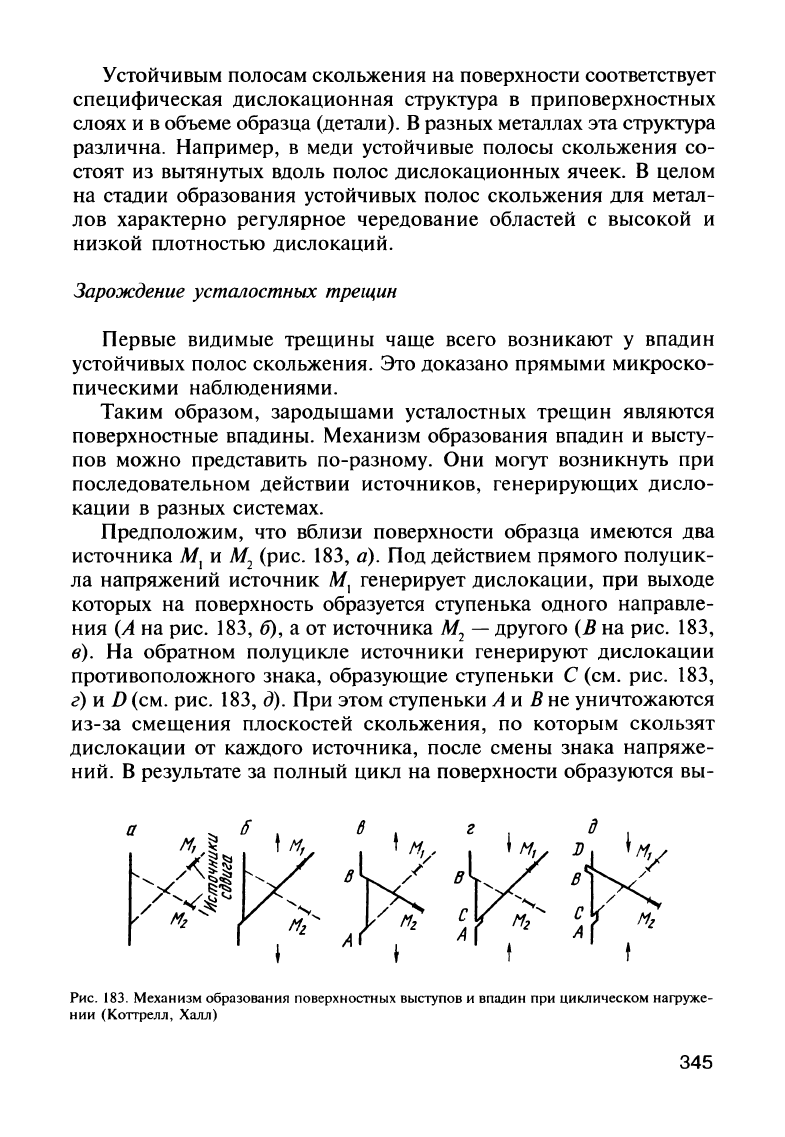
Устойчивым
полосам
скольжения
на
поверхности
соответствует
специфическая
дислокационная
структура
в
приповерхностных
слоях
и
в
объеме
образца
(детали).
В
разных
металлах
эта
структура
различна.
Например,
в
меди
устойчивые
полосы
скольжения
со
стоят
из
вытянутых
вдоль
полос
дислокационных
ячеек.
В
целом
на
стадии
образования
устойчивых
полос
скольжения
для
метал
лов
характерно
регулярное
чередование
областей
с
высокой
и
низкой
плотностью
дислокаций.
Зарождение
усталостных
трещин
Первые
видимые
трещины
чаще
всего
возникают
у
впадин
устойчивых
полос
скольжения.
Это
доказано
прямыми
микроско
пическими
наблюдениями.
Таким
образом,
зародышами
усталостных
трещин
являются
поверхностные
впадины.
Механизм
образования
впадин
и
высту
пов
можно
представить
по-разному.
Они
могут
возникнуть
при
последовательном
действии
источников,
генерирующих
дисло
кации
в
разных
системах.
Предположим,
что
вблизи
поверхности
образца
имеются
два
источника
М
1
и
М
2
(рис.
183,
а).
Под
действием
прямого
полуцик
ла
напряжений
источник
М
1
генерирует
дислокации,
при
выходе
которых
на
поверхность
образуется
ступенька
одного
направле
ния
(А
на
рис.
