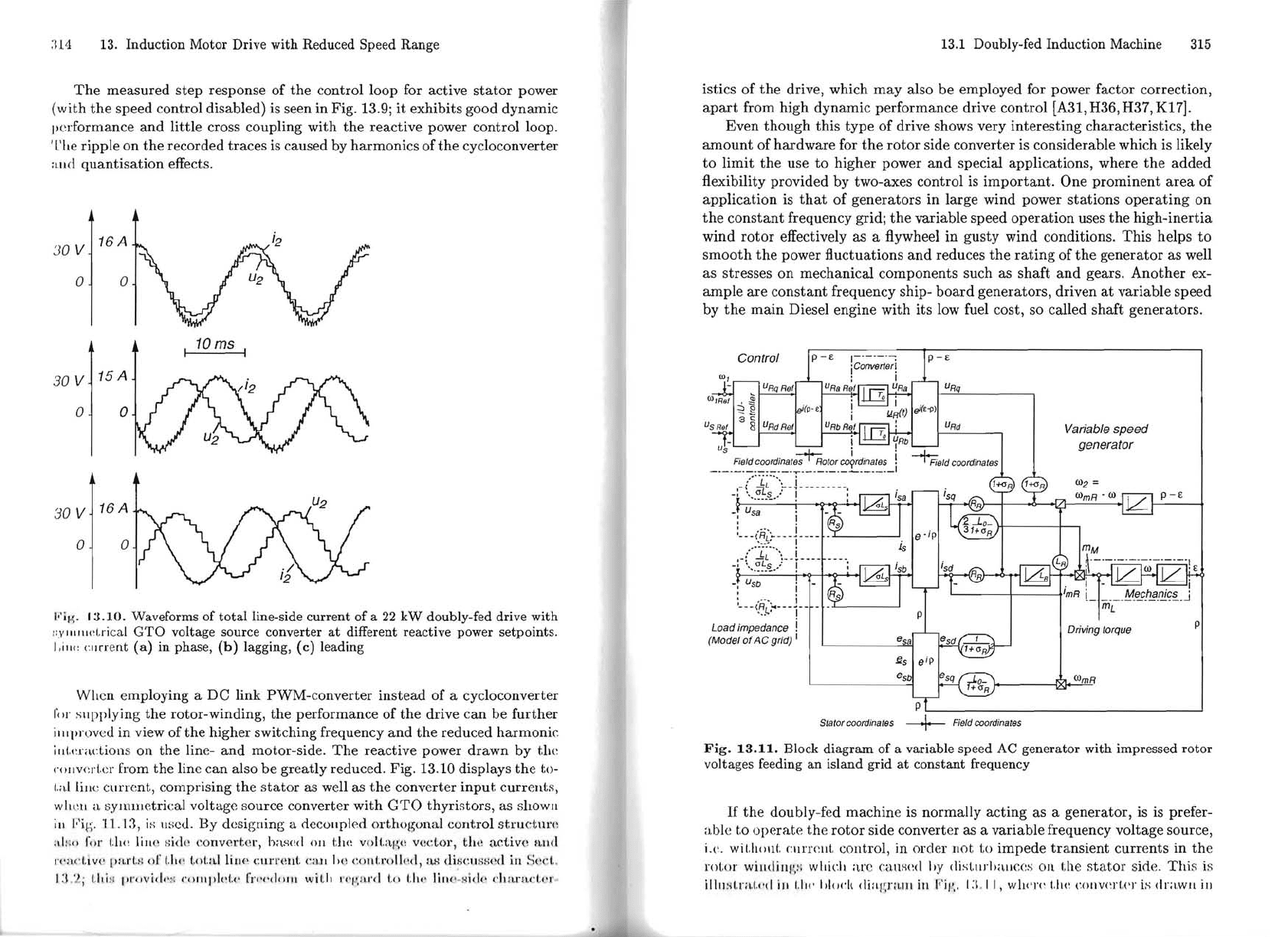
:
H4
13.
Induction
Motor
Drive
with
Reduced
Speed
Range
The
measured
step
response
of
the
control loop for active
stator
power
(with
the
speed control disabled) is seen in Fig. 13.9j
it
exhibits good dynamic
pcrformance
and
little cross coupling with
the
reactive power control loop.
