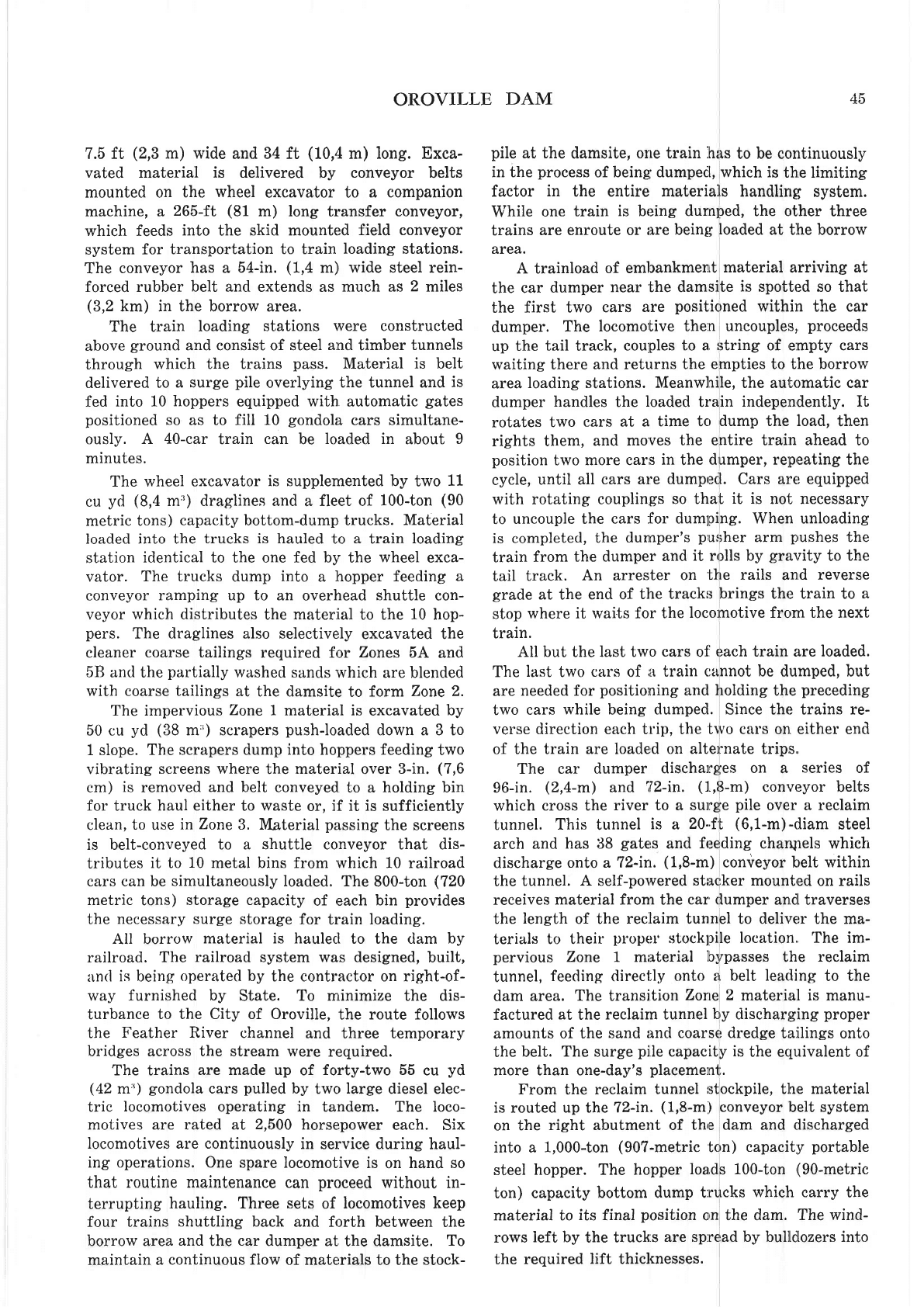
OROVILLE
DAM
45
7.5
ft
(2,3
m) wide
and 34 ft
(10,4
m) long. Exca-
vated material is delivered
by
conveyor
belts
mounted on
the
wheel
excavator to a
companion
machine, a
265-ft
(81
m) long
transfer
conveyor,
which feeds
into
the
skid mounterd
field conveyor
system
for transportation
to train
loading stations.
The
conveyor
has
a
54-in.
(1,4
m)
wide steel rein-
forced rubber
belt and
extends as
much as
2
miles
(3,2
km) in the borrow area.
The train
loading
stations
were constructed
above
ground
and consist of steel
arnd
timber
tunnels
through
which the trains
pass.
Material
is
belt
delivered
to
a surge
pile
overlying
the tunnel and
is
fed
into 10
hoppers
equipped with automatic
gates
positioned
so
as to fill 10
gondola
cars simultane-
ously.
A
40-car
train
can
be
loaded in
about
I
minutes.
The wheel
excavator
is supplemented by
two
11
cu
yd
(8,4
m") draglines and
a
fleet of
100-ton
(90
metric tons)
capacity
bottom-dump
trucks. Material
loaded into the
trucks is hauled
to
a
train
loading
station
identical to
the one
fed by
the
wheel
exca-
vator.
The trucks
dump
into
a
Jropper feeding
a
conveyor
ramping up to
an overhead
shuttle
con-
veyor
which
distributes
the
material
to the
10
hop-
pers.