183,6),
а
от
источника
М
2
-
другого
(В
на
рис.
183,
в).
На
обратном
полуцикле
источники
генерируют
дислокации
противоположного
знака,
образующие
ступеньки
С
(см.
рис.
183,
г)
и
D
(см.
рис.
183,
д).
При
этом
ступеньки
А
и
В
не
уничтожаются
из-за
смещения
плоскостей
скольжения,
по
которым
скользят
дислокации
от
каждого
источника,
после
смены
знака
напряже
ний.
В
результате
за
полный
цикл
на
поверхности
образуются
вы-
iJ
]}K~J'fY
В
/
/
С
I1
!
А
t
Рис.
183.
Механизм
образования
поверхностных
выступов и
впадин
при
циклическом
нагруже
нии
(Котгрелл,
халл)
345
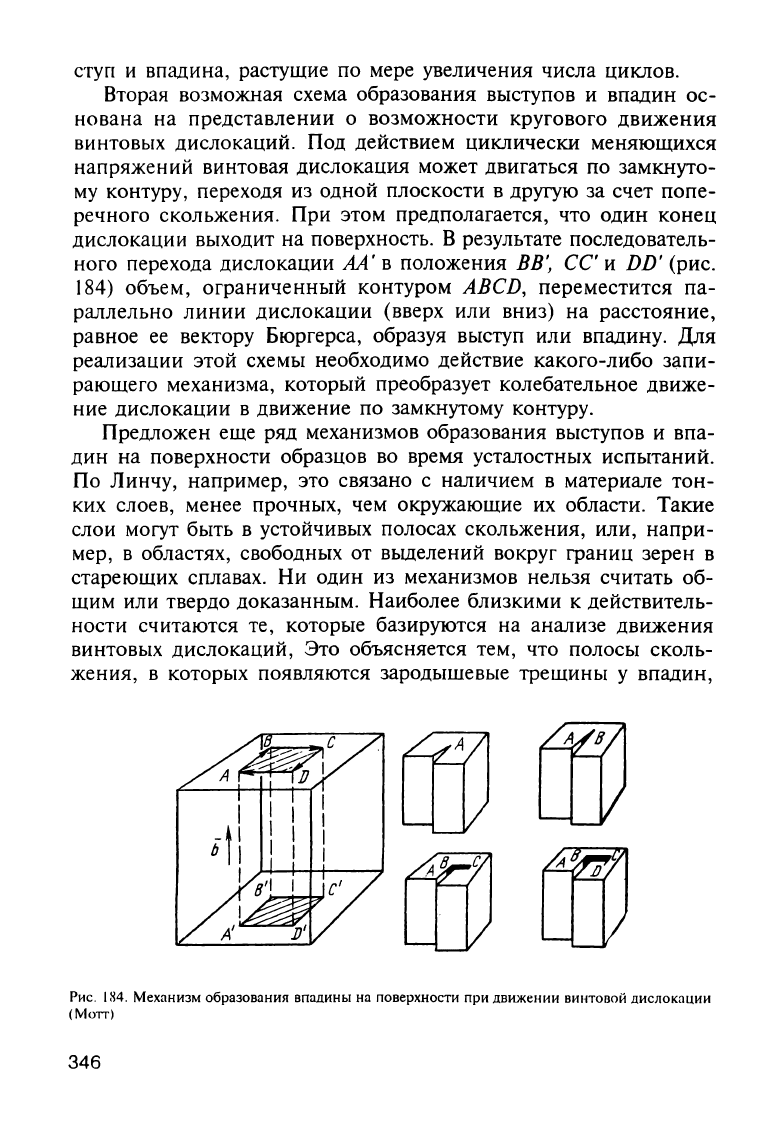
ступ
и
впадина,
растущие по
мере
увеличения
числа
циклов.
Вторая
возможная
схема
образования
выступов
и
впадин
ос
нована
на
представлении
о
возможности
кругового
движения
винтовых
дислокаций.
Под
действием
циклически
меняющихся
напряжений
винтовая
дислокаuия
может
двигаться
по
замкнуто
му
контуру,
переходя
из
одной
плоскости
в
другую
за
счет
попе
речного
скольжения.
При
этом
предполагается,
что
один
конец
дислокации
выходит
на
поверхность.