'l'he ripple
on
the
recorded traces is caused by
harmonics
of
the
cycloconverter
a.lI(!
quantisation
effects.
30
V'
16 A
OJ
O
1
10ms
1
30 V 115 A
OJ
O
30 V I 16 A
OJ O
I"i
r.:;
. I:J.10. Waveforms of
totalline-side
current
of
a
22
kW
doubly-fed drive
with
::Y
"IIII<'I.ri
ca
l
GTO
voltage source converter
at
different reactive power setpoints.
I.ill
<:
C1ment
(a)
in
phase,
(b)
lagging,
(c)
leading
Whcn employing a
De
link
PWM-
converter
instead
of
a cycloconverter
for
sllpplying
the
rotor-winding, the performance
of
the
drive c
an
be
further
illlproved in view of
the
higher switching frequency
and
the
reduced
harmonk
illt.(~raction
s
on the line-
and
motor-side.
The
reactive power drawn
by
tlw
collverl.er from the line
ca
n also
be
greatly
reduced. Fig. 13.10 displays
the
to-
t.
al
Iill!:
currcnt, comprising the
stator
as well as
the
conve
rter
input
currents,
Wll
C
lI
a sYlfunetrical volt age source converter with
GTO
thyristors, as s
howl1
i
II
ICi
g. 11. I
:3,
is
used. By designing a decollpled orthogonal control
stnl(:tlln~
;d
liO for
(.jl<~
líH
e side
co
nv
erte
r,
ha:wr!
OH
tJl<~
v()lt,:q
~
(
~
vector,
th(~
active
fUld
l"C
°ndi
VI'
p:
....
't
.K
0
1'
t.Il(
~
t.ot.nlliJl(
~
Cllrr(~I1t.
c;t.u
h(~
e
Olltl'oll(
~
d,
as
di
:
~ct
H
;se
d
il1
S
oei.
.
r:!:
.!.j
I.hi
!1
1'
I'
lJ
vid.
,:;
('o"lpld('
[n
'
('d""1
wit
\h
1 '
('
I
~n
,
l'd
t.o
1.111'
liIH
Hlíd., chnrad .• 'r.
13.1 Doubly-fed
Induction
Machine 315
istics
of
the
drive, which
may
also
be
employed for power factor correction,
apart
from high dynamic performance drive control [A31, H36, H37, K17].
Even
though
this
type
of
drive shows very interesting characteristics,
the
amount
of
hardware
for
the
rotor
si de converter is considerable which is likely
to
limit
the
use
to
higher power
and
special applications, where
the
added
flexibility provided by two-axes control is
important.
One
prominent
area
of
application
is
that
of
generators
in
large wind power
stations
operating
on
the
constant
frequency gridj
the
variable speed
operation
uses
the
high-inertia
wind
rotor
effectively as a flywheel
in
gusty
wind conditions.
This
helps
to
smooth
the
power fluctuations
and
reduces
the
rating
of
the
generator
as well
as stresses
on
mechanical components such as
shaft
and
gears.
Another
ex-
ample
are
constant
frequency ship-
board
generators, driven
at
variable
speed
by
the
main
Diesel engine with its low fuel cost, so called shaft generators.
Contrai
p-ê
p-ê
w,
URq
URd
Variable speed
generator
, i
,-
:_--(~~;-.--+-
p
Load
impedance j
Driving forque
(Mo dei
of
AG
grid) I
OlmR
p
~'-------------------------------------------'
S/a/or coordina/8S
--+--
Field coordina/8s
Fig.
13.11.
Block
diagram
of
a variable speed AC
generator
with
impressed
rotor
voltages feeding
an
island grid
at
constant
frequency
If
the
doubly-fed machine is normally
acting
as a generator, is is prefer-
able
to
operate
the
rotor
side converter as a variable frequency volt age source,
i.(·.
wit.ll<llll
,
CIIIT
(!
llt.
control, in order not to
impede
transient
currents
in
th
e
rot.or
Willdil1f',:;
wllich are
c
a.
lul(
~
d
hy díst.llrh:wces OH the
stator
side.
Thi
s is
illll:it.r;d .•
'd
iII LlI('
I"ud
t diaf
!;
r:l.Il1
iII
,I,'il',.
1:
1.
11,
Wh('JT
t.\\(
~
('.ollvnt.(·]"
is
drawll
jlJ