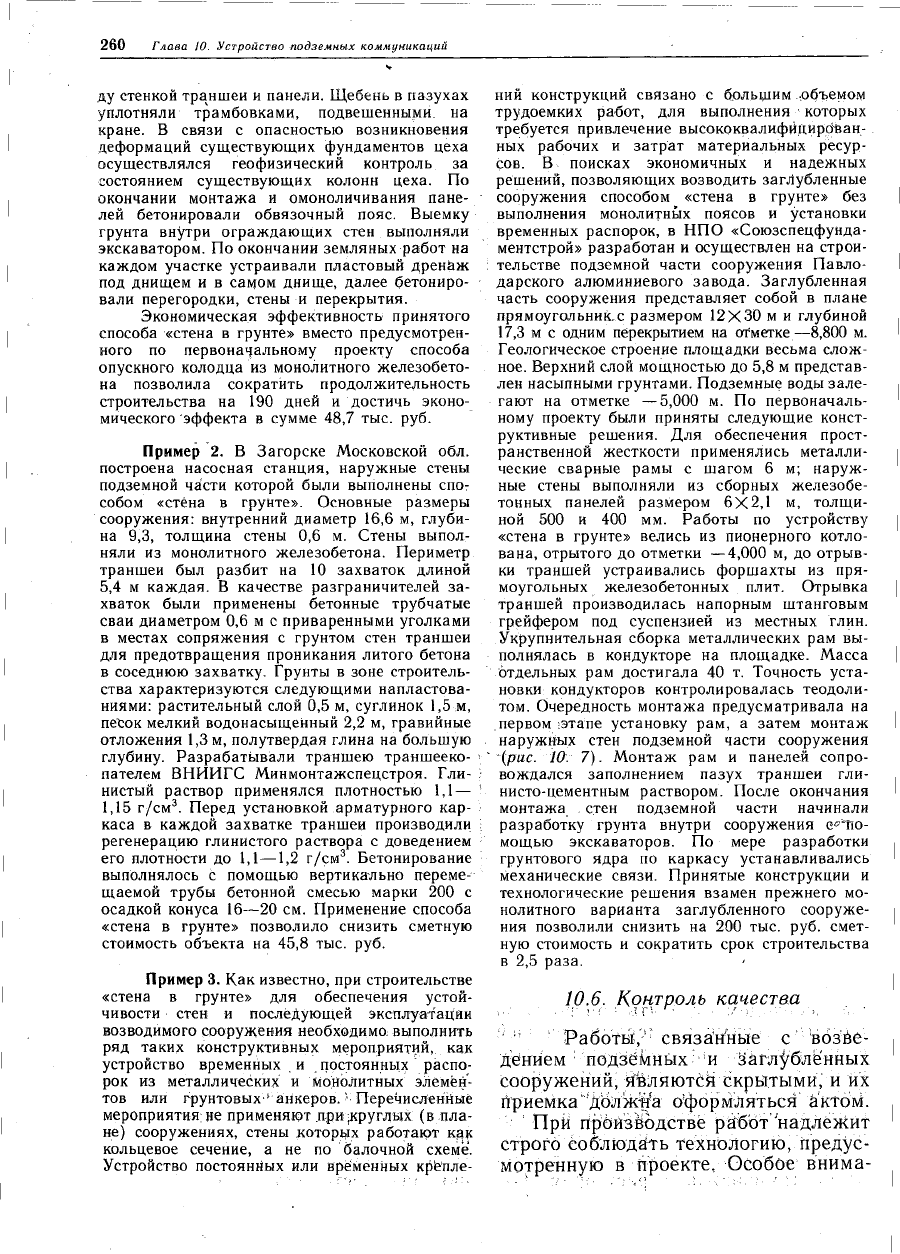
260 Г лава JO. Устройство подземных коммуникаций
ду стенкой траншеи и панели. Щебень в пазухах
уплотняли трамбовками, подвешенными, на
кране. В связи с опасностью возникновения
деформаций существующих фундаментов цеха
осуществлялся геофизический контроль за
состоянием существующих колонн цеха. По
окончании монтажа и омоноличивания пане-
лей бетонировали обвязочный пояс. Выемку
грунта внутри ограждающих стен выполняли
экскаватором. По окончании земляных работ на
каждом участке устраивали пластовый дрен&ж
под днищем и в самом днище, далее бетониро-
вали перегородки, стены и перекрытия.
Экономическая эффективность принятого
способа «стена в грунте» вместо предусмотрен-
ного по первоначальному проекту способа
опускного колодца из монолитного железобето-
на позволила сократить продолжительность
строительства на 190 дней и достичь эконо-
мического эффекта в сумме 48,7 тыс. руб.
Пример 2. В Загорске Московской обл.