В
результате
последователь
ного
перехода
дислокации
АА'
в
положения
ВВ',
се
и
DD'
(рис.
184)
объем,
ограниченный
контуром
ABCD,
переместится
па
раллельно
линии
дислокаuии
(вверх
или
вниз)
на
расстояние,
равное
ее
вектору
Бюргерса,
образуя
выступ
или
впадину.
Для
реализаuии
этой
схемы
необходимо
действие
какого-либо
запи
рающего
механизма,
который
преобразует
колебательное
движе
ние
дислокации
в
движение
по
замкнутому
контуру.
ПредЛожен
еще
ряд
механизмов
образования
выступов
и
впа
дин
на
поверхности
образuов
во
время
усталостных
испытаний.
По
Линчу,
например,
это
связано
с
наличием
в
материале
тон
ких
слоев,
менее
прочных,
чем
окружающие
их
области.
Такие
слои
могут
быть
в
устойчивых
полосах
скольжения,
или,
напри
мер,
в
областях,
свободных
от
вьщелений
вокруг
границ
зерен
в
стареющих
сплавах.
Ни
один
из
механизмов
нельзя
считать
об
щим
или
твердо
доказанным.
Наиболее
близкими
к
действитель
ности
считаются
те,
которые
базируются
на анализе
движения
винтовых
дислокаций,
Это
объясняется
тем,
что
полосы
сколь
жения,
в
которых
появляются
зародышевые
трещины
у
впадин,
Рис.
184.
Механизм
образования
впадины
на
поверхности
при
движении
винтовой
дислокации
(Мотт)
346
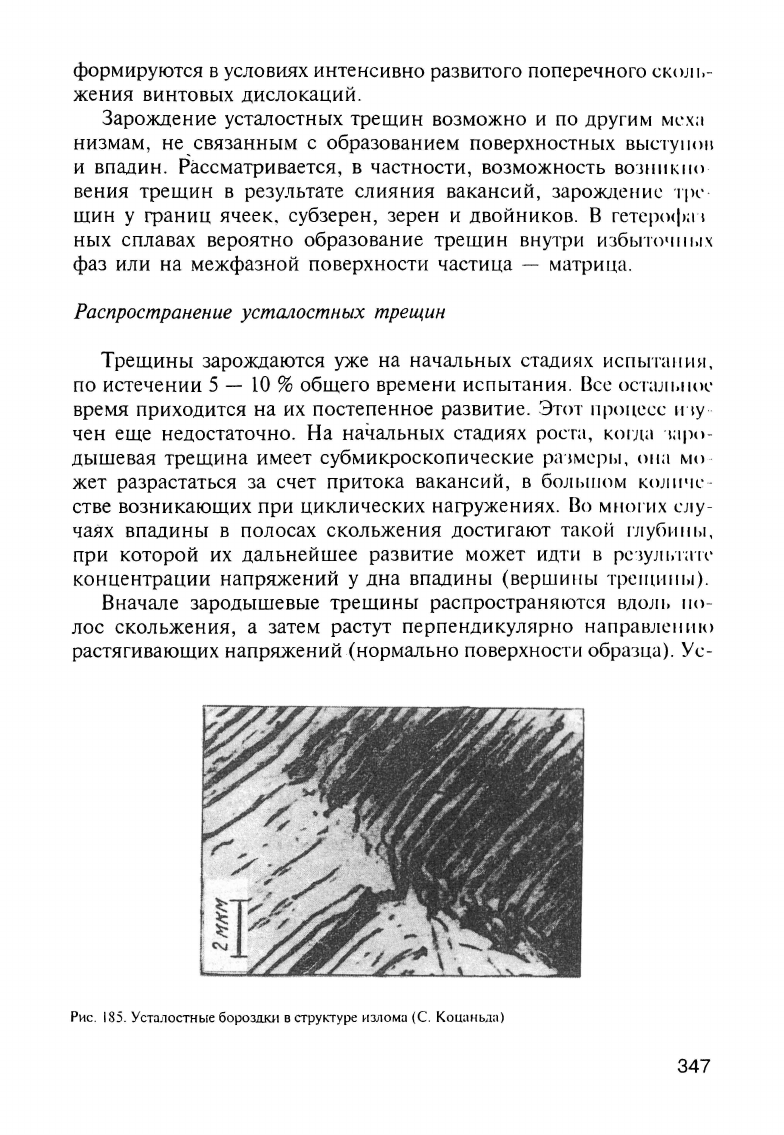
формируются
в
условиях
интенсивно
развитого
поперечного
CI<OJlI.-
жения
винтовых
дислокаций.
