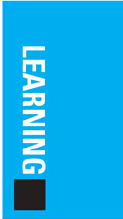
BUILDING EFFECTIVE TEAMS AND TEAMWORK CHAPTER 9 495
❏ Dana Corporation’s Minneapolis valve plant
trimmed customer lead time from six months
to six weeks.
❏ General Mills plants became 40 percent more
productive than plants operating without
teams.
❏ A garment-making plant increased its pro-
ductivity 14 percent by adopting a team-based
production system.
Table 9.1 reports the positive relationships
between employee involvement in teams and several
dimensions of organizational and worker effectiveness.
Lawler, Mohrman, and Ledford (1995) found that
among firms that were actively using teams, both
organizational and individual effectiveness were above
average and improving in virtually all categories of per-
formance. In firms without teams or in which teams
were infrequently used, effectiveness was average or
low in all categories.
Of course, a variety of factors can affect the per-
formance and usefulness of teams. Teams are not
inherently effective just because they exist. A Sports
Illustrated cover story, for example, labeled the Los
Angeles Clippers NBA basketball team the worst team
in the history of professional sports from inception
to the year 2000 (Lidz, 2000)—evidence that just
because a group of talented people get together does
not mean that an effective team can be created.
Hackman (1993) identified a set of common inhibitors
to effective team performance, including reward-
ing and recognizing individuals instead of the team,
not maintaining stability of membership over time, not
providing team members with autonomy, not fostering
interdependence among team members, and failing to
orient all team members. In contradiction to Peters’
comments about the universal utility of teams,
Verespei (1990) observed:
All too often corporate chieftains read the suc-
cess stories and ordain their companies to
adopt work teams—NOW. Work teams don’t
always work and may even be the wrong solu-
tion to the situation in question.
The instrument, called “Diagnosing the Need for
Team Building” in the Skill Assessment section of this
chapter, helps identify the extent to which the work
teams in which you are involved are performing effec-
tively, and the extent to which they need team building.
Often, teams can take too long to make decisions, they
can drive out effective action by becoming too insular,
and they can create confusion, conflict, and frustration
ability to lead and manage teams and teamwork, in
other words, has become a commonplace requirement
in most organizations. In one survey, the most desired
skill of new employees was found to be the ability to
work in a team (Wellins, Byham, & Wilson, 1991).
One noted management consultant, Tom Peters
(1987), even asserted:
Are there any limits to the use of teams? Can we
find places or circumstances where a team
structure doesn’t make sense? Answer: No, as
far as I can determine. That’s unequivocal, and
meant to be. Some situations may seem to lend
themselves more to team-based management
than others. Nonetheless, I observe that the
power of the team is so great that it is often wise
to violate apparent common sense and force a
team structure on almost anything. (p. 306)
One reason for the escalation in the desirability of
teamwork is that increasing amounts of data show
improvements in productivity, quality, and morale when
teams are utilized. Many companies have attributed
their improvements in performance directly to the insti-
tution of teams in the workplace (Cohen & Bailey, 1997;
Guzzo & Dickson, 1996; Hamilton, Nickerson, &
Owan, 2003; Katzenbach & Smith, 1993; Senge, 1991).
For example, by using teams in their organizations:
❏ Shenandoah Life Insurance Company in
Roanoke, Virginia, saved $200,000 annually
because of reduced staffing needs, while
increasing its volume 33 percent.
❏ Westinghouse Furniture Systems increased
productivity 74 percent in three years.
❏ AAL increased productivity by 20 percent, cut
personnel by 10 percent, and handled 10 percent
more transactions.
❏ Federal Express cut service errors by 13 percent.
❏ Carrier reduced unit turnaround time from
two weeks to two days.
❏ Volvo’s Kalamar facility reduced defects by
90 percent.
❏ General Electric’s Salisbury, North Carolina,
plant increased productivity by 250 percent
compared to other GE plants producing the
same product.
❏ Corning cellular ceramics plant decreased defect
rates from 1,800 parts per million to 9 parts per
million.
❏ AT&T’s Richmond operator service increased
service quality by 12 percent.