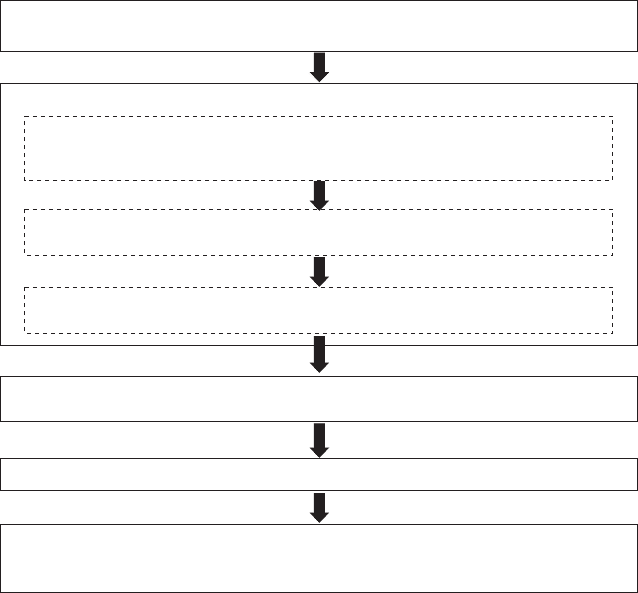
955Diesel engine system specification and subsystem interaction
© Woodhead Publishing Limited, 2011
the change in emissions target. A system design point can be selected based
on the best trade-offs between the tentative emissions target and the design
constraints from these analysis maps.
15.4.2 Subsystem interaction and optimization
In engine air system design, there are strong dependencies among the following
four parameters: exhaust restriction, EGR circuit ow restriction, turbine
effective area, and turbocharger efciency. In hardware selection at each
speed and load mode for a pair of target air–fuel ratio and EGR rate, when
the EGR valve is set fully open to minimize the engine delta P, the required
turbine area and turbocharger efciency are unambiguously determined (Table
4.1). But the reality is that the turbocharger efciency cannot reach all the
desirable values computed as such at all speeds and loads. At some modes,
if the actual turbocharger efciency is too low, the air–fuel ratio will become
System engineers receive air system requirements (intake manifold temperature, A/F,
EGR rate, fuel injection timing) from combustion emissions testing at minimum BSFC
System engineers conduct simulation types of A, B and C analyses to define air system
Type A: Study subsystem interaction at fixed NO
x
and soot target, and optimize
hardware requirements at critical speeds/loads. Sequence of selection: cooler
size, EGR circuit flow restriction, exhaust restriction, turbocharger. Determine
baseline values of DoE factors for Type C.
Type B: Simulate subsystem interaction between EGR circuit restriction, turbocharger
and exhaust restriction with fixed EGR rate and moving A/F ratio, or vice versa.
Type C: Simulate system performance and hardware requirements at moving
emissions targets to check sensitivity to A/F ratio and EGR rate changes.
Give the air system definition/requirements to suppliers (turbocharger, aftertreatment,
EGR cooler, EGR valve, charge air cooler) to let suppliers propose subsystem designs
Review suppliers’ proposals and coordinate the conflicts in subsystem requirements
Review revised proposals from suppliers. Check engine performance with real turbo
maps in engine cycle simulation for steady-state modes and transients. If the turbo is
acceptable, finalize all suppliers’ requirements and order hardware. If not, revise it.
15.9 Process of engine system design to optimize subsystem
interaction.
Diesel-Xin-15.indd 955 5/5/11 12:07:07 PM