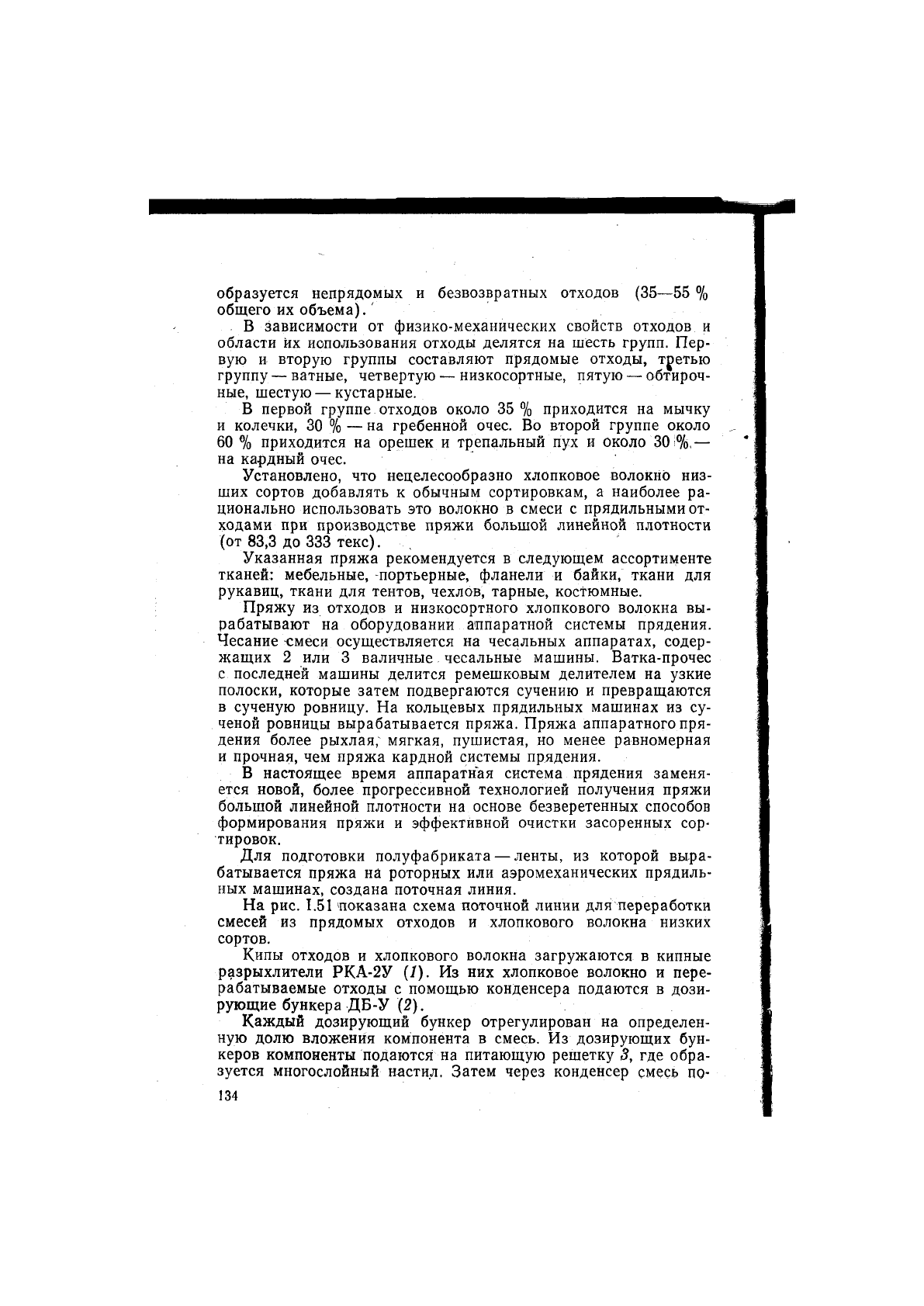
образуется непрядомых и безвозвратных отходов (35—55 %
общего их объема).'
В зависимости от физико-механических свойств отходов и
области их использования отходы делятся на шесть групп. Пер-
вую и вторую группы составляют прядомые отходы, третью
группу —ватные, четвертую — низкосортные, пятую — обтироч-
ные, шестую — кустарные.
В первой группе отходов около 35% приходится на мычку
и колечки, 30 % — на гребенной очес. Во второй группе около
60 % приходится на орешек и трепальный пух и около 30 %,—
на кардный очес.
Установлено, что нецелесообразно хлопковое волокно низ-
ших сортов добавлять к обычным сортировкам, а наиболее ра-
ционально использовать это волокно в смеси с прядильными от-
ходами при производстве пряжи большой линейной плотности
(от 83,3 до 333 текс).
Указанная пряжа рекомендуется в следующем ассортименте
тканей: мебельные, -портьерные, фланели и байки, ткани для
рукавиц, ткани для тентов, чехлов, тарные, костюмные.
Пряжу из отходов и низкосортного хлопкового волокна вы-
рабатывают на оборудовании аппаратной системы прядения.
Чесание ч:меси осуществляется на чесальных аппаратах, содер-
жащих 2 или 3 наличные чесальные машины. Ватка-прочес
с последней машины делится ремешковым делителем на узкие
полоски, которые затем подвергаются сучению и превращаются
в сученую ровницу. На кольцевых прядильных машинах из су-
ченой ровницы вырабатывается пряжа. Пряжа аппаратного пря-
дения более рыхлая,- мягкая, пушистая, но менее равномерная
и прочная, чем пряжа кардной системы прядения.
В настоящее время аппаратная система прядения заменя-
ется новой, более прогрессивной технологией получения пряжи
большой линейной плотности на основе безверетенных способов
формирования пряжи и эффективной очистки засоренных сор-
тировок.
Для подготовки полуфабриката —ленты, из которой выра-
батывается пряжа на роторных или аэромеханических прядиль-
ных машинах, создана поточная линия.
На рис. 1.51 показана схема поточной линии для переработки
смесей из прядомых отходов и хлопкового волокна низких
сортов.
Кипы отходов и хлопкового волокна загружаются в кипные
разрыхлители РКА-2У (/). Из них хлопковое волокно и пере-
рабатываемые отходы с помощью конДенсера подаются в дози-
рующие бункера ДБ-У (2).
Каждый дозирующий бункер отрегулирован на определен-
ную долю вложения компонента в смесь. Из дозирующих бун-
керов компоненты подаются на питающую решетку 5, где обра-
зуется многослойный настил. Затем через конденсер смесь по-