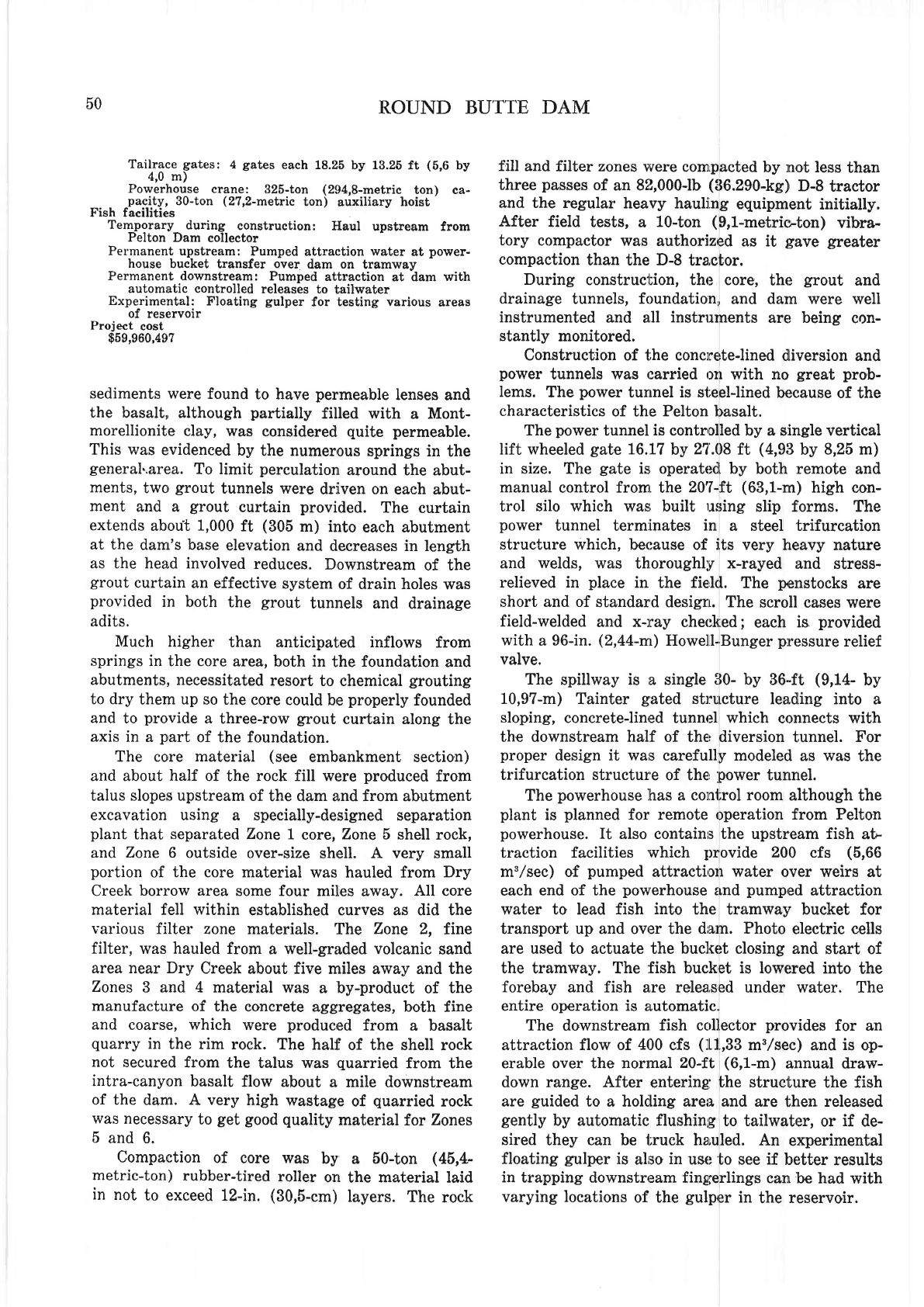
50
ROUND BUTTE
DAM
Tailrace
gates:
4
gates
each
18.25 by 13.26
ft
(5,6
by
4,0 m)
Powerhouse
erane:
325-ton
(294,8-metric
ton) ca-
-pa.c_ity,
30-ton
(Z?,Z-metric
ton)
auxiliary hoist
Fish facilities
Temporary_
during-
construction:
Ilaul
upstream from
Pelton
Dam
collector
Permanent
upstream:
Pumped
attraction
water
at
power-
house
bucket
transfer
over
dam
on
tramway
Permanent
downstream: Pumped
attraction
at dam
with
automatic
controlled
releases to
l;ailwater
Experimental:
Floating
gulper
for
testing various
are&s
of reservoir
Project
cost
$59,960,49?
sediments
were
found
to have
permeable
lenses
and
the basalt,
although
partially
filled with
a Mont-
morellionite clay,
was
considered
quite
permeable.
This
was
evidenced
by
the rurr€rous
springs in
the
general..area.
To limit
perculation
around
the abut-
ments,
two
grout
tunnels
were
driiven
on
each
abut-
ment
and a
grout
curtain
provided.