построена насосная станция, наружные стены
подземной части которой были выполнены спо-
собом «стена в грунте». Основные размеры
сооружения: внутренний диаметр 16,6 м, глуби-
на 9,3, толщина стены 0,6 м. Стены выпол-
няли из монолитного железобетона. Периметр
траншеи был разбит на 10 захваток длиной
5,4 м каждая. В качестве разграничителей за-
хваток были применены бетонные трубчатые
сваи диаметром 0,6 м с приваренными уголками
в местах сопряжения с грунтом стен траншеи
для предотвращения проникания литого бетона
в соседнюю захватку. Грунты в зоне строитель-
ства характеризуются следующими напластова-
ниями: растительный слой 0,5 м, суглинок 1,5 м,
netoK мелкий водонасыщенный 2,2 м, гравийные
отложения 1,3 м, полутвердая глина на большую
глубину. Разрабатывали траншею траншееко-
пателем ВНИИГС Минмонтажспецстроя. Гли- )
нистый раствор применялся плотностью 1,1— •
1,15 г/см
3
. Перед установкой арматурного кар-
каса в каждой захватке траншеи производили \
регенерацию глинистого раствора с доведением
его плотности до
1,1
—1,2 г/см
3
. Бетонирование
выполнялось с помощью вертикально переме-
щаемой трубы бетонной смесью марки 200 с
осадкой конуса 16—20 см. Применение способа
«стена в грунте» позволило снизить сметную
стоимость объекта на 45,8 тыс. руб.
Пример 3. Как известно, при строительстве
«стена в грунте» для обеспечения устой-
чивости стен и последующей эксплуатации
возводимого сооружения необходимо; выполнить
ряд таких конструктивных мероприятий, как
устройство временных и постоянных распо-
рок из металлических и монолитных элемен-
тов или грунтовых^ анкеров.
>
Перечисленные
мероприятия; не применяют дри •круглых (в пла-
не) сооружениях, стены которых работают как
кольцевое сечение, а не по балочной схеме.
Устройство постоянных или временных крепле-
ний конструкций связано с большимобъемом
трудоемких работ, для выполнения которых
требуется привлечение высококвалифйциррйан-
ных рабочих и затрат материальных ресур-
сов.
В поисках экономичных и надежных
решений, позволяющих возводить заглубленные
сооружения способом «стена в грунте» без
выполнения монолитных поясов и установки
временных распорок, в НПО «Союзспецфунда-
ментстрой» разработан и осуществлен на строи-
тельстве подземной части сооружения Павло-
дарского алюминиевого завода. Заглубленная
часть сооружения представляет собой в плане
прямоугольнике размером 12X30 м и глубиной
17,3 м с одним перекрытием на отметке—8,800 м.
Геологическое строение площадки весьма слож-
ное.
Верхний слой мощностью до 5,8 м представ-
лен насыпными грунтами. Подземные воды зале-
гают на отметке —5,000 м. По первоначаль-
ному проекту были приняты следующие конст-
руктивные решения. Для обеспечения прост-
ранственной жесткости применялись металли-
ческие сварные рамы с шагом 6 м; наруж-
ные стены выполняли из сборных железобе-
тонных панелей размером 6X2,1 м, толщи-
ной 500 и 400 мм. Работы по устройству
«стена в грунте» велись из пионерного котло-
вана, отрытого до отметки —4,000 м, до отрыв-
ки траншей устраивались форшахты из пря-
моугольных железобетонных плит. Отрывка
траншей производилась напорным штанговым
грейфером под суспензией из местных глин.
Укрупнительная сборка металлических рам вы-
полнялась в кондукторе на площадке. Масса
отдельных рам достигала 40 т. Точность уста-
новки кондукторов контролировалась теодоли-
том.
Очередность монтажа предусматривала на
первом -этапе установку рам, а затем монтаж
наружных стен подземной части сооружения
(рас. 10. 7). Монтаж рам и панелей сопро-
вождался заполнением пазух траншеи гли-
нисто-цементным раствором. После окончания
монтажа стен подземной части начинали
разработку грунта внутри сооружения ^"по-
мощью экскаваторов. По мере разработки
грунтового ядра по каркасу устанавливались
механические связи. Принятые конструкции и
технологические решения взамен прежнего мо-
нолитного варианта заглубленного сооруже-
ния позволили снизить на 200 тыс. руб. смет-
ную стоимость и сократить срок строительства
в 2,5 раза.
10.6. Контроль качества
и
Работа/" связанные с возве-
дением подземных 'И Заглублённых
сооружений, Йтзляютсй скрытыми, и их
йриемка''''Abji'ikWa оформляться актом.
При прбйзЙодствё рйбот 'надлежит
строго боблюдагть технологию, предус-
мотренную в проекте, Особое внима-