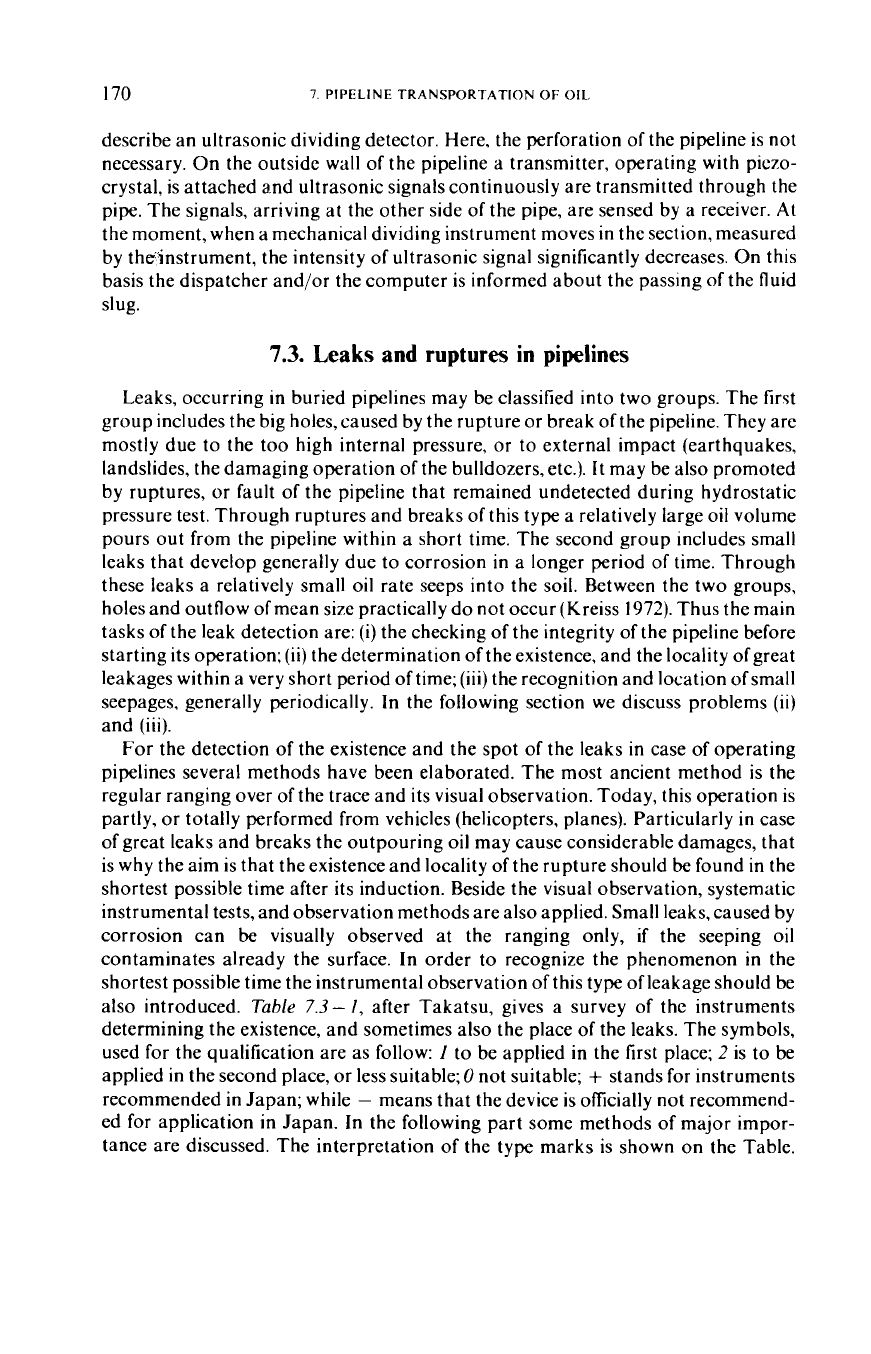
170
7.
PIPELINE TRANSPOR7ATION
OF
OIL
describe an ultrasonic dividing detector. Here, the perforation of the pipeline is not
necessary. On the outside wall of the pipeline a transmitter, operating
with
piezo-
crystal, is attached and ultrasonic signals continuously are transmitted through the
pipe. The signals, arriving at the other side of the pipe, are sensed by a receiver.
At
the moment, when a mechanical dividing instrument moves
in
the section, measured
by the'instrument, the intensity of ultrasonic signal significantly decreases.
On
this
basis the dispatcher and/or the computer is informed about the passing of the fluid
slug.
7.3.
Leaks and ruptures in pipelines
Leaks, occurring in buried pipelines may be classified into two groups. The first
group includes the big holes, caused by the rupture
or
break of the pipeline. They are
mostly due to the too high internal pressure,
or
to external impact (earthquakes,
landslides, the damaging operation of the bulldozers, etc.).
It
may be also promoted
by ruptures,
or
fault
of the pipeline that remained undetected during hydrostatic
pressure test. Through ruptures and breaks
of
this type a relatively large oil volume
pours out from the pipeline
within
a short time. The second group includes small
leaks that develop generally due to corrosion
in
a longer period of time. Through
these leaks a relatively small oil rate seeps into the soil. Between the two groups,
holes and outflow ofmean size practically do not occur (Kreiss
1972).
Thus the main
tasks
of
the leak detection are:
(i)
the checking of the integrity of the pipeline before
starting its operation;
(ii)
the determination of the existence, and the locality of great
leakages within a very short period
of
time;
(iii)
the recognition and location of small
seepages, generally periodically. In the following section we discuss problems
(ii)
and
(iii).
For
the detection
of
the existence and the spot
of
the leaks in case of operating
pipelines several methods have been elaborated. The most ancient method is the
regular ranging over of the trace and its visual observation. Today, this operation is
partly,
or
totally performed from vehicles (helicopters, planes). Particularly in case
of great leaks and breaks the outpouring oil may cause considerable damages, that
is why the aim is that the existence and locality of the rupture should
be
found in the
shortest possible time after its induction. Beside the visual observation, systematic
instrumental tests, and observation methods are also applied. Small leaks, caused by
corrosion can
be
visually observed at the ranging only,
if
the seeping oil
contaminates already the surface. In order to recognize the phenomenon
in
the
shortest possible time the instrumental observation of this type
of
leakage should be
also introduced.
Table
7.3-1,
after Takatsu, gives a survey of the instruments
determining the existence, and sometimes also the place of the leaks. The symbols,
used for the qualification are as follow:
I
to be applied in the first place;
2
is to be
applied in the second place,
or
less suitable;
0
not suitable;
+
stands for instruments
recommended in Japan; while
-
means that the device is officially not recommend-
ed for application in Japan. In the following part some methods of major impor-
tance are discussed. The interpretation of the type marks is shown on the Table.