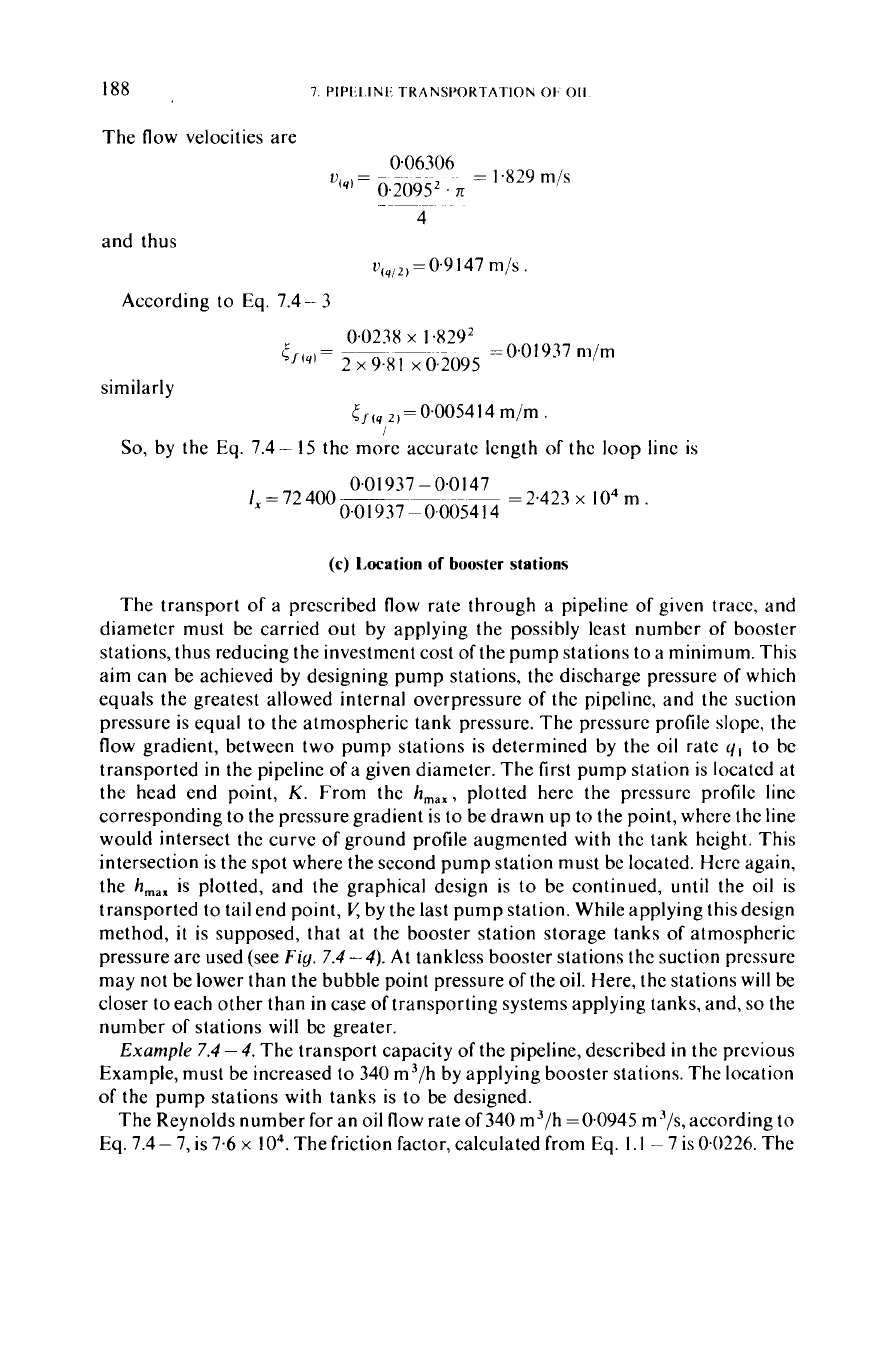
I88
7.
PIPl:l.INl~
TKANSI'OK'IATION
Ot-
011
The flow velocities are
and thus
4
~1,~~~)
=
0.9
I
47 m/s
According to
Eq.
7.4
-
3
0.0238
x
1.8292
2
x
9.8
I
x
0,2095
=
0.0
I937 m/m
c/w=
~~ ~~ ~
similarly
tfIq
,,=0.005414 m/m.
/
So,
by the
Eq.
7.4-
15
the more accurate length of the loop line is
0.01937 -0.0147
0.0
1
937
-
0,0054
1
4
I,
=
72 400 ~~~ ~~ ~
=
2.423
x
lo4
m .
(c)
Location
of
booster stations
The transport of a prescribed flow rate through a pipeline of given trace, and
diameter must be carried out by applying the possibly least number of booster
stations, thus reducing the investment cost ofthe pump stations to a minimum. This
aim can be achieved by designing pump stations, the discharge pressure of which
equals the greatest allowed internal overpressure of the pipeline, and the suction
pressure is equal to the atmospheric tank pressure. The pressure profile slope, the
flow gradient, between two pump stations is determined by the oil rate
4,
to be
transported
in
the pipeline of a given diameter. The first pump station is located at
the head end point,
K.
From the
h,,,,
plotted here the pressure profile line
corresponding to the pressure gradient is to be drawn up
to
the point, where the line
would intersect the curve of ground profile augmented
with
the tank height. This
intersection is the spot where the second pump station must be located. Here again,
the
h,,,
is plotted, and the graphical design is to be continued,
until
the oil is
transported to tail end point,
r!
by the last pump station. While applying this design
method,
it
is supposed, that at the booster station storage tanks of atmospheric
pressure are used (see
Fig.
7.4-4).
At
tankless booster stations the suction pressure
may not be lower than the bubble point pressure of the oil. Here, the stations
will
be
closer to each other than
in
ease of transporting systems applying tanks, and,
so
the
number of stations will be greater.
Example
7.4-
4.
The transport capacity of the pipeline, described
in
the previous
Example, must be increased
to
340 m3/h by applying booster stations. The location
of the pump stations with tanks is to be designed.
The Reynolds number for an oil flow rate of 340 m3/h =0.0945 m3/s, according to
Eq. 7.4- 7, is 7.6
x
lo4.
The friction factor, calculated from
Eq.
1
.I
-
7 is 0.0226. The