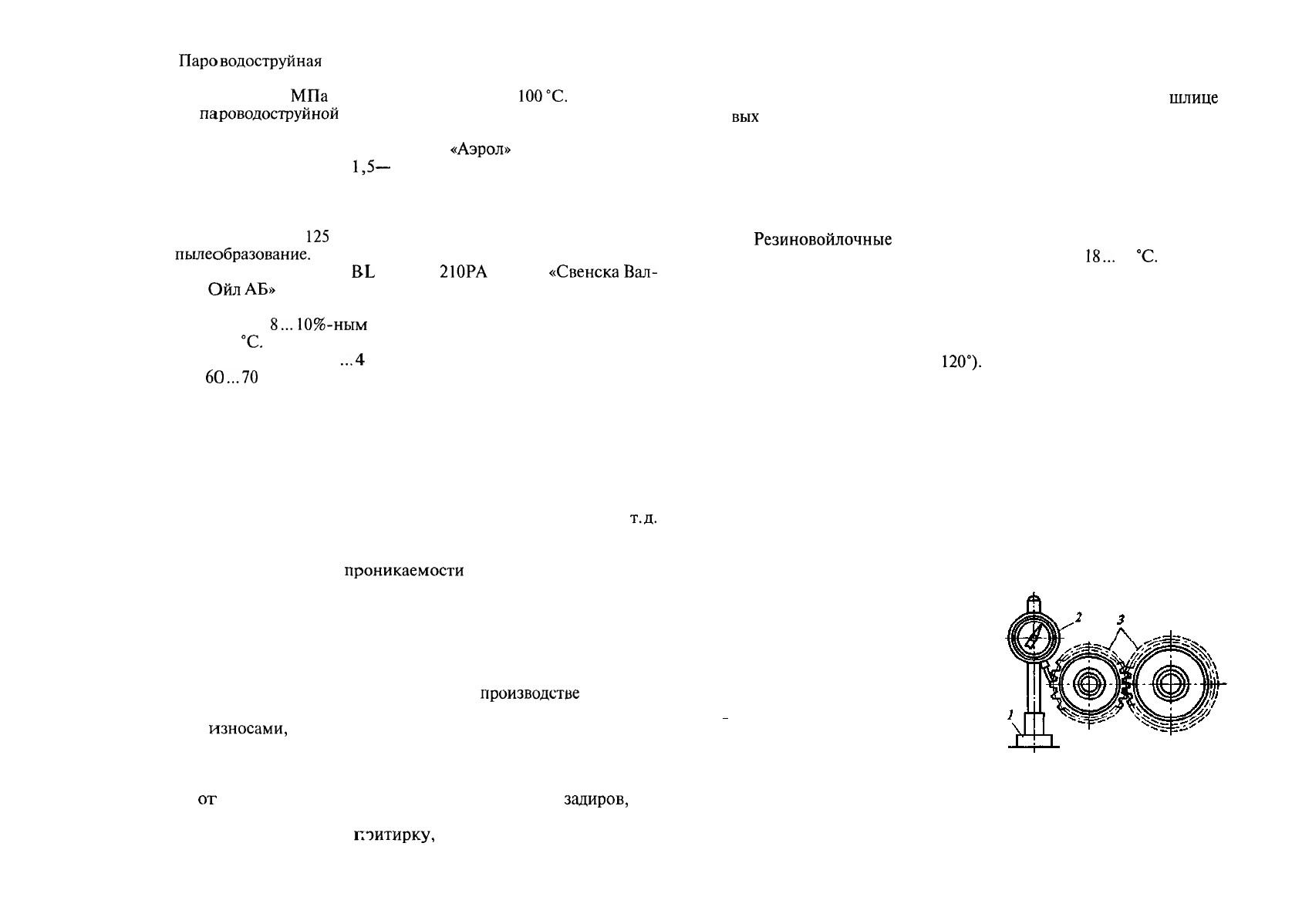
Пароводоструйная
очистка деталей и агрегатов заключается в
том, что на очищаемую поверхность подается пароводяная струя
под давлением 2
МПа
и при температуре 90...
100°С.
Эффектив-
ность
пароводоструйной
очистки деталей зависит от энергии струи,
температур и активности моющих средств. Испытания показали,
что применение моющих средств типа
«Аэрол»
в 2 раза сокращает
время очистки деталей и в
1,5
—
2 раза снижает ее стоимость. Струй-
ная очистка кварцевым песком обеспечивает эффективное удале-
ние с деталей ржавчины, старой краски, окалины. Обработка вы-
полняется без применения сжатого воздуха струей песка высокой
скорости (не менее
125
м/с). Применение мокрого песка исключа-
ет
пылеобразование.
