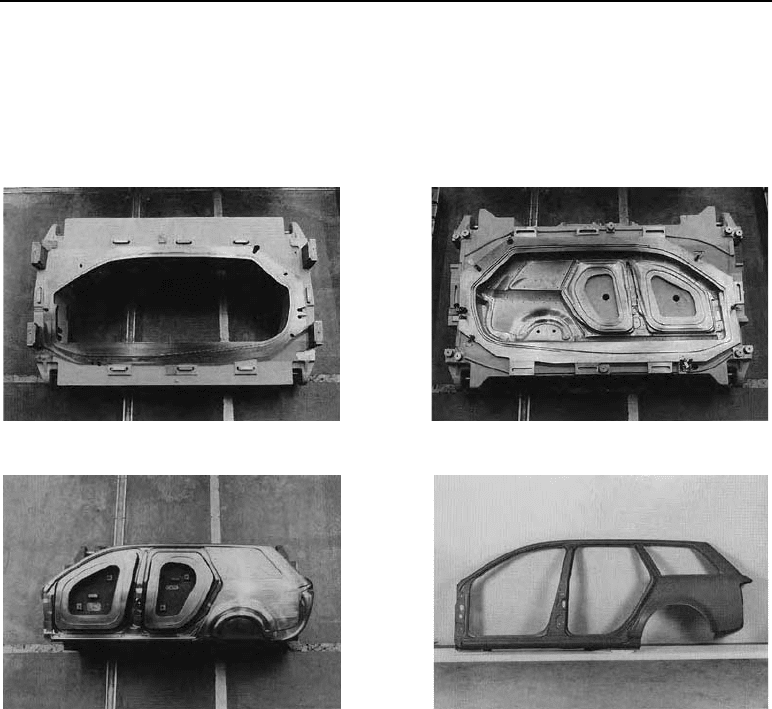
14.10 Drawing tooling (Figure 14.17) 163
The draw beads and lock beads mean that the material flow can be controlled, fine-tuned by
FEM simulation and ultimately the toolmaker’s experience, so that the defects of cracking,
over-reduction of sheet thickness and wrinkling can be avoided. Figure 14.28 shows the deep
drawing punch, the blank holder, the drawing die and a component, the side door of an Audi
Avant automobile.
Blank holder
Drawing die
Drawing punch
Side wall component of Audi Avant
Figure 14.28 Toolset for manufacturing the Audi Avant side wall (Photograph from KUKA Werkzeug-
bau Schwarzenberg GmbH works, Germany)
The problems presented by this complicated drawing tooling mean that in practice, when pre-
developing new automobile components, prototype tooling is still required to produce a limited
number of components for test purposes, as well as FEM simulations of the viability of the
process and the construction of tooling.
In Figure 14.29, for example, there are three toolsets for manufacturing prototype components
which allow rapid production of the tooling, and therefore also the workpieces, from 3D CAD
construction data. In version 1, the tooling is produced by casting using an alloy with a very
low melting point, MCP 137 (HEK GmbH works). This tooling can be used for up to approx.
30 parts, then it must be re-cast with the nearly 100% reusable MCP alloy. For larger numbers
of prototype parts, a Zn alloy (ZAMAK) is used internationally which requires full mould
casting followed by a chip-producing finishing process.