Зарождение
усталостных
трещин
возможно
и
по
другим
меха
низмам,
не
связанным
с
образованием
поверхностных
BbICTYII()1\
и
впадин.
Рассматривается,
в
частности,
возможность
B0311111<1IO
вения
трещин
в
результате
слияния
вакансий,
зарождение
тр('
щин
у
границ
ячеек.
субзерен,
зерен
и
двойников.
В
гетсрофаl
ных
сплавах
вероятно
образование
трещин
внутри
изБЫТО'lIlI.11<
фаз
или
на
межфазной
поверхности
частица
-
матрица.
Распространение
устШLOстных
трещин
Трещины
зарождаются
уже
на
начальных
стадиях
испытании,
по
истечении
5 -
10
%
общего
времени
испытания.
Все
ОСТ<1ЛI>IIОl'
время
приходится
на их
постепенное
развитие.
Этот
процссс
IПУ
чен
еще
недостаточно.
На
начальных
стадиях
роста,
коm<11аро
дышевая
трещина
имеет
субмикроскопические
pa·JMCpbl,
olla
м()
жет
разрастаться
за
счет
притока
вакансий,
в
БОЛЫIЮМ
KOJIII'Il'-
стве
возникающих
при
циклических
нагружениях.
ВО
МНОПIХ
CJlY-
чаях
впадины
в
полосах
скольжения
достигают
такой
глуfiИIII.I,
при
которой
их
дальнейшее
развитие
может
идти
в
rC'JYJII.I<1Tl'
концентрации
напряжений
у
дна
впадины
(вершины
TPCII\IIIII.I).
Вначале
зародышевые
трещины
распространяются
ВЛОJII.
II()-
лос
скольжения,
а
затем
растут
перпендикулярно
напраВЛСIIИЮ
растягивающих
напряжений
(нормально
поверхности
образца).
Ус-
Рис.
185.
Устолостные
бороздки
В
структуре
излома
(с.
Коцань,ы)
347
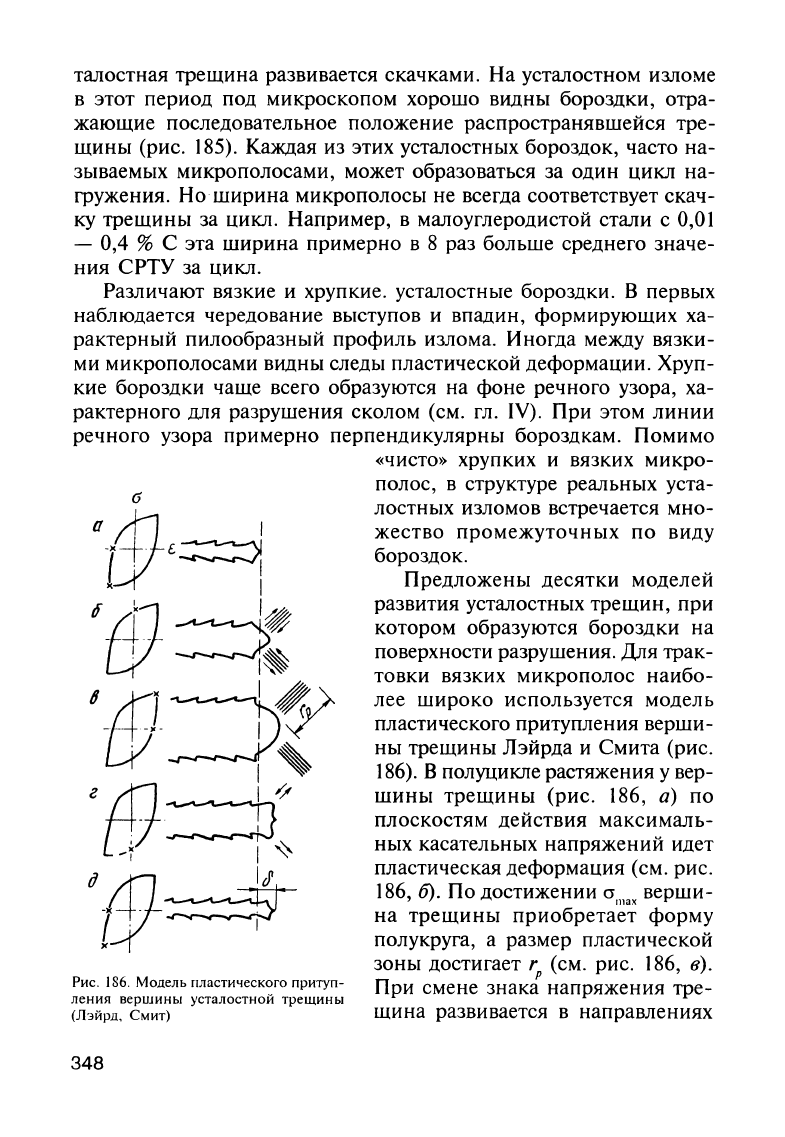
талостная
трещина
развивается
скачками.