Для струйной обработки деталей мокрым пес-
ком применяют агрегаты
BL
210, BL
210PA
фирмы
«Свенска
Вал-
волин
Ойл
АБ»
(США).
Очистка от накипи чугунных деталей производится промыва-
нием деталей
8...10%-ным
раствором соляной кислоты, нагре-
тым до 70
°С.
Для предохранения деталей от коррозии в раствор
добавляют уротропин (3
...4
г на 1 л). Продолжительность обработ-
ки —
60...70
мин. Затем двигатель необходимо промыть чистой
водой с добавлением хромпика. Внутренние поверхности газопро-
водов двигателей очищают металлическим скребком или ершом,
а затем промывают керосином и продувают сжатым воздухом.
Очищенные и обезжиренные детали сортируют на годные без
восстановления, подлежащие ремонту и негодные. Контроль осу-
ществляется как визуально, с проверкой геометрических размеров
мерительным инструментом, так и с использованием дефектоско-
пов для обнаружения скрытых дефектов трещины, раковины и
т.д.
Дефектоскопия использует для обнаружения скрытых дефек-
тов: магнитный метод для металлических деталей, капиллярный
метод, основанный на
проникаемости
специальных растворов,
методы гидравлического или пневматического опрессования, уль-
тразвуковой метод, основанный на свойстве ультразвука прохо-
дить через металлические изделия и отражаться от границы разде-
ла двух сред, в том числе и от дефекта.
Сборка является завершающим этапом ремонта агрегатов ав-
томобиля. От ее качества зависят надежность и долговечность ра-
боты агрегатов и систем. В авторемонтном
производстве
при сбор-
ке используют детали с измененными размерами или с допусти-
мыми
износами,
поэтому процессу сборки предшествуют комп-
лектовочные работы, при которых вместо выбракованных деталей
используют новые или отремонтированные из оборотного фонда.
При сборке рабочую поверхность детали необходимо предохра-
нить
от
попадания абразивных частиц, образования
задиров,
за-
усенцев и т.д. При комплектовании деталей иногда выполняют
припиловку, шабрение,
поитирку,
полировку, развертывание,
прогонку резьбы.
Процесс сборки непосредственно состоит из последовательно
выполняемых работ по подсборке типовых соединений, цилиндри-
ческих и конических шестерен, конусных, шпоночных,
шлице
-
вых
соединений, шариковых и роликовых подшипников и др. Пе-
ред сборкой детали необходимо промыть в специальном растворе:
стальные и чугунные — на 100 л воды 0,3 кг нитрита и 1 кг каль-
цинированной соды; алюминиевые — на 100 л воды 0,25 кг каль-
цинированной соды, 0,2 кг хромпика, 0,3 кг жидкого стекла. Пос-
ле мойки детали перед сборкой обдувают сухим сжатым возду-
хом, трущиеся поверхности смазывают тонким слоем масла.
Резиновойлочные
сальники перед установкой выдерживают
30 мин в жидком масле, имеющем температуру
18...
20
°С.
Для пре-
дохранения рабочих кромок сальников от повреждения при ус-
тановке деталей в узел, где стоит сальник, применяют оправки.
При сборке цилиндрических шестерен зазор между зубьями
шестерен проверяют с помощью щупа, прокатыванием свинцо-
вой пластинки или индикатором. Зазор измеряют в трех местах
венца шестерни (под углом
120°).
На основании результатов изме-
рения определяют средний зазор. Более точные значения боково-
го зазора между зубьями шестерен получаются при прокатывании
свинцовой пластинки. После прокатки замеряют ее толщину мик-
рометром и по результатам измерения устанавливают величину
зазора между зубьями шестерен.
Боковой зазор между зубьями можно определить индикато-
ром (рис. 12.2). Мерительный наконечник индикатора устанавли-
вают на зубе первой шестерни, которая находится в зацеплении
с сопряженной шестерней. Поворачивая первую шестерню (вто-
рая застопорена), выбирают зазор между зубьями и одновремен-
но следят за отклонением стрелки индикатора. Разность показа-
ния индикатора составит величину зазора между зубьями сопря-
женных шестерен. При неравно-
мерном зазоре следует устано-
вить, какая из шестерен имеет
дефект. Для этого сначала находят
наименьший зазор между зубь-
ями шестерен, а затем их разъ-
единяют. Одну из шестерен по-
ворачивают на 180° и снова со-
единяют. Если после этого харак-
тер зацепления не изменился,
значит, дефект имеет та шестер-
ня, которая оставалась непо-
движной. Если до поворота шес-
терни зазор между зубьями имел
минимальную величину, а после
поворота стал максимальным, то
Рис. 12.2. Измерение индикатором
зазора между зубьями цилиндри-
ческих шестерен:
/ — стойка; 2 — индикатор; 3 —
шестерни
82
83