The
curtain
extends
about
1,000
ft
(305
m) into
each abutment
at the
dam's
base
elevation
and
decreases in length
as the head involved
reduces.
Downstream
of the
grout
curtain
an effective
system
of drain holes
was
provided
in both
the
grout
tunnels and
drainage
adits.
Much
higher
than anticipat,ed inflows
from
springs in
the core
area, both
in
the
foundation
and
abutments, necessitated
resort
to chemical
grouting
to dry
them up so
the
core
could
bra
properly
founded
and to
provide
a
three-row
grout
curtain along
the
axis
in a
part
of the
foundation.
The core material
(see
embankment section)
and
about
half
of
the
rock fill were
produced
from
talus
slopes upstream
of
the dam a'nd from abutment
excavation using a specially-designed
separation
plant
that
separated Zone
1
core,
Zone 5 shell
rock,
and
Zone 6
outside
over-size
shrell.
A very small
portion
of
the core material
was hauled from
Dry
Creek
borrow area
some four
mil,es away.
All core
material fell within
established curves as did
the
various
filter zone
materials.
lthe
Zone
2,
fine
filter,
was hauled from
a
well-graded volcanic
sand
area
near Dry
Creek about five
miles awa.y
and
the
Zones
3 and 4 material
was
a
'by-product
of
the
manufacture
of
the
concrete aggregates, both
fine
and
coarse,
which
were
producred
from
a basalt
quarry
in
the rim
rock.
The halil
of the shell
rock
not secured
from
the talus
qTss
eu&rried
from
the
intra-canyon
basalt
flow
about
a mile downstream
of the
dam. A very
high
wastage
of
quarried
rock
was
necessary
to
get
good
quality
material
for
Zones
5
and 6.
Compaction
of
core was
by
a
50-ton
(45,4-
metric-ton)
rubber-tired
roller
on
the
material laid
in
not
to
exceed
12-in.
(30,5-cm)
layers.
The
rock
fill
and filter zones
vyere
comrpacted
by lnrof, l.w
than
three
passes
of
an 821,000-lb
(i|6.290-ks)
D-8
traetor
and
the regular
heavy hauliing
equipment
initially.
After
field
tests,
a
10-ton
(9,1-metrie.ton)
vibra-
tory compactor
was
authorizred
as it
gave
greater
compaction
than the D-8
tra;ctor.
During
construclbion, the core,
the
grout
drainage
tunnels,
foundatio,n,,
and darn were
instrumented
and
a,ll
instnrrnents
are being
stantly
monitored.
and
well
con-
Construction
of
t;he
concreteJined
dli'version and
power
tunnels
was earried
on with no
great prob-
lems.
The
power
tunnel
is st;eelJined
txrcause
of
the
characteristics
of the
Pelton
basalt.
The
power
tunnel
is
contr,olled by a s;ingle vertical
lift wheeled
gate
16.17
by
2?'.08
ft
(4,93
by
8,25 m)
in size.
The
gate
is; operatedl
by both remote
and
manual
control
frorrrr
the
20'I-ft
(63,1-nn)
high
con-
trol silo which was built
rnsing
slip florms. The
power
tunnel term:inates
in
a steel trifurcation
structure which,
because of
iits
very heavy
nature
and
welds,
was
thoroughl;7
x-rayed
and stress-
relieved in
place
in
the
fieilcl.
The
pe:nstocks
are
short and of
standard design. The
scroll
cases were
field-welded
and
x-lray
check:ed;
each
is.
provided
with
a
96-in.
(2,44-nr)
Howel,l-Bunger
prressure
relief
valve.
The
spillway is a single
If0-
by 36-f't
(9,14-
by
10,97-m)
Tainter
g'ated
structure
lea,dling into
a
sloping,
concrete-linred tunnel which
connects with
the downstream half of ther diversion
t;unnel.
For
proper
design
it wars
carefull;y modelecl
as
was
the
trifurcation structure
of ther
power
turrnel.
The
powerhouse
lhas a co:nl;rol
room
although the
plant
is
planned
for
remote
operation
llrom Pelton
powerhouse.
It
also
containrs the upstream fish
at*
traction
facilities
'which
provide
200
cfs
(5,66
m'/sec) of
pumped
attracti,on
water
over weirs at
each
end of the
powerhouse
ernd
pumpred
attraction
water to lead fish
into
the
tramway bucket for
transport up and ov(sr the
dam. Photo
electric
cells
are used to actuate the
bucket
closing
ernd start of
the tramway. The :fish
bucket is
lowered into
the
forebay
and fish
a,re
relea,sed under water.
The
entire operation is
euutomatic.
The
downstream
fish colliector
provides
for an
attraction flow of
400
cfs
(111.,33
m3lsec)
and
is
op-
erable over the
normal
20-ft
(6,1-m)
a:rnual draw-
down range.
After
entering:
bhe structure
the fish
are
guided
to a holcling area and
are
then
released
gently
by automatic flushinig
to tailwatrer,
or
if
de-
sired
they can be l;ruck haruled. An
experimental
floating
gulper
is
also
in
use'to see if
better
results
in trapping
downstrrsam finglerlings
can'be
had
with
varying locations
of the
gulprer
in
the
reservoir.