На
усталостном
изломе
в
этот
период
под
микроскопом
хорошо видны
бороздки,
отра
жающие
последовательное
положение
распространявшейся
тре
щины
(рис.
185).
Каждая
из
этих
усталостных
бороздок,
часто
на
зываемых
микрополосами,
может
образоваться
за
один
цикл
на
гружения.
Но
ширина
микрополосы
не
всегда
соответствует
скач
ку
трещины
за
цикл.
Например,
в
малоуглеродистой
стали
с
0,01
- 0,4 %
С
эта
ширина
примерно
в
8
раз
больше
среднего
значе
ния
СРТУ
за
цикл.
Различают
вязкие
и
хрупкие.
усталостные
бороздки.
В
первых
наблюдается
чередование
выступов
и
впадин,
формирующих
ха
рактерный
пилообразный
профиль
излома.
Иногда
между
вязки
ми
микрополосами
видны
следы
пластической
деформации.
Хруп
кие
бороздки
чаще
всего
образуются
на
фоне
речного
узора,
ха
рактерного
для
разрушения
сколом
(см.
гл.
IV).
При
этом
линии
речного
узора
примерно
перпендикулярны
бороздкам.
Помимо
Рис.
] 86.
Модель
пластического
притуп
ления
веРШИНbI
усталостной
треШИНbI
(Лэйрд,
Смит)
348
«чисто»
хрупких
И
вязких
микро
полос,
В
структуре
реальных
уста
лостных
изломов
встречается
мно
жество
промежуточных
по
виду
бороздок.
Предложены
десятки
моделей
развития
усталостных
трещин,
при
котором
образуются
бороздки
на
поверхности
разрушения.
Для
трак
товки
вязких
микрополос
наибо
лее
широко
используется
модель
пластического
притупления
верши
ны
трещины
Лэйрда
и
Смита
(рис.
186).
В
полуцикле
растяжения
у
вер
шины
трещины
(рис.
186,
а)
по
плоскостям
действия
максималь
ных
касательных
напряжений
идет
пластическая
деформация
(см.
рис.
186,
б).
По
достижении
cr
верши
на
трещины
приобрета'~~
форму
полукруга,
а
размер
пластической
зоны
достигает
Гр
(см.
рис.
186,
в).
