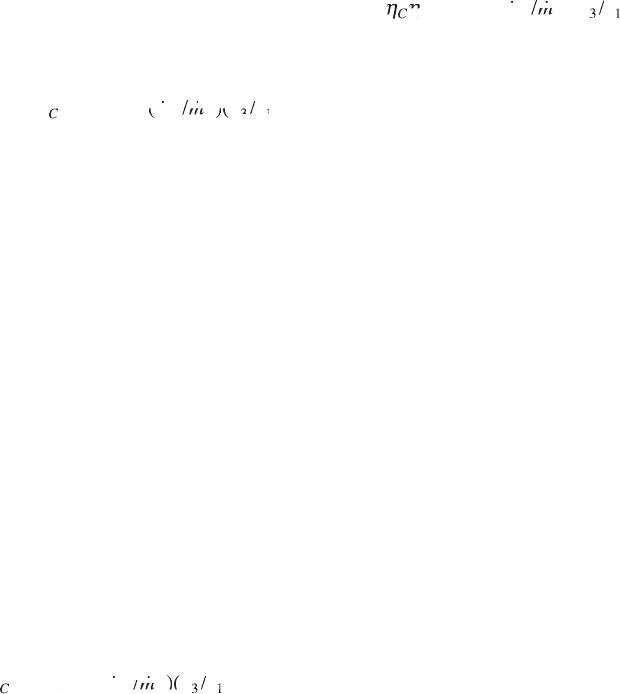
330 Diesel engine system design
© Woodhead Publishing Limited, 2011
ow turbines) for generating the engine air ow by the turbine. Substituting
4.40 into 4.47, the parametric dependency of engine delta P (p
3
– p
2a
) can
be re ected by 4.47 and 4.57. With the engine air ow rate and the EGR
rate as known target inputs (or equivalently the intake manifold pressure
p
2a
and the EGR rate as known targets by using 4.40), when T
3
and p
4
are
constant, if the turbine area A
T
varies, the exhaust manifold pressure p
3
changes according to 4.57. Thus, a change in p
2
,
TC
mm
TC
()
TC
mm
TC
//
TC
mm
TC
()
TC
mm
TC
TT()TT//TT()TT
31
TT()TT//TT()TT
or p
4
is required in order to balance the equation in 4.47. Therefore, the
parameters that can reduce the engine delta P (i.e., minimize p
3
at a given
p
2a
) are shown directly in 4.47 and 4.57. These parameters are: p
1
, p
2
, the
term
TC
mm
TC,3TC
mm
TC
()
TC
mm
TC,3TC
mm
TC
TC,3TC
()
TC,3TC
/
TC,3TC
()
TC,3TC
mm
,3
mm()mm
,3
mm/mm
,3
mm()mm
,3
mm
TC
mm
TC,3TC
mm
TC
()
TC
mm
TC,3TC
mm
TC
/
TC
mm
TC,3TC
mm
TC
()
TC
mm
TC,3TC
mm
TC
, p
4
, and A
T
. Note that the compressor
inlet temperature T
1
is affected by ROA. The compressor inlet pressure
p
1
is affected by the degree of ow throttling at the compressor inlet. The
compressor outlet pressure p
2
is affected by engine speed, volumetric ef ciency
(especially valve timing), effective engine displacement and intake manifold
temperature, as shown in equation 4.40. The pressure p
2
is also affected by
charge air cooler ow restriction and intake throttle as shown in equation
4.56. The turbine inlet temperature T
3
is affected by cylinder cooling and
heat losses from the exhaust port and the exhaust manifold, as shown in
equation 4.39. T
3
is also affected by the air–fuel ratio. The turbine ow rate
is affected by turbine wastegate opening. The turbine outlet pressure p
4
is affected by aftertreatment exhaust restriction C
d,exh
as shown in equation
4.43. The turbocharger ef ciency h
C
h
T
h
TC,mech
and the turbine area A
T
are
turbocharger design parameters.
EGR circuit ow restriction also affects engine delta P and other system
design parameters. In a HPL EGR system, the EGR circuit ow restriction
coef cient C
d,EGR
(or lumped EGR valve opening) can be solved using
equation 4.44 when p
3
– p
2a
and the EGR ow rate are known. On the other
hand, at a xed air ow rate and EGR rate (or equivalently, at a xed EGR
mass ow rate), when the EGR circuit ow restriction is also xed, p
3
must
be calculated using equation 4.44. Then the turbine area A
T
needs to change
according to equation 4.57, and simultaneously another change is required
in one of the following in order to balance equation 4.47: p
1
, p
2
, the term
TC
mm
TC
//
TC
mm
TC
()
TC
mm
TC
//
TC
mm
TC
TT//TT()TT//TT
31
TT//TT()TT//TT
, or p
4
.
Using the model of exhaust manifold gas temperature as shown in equation
14.4 in Chapter 14, the factors affecting the cycle-average engine delta P
are obtained by solving equations 4.40, 4.47, and 4.57. Figure 4.5 illustrates
that the following design may reduce engine delta P at a given speed–load
mode and xed targets of air–fuel ratio and EGR rate: higher turbocharger
ef ciency, higher exhaust manifold gas temperature, less turbine wastegating,
lower exhaust restriction pressure drop, and lower charge air cooler pressure
drop. It is also observed that at higher engine load (fueling rate), engine delta
P becomes higher. It is worth noting that in some engine designs with reed
Diesel-Xin-04.indd 330 5/5/11 11:47:41 AM