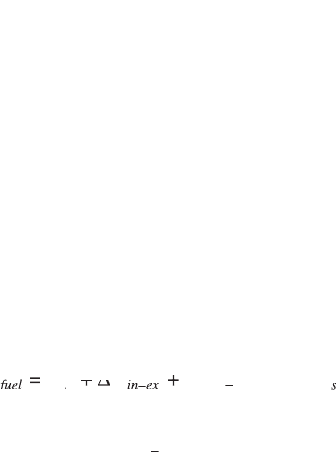
322 Diesel engine system design
© Woodhead Publishing Limited, 2011
while volumetric ef ciency is related primarily to the designs of cylinder
head, valvetrain, and manifolds.
The system of equations governing the steady-state engine performance
is derived below. Starting with a simpler example of the naturally aspirated
non-EGR engine (Fig. 4.3(a)), at a given engine speed, fuel rate, and brake
power, the four unknowns to be solved are the engine air ow rate
,
the exhaust manifold gas temperature T
3
, the inlet pressure p
1
, and the
exhaust manifold pressure p
3
. T
3
can be solved based on the engine energy
balance of thermodynamic rst law. The air ow rate
is solved based
on the de nition of engine volumetric ef ciency by assuming the volumetric
ef ciency is a known value. The pressure p
1
is solved by using the intake
ow restriction characteristics (i.e., a curve of pressure drop vs. volume
ow rate). The pressure p
3
is solved by using the exhaust ow restriction
characteristics.
For turbocharged EGR engines (Fig. 4.3(b) and (c)), the situation is
much more complex. At a given engine speed, fuel rate and brake power,
assuming the turbo characteristics (turbo maps) are known, there are 18
unknowns to be solved:
,
T
3
, p
4
, T
1,ROA
, p
1
, p
2
, T
2
, p
3
, T
4
, N
C
,
N
T
, h
C
, h
T
, p
2a
, T
2a
(for the high-pressure-loop EGR system) or T
1
(for the
low-pressure-loop EGR system), T
CACout
,
and T
EGRcoolerGasOut
. The detailed
explanation of the high-pressure loop and low-pressure loop EGR systems
is provided in Chapter 13 and Fig. 13.4. The engine delta P is p
3
– p
2a
. In
order to understand the system performance, a set of 18 equations is formed
(equations 4.39–4.56) based on the thermal, ow or ef ciency characteristics
of each element or device. It should be noted that the formulated equations
also serve as a foundation for developing future real-time model-based
algorithms in advanced electronic controls.
Unlike using the detailed differential equations of the in-cylinder cycle
process (equations 4.7, 4.10 and 4.12) for high- delity modeling, the engine
in the air system circuit is treated as a single lumped element here in terms
of energy balance so that the exhaust enthalpy or the exhaust manifold gas
temperature can be calculated by the following:
4.39
where
in-ex
is the rise in gas enthalpy rate from the intake manifold to
the exhaust manifold,
is the base engine heat rejection to the
coolant (if water cooled) or the cooling air (if air cooled), and
the miscellaneous heat losses, is treated as a known quantity here and is
detailed in Chapter 12. Equation 4.39 is used to solve for the exhaust
manifold gas temperature T
3
when the engine brake power
is assumed
to be known or calculated from equation 4.38.
It should be noted that the exhaust temperature measured by a thermocouple
is different from the time-averaged and the mass-averaged temperatures. This
Diesel-Xin-04.indd 322 5/5/11 11:47:32 AM