При
смене
знака
напряжения
тре
шина
развивается
в
направлениях
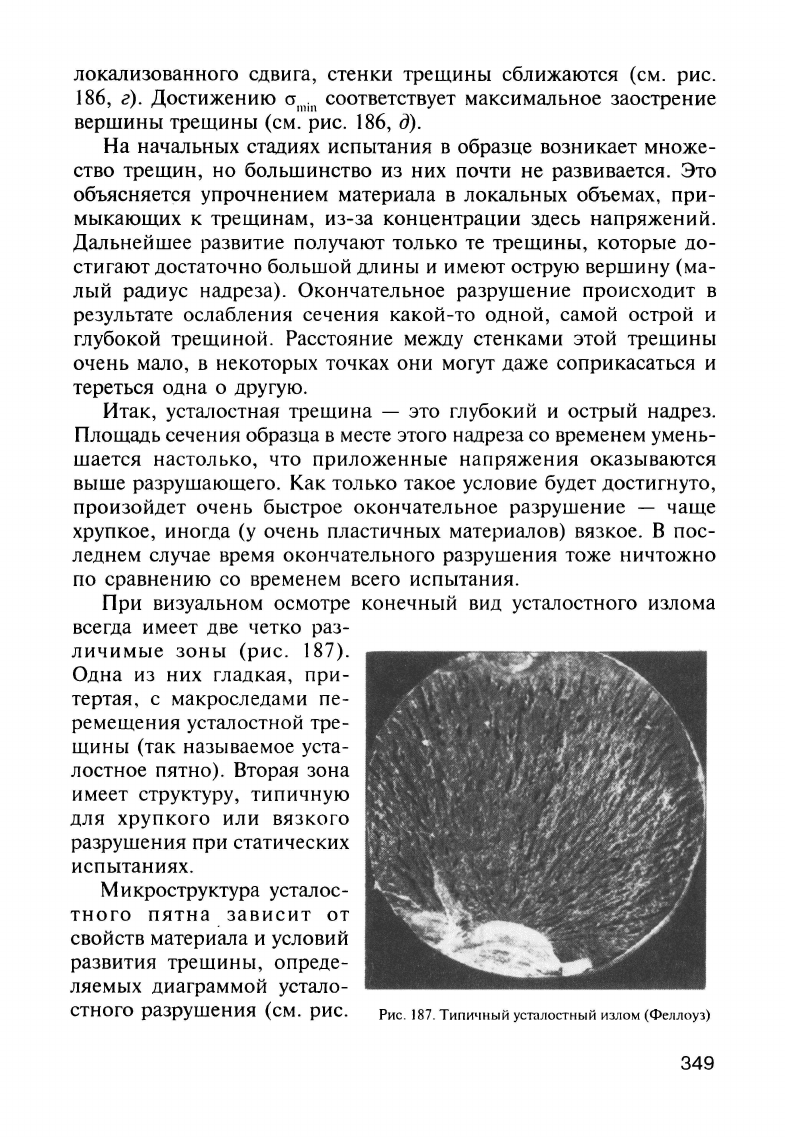
локализованного
сдвига,
стенки
трещины
сближаются
(см.
рис
.
186,
г).
Достижению
(J
.
соответствует
максимальное
заострение
111111
вершины
трещины
(см.
рис.
186,
д).
На
начальных
стадиях
испытания
в
образце
возникает
множе
ство
трещин,
но
большинство
из
них
почти
не
развивается.
Это
объясняется
упрочнением
материала
в
локальных
объемах,
при
мыкающих
к
трещинам,
из-за
концентрации
здесь
напряжений.
Дальнейшее
развитие
получают
только
те
трещины,
которые
до
стигают
достаточно
большой
длины
и
имеют
острую
вершину
(ма
лый
радиус
надреза).
Окончательное
разрушение
происходит
в
результате
ослабления
сечения
какой-то одной,
самой
острой
и
глубокой
трещиной.
Расстояние
между
стенками
этой
трещины
очень
мало,
в
некоторых
точках
они
могут
даже
соприкасаться
и
тереться
одна
о
другую.
Итак,
усталостная
трешина
-
это
глубокий
и
острый
надрез.
Площадь
сечения
образца
в
месте
этого
надреза
со
временем
умень
шается
настолько,
что
приложенные
напряжения
оказываются
выше
разрушаюшего.
Как
только
такое
условие
будет
достигнуто,
произойдет
очень
быстрое
окончательное
разрушение
-
чаще
хрупкое,
иногда
(у
очень
пластичных
материалов)
вязкое.
В
пос
леднем
случае
время
окончательного
разрушения тоже
ничтожно
по
сравнению
со
временем
всего
испытания.
При
визуальном
осмотре
конечный
вид
усталостного
излома
всегда
имеет
две
tleTKo
раз-
личимые
зоны
(рис.
187).
Одна
из
них
гладкая,
при
тертая,
смакроследами
пе
ремещения
усталостной
тре
щины
(так
называемое
уста
лостное
пятно).
Вторая
зона
имеет
структуру,
типичную
для
хрупкого
или
вязкого
разрушения
при
статических
испытаниях.
Микроструктура
усталос
тного
пятна
зависит
от
свойств
материала
и
условий
развития
трешины,
опреде
ляемых
диаграммой
устало
стного
разрушения
(см.
рис.
Рис
.
187
.
ТИПИ'IНЫЙ
УСТШIOСТНЫЙ
излом
(Феллоуз)
349