The draglines also selectively
excavated the
cleaner
coarse tailings
required far
Zones
5A
and
58 and
the
partially
washed
sands
which are blended
with coarse tailings
at
the damsite
to
form
Zone 2.
The impervious
Zone
1 materia,l is
excavated
by
50 cu
yd
(38
m") scrapers
push-loaded
down a 3 to
1 slope.
The scrapers dump
into
hoppers
feeding
two
vibrating
screens
where
the
material
over
3-in.
(7,6
cm)
is
removed
and
belt conveyed
to a
holding
bin
for
truck
haul either
to
waste
or,
if it is sufficiently
clean,
to
use
in
Zone
3.
Material
pzrssing
the screens
is belt-conveyed
to a shuttle conveyor that dis-
tributes
it to
10
metal bins from
'which
10 railroad
cars can be
simultaneously
loaded. The
800-ton
(720
metric
tons)
storage capacity
of each
bin
provides
the
necessary surge
storage
for
train
loading.
All borrow
material is hauled
to the dam by
railroad.
The
railroad
system was designed,
built,
and
is being
operated by
the contractor on right-of-
way furnished
by
State.
To minimize
the dis-
turbance
to the City of Oroville,
the
route follows
the
Feather River
channel
and
three
temporary
bridges across the stream were
required.
The trains
are made up
of
forty-two 55
cu
yd
(42
m'')
gondola
cars
pulled
by
two
large
diesel elec-
tric
locomotives
operating
in
tandem. The loco-
motives are rated at
2,500
horsepower
each. Six
locomotives are continuously
in
service during haul-
ing operations. One
spare locomotive
is
on
hand so
that routine maintenance
can
proceed
without
in-
terrupting
hauling. Three sets
of
locomotives keep
four trains
shuttling back
and forth between
the
borrow arel"
and
the
car
dumper at
the
damsite.
To
maintain a continuous flow of materrials to the stock-
pile
at the
damsite,
one
train
lhas
to be continuously
in the
process
of
being: dumpecl, which
is
thLe limiting
factor
in
the
entire
materialls handlinll
system.
While
one
train
is
being
durnped,
the
ot;her
three
trains
are enroute or
are being
loaded
at the borrow
area.
A
trainload
of embankmenrt
material
arriving
at
the
car
dumper
nearbhe damsite
is
spottr:d so that
the
first two
cars
are
positioned
withirn
the car
dumper.
The
locomotive the:n
uncouplers,
proceeds
up
the
tail
track,
couples
to a string
of empty
cars
waiting there
and returns the
empties
to the
borrow
area
loading stations.
Meanwhile,
the automatic car
dumper
handles
the
loaded
train
indepe:ndently. It
rotates
two
cars at a
time to
dump the load,
then
rights them,
and
mo'ves
the entire train ahead to
position
two
more caris
in
the
dumper, re'peating
the
cycle,
until all
cars are
dumpeil.
Cars
ar:et equipped
with
rotating couplin,gs
so that
it is
nolb necessary
to
uncouple the
cars :for dumping. When unloading
is
completed,
the
dunnper's
prnsher
arm
prushes
the
train
from
the dumper
and
it rolls by
grarrity
to
the
tail
track.
An arrester
on
the rails
anLd
reverse
grade
at the
end of
the tracks
brings thr: train to
a
stop
where
it wai-ts for the
locornotive frorn the next
train.
All but
the
last two
cars
oli
each train are
loaded.
The
last
two
cars
of
n
train
cannot be dumped, but
are
needed for
positiorning
and
holding
the
preceding
two
cars
while
being dumped. Since the trains re-
verse direction eerch trip, the brvo cal's oni either end
of the train
are
loade,d
on altercnate trips,
The car
dumper
discharges
on
a
series
of
96-in.
(2,4-m)
and
'tr2-in.
(1.,13-m)
conrreyor belts
which
cross the
river to a
sur:eie
pile
over a
reclaim
tunnel.
This
tunnel
is
a
20-'ft
(6,1-m)-diam
steel
arch
and
has
38
gaters
and
feeding
charqrels whicli
discharge
onto a 72-in.
(1,8-m)
conveyor belt within
the
tunnel.
A
self-porvered
stilcker mounted
on rails
receives material from the
car dumper
anrcl traverses
the
length
of the
reclaim
tunnel to delirrerr the ma-
terials
to their
propet'
stockpile
location,,
The
im-
pervious
Zone 1 material
)bypasses
the
reclaim
tunnel,
feeding
direcl;ly
onto
ar belt leading
to the
dam
area. The transition
Zone 2
material is manu-
factured
at
the
reclairn tunnel
by
dischar:ging
proper
amounts of the
sand ilnd
coarse dredge
trailings
onto
the
belt.
The
surge
pi,le
capacity
is
the equivalent of
more than one-day's
placemenl,.
From
the
reclaim
tunnel
rstockpile,
tlhe
material
is routed up the
72-in.
(1,8-m,)
conveyor
belt
system
on
the
right abutmetrt of the
dam and discharged
into a
1,000-ton
(9O?-metric
ton)
capacit,y
portable
steel
hopper. The hopper
loa,ds 100-ton
(9O-metric
ton)
capacity bottom
dump t:rucks
which carry
the
material to
its
final
position
o,n the dam.
The wind-
rows
left by
the trucks
are sp:rerad by bul)titozers into
the required
lift
thicl<nesses.