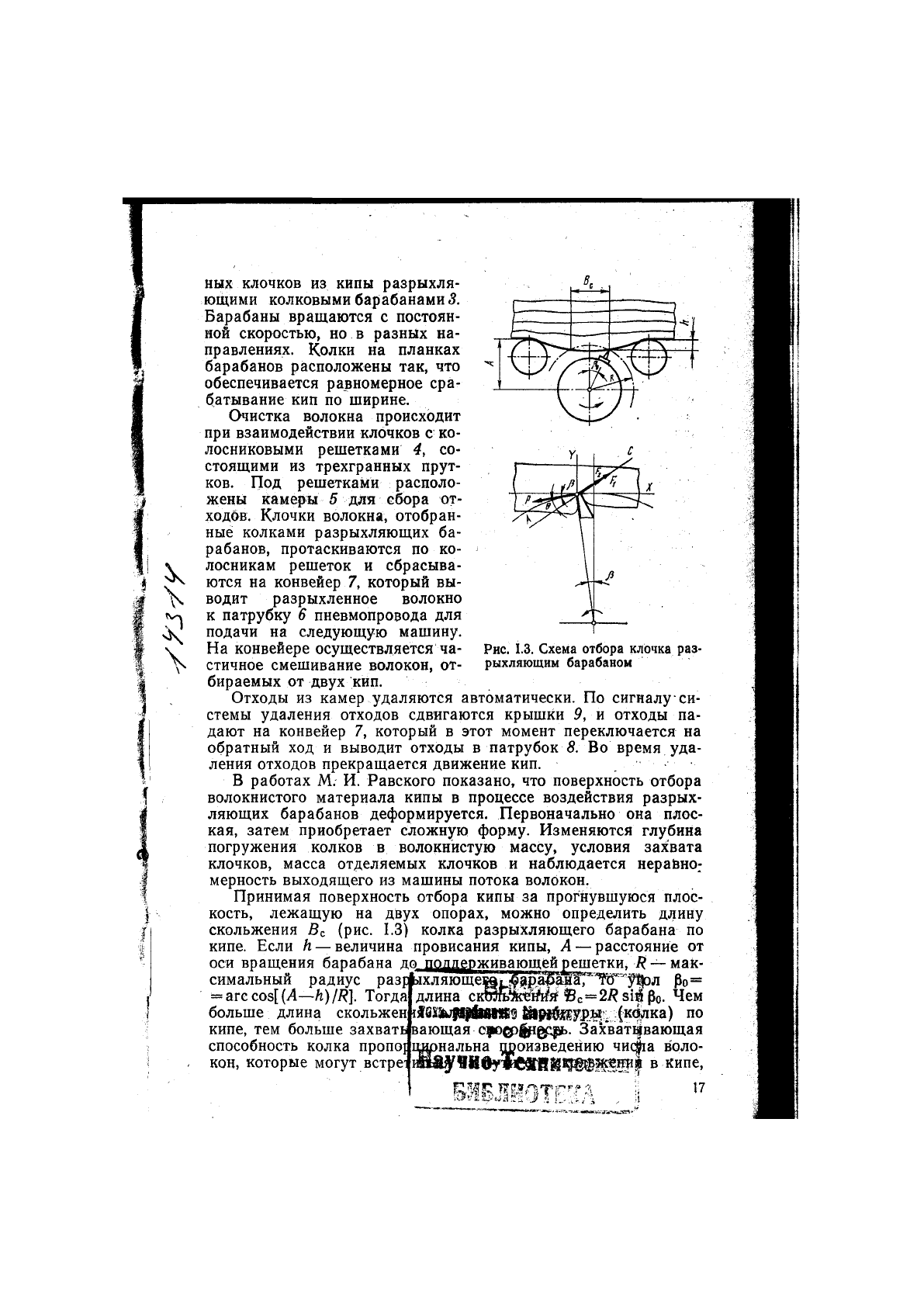
V
V
Рис. 1.3. Схема отбора клочка раз-
рыхляющим барабаном
ных клочков из кипы разрыхля-
ющими колковыми барабанами 8.
Барабаны вращаются с постоян-
ной скоростью, но в разных на-
правлениях. Колки на планках
барабанов расположены так, что
обеспечивается равномерное сра-
батывание кип по ширине.
Очистка волокна происходит
при взаимодействии клочков с ко-
лосниковыми решетками 4, со-
стоящими из трехгранных прут-
ков. Под решетками располо-
жены камеры 5 для сбора от-
ходбн. Клочки волокна, отобран-
ные колками разрыхляющих ба-
рабанов, протаскиваются по ко-
лосникам решеток и сбрасыва-
ются на конвейер 7, который вы-
водит разрыхленное волокно
к патрубку 6 пневмопровода для
подачи на следующую машину.
На конвейере осуществляется ча-
стичное смешивание волокон, от-
бираемых от двух кип.
Отходы из камер удаляются автоматически. По сигналу си-
стемы удаления отходов сдвигаются крышки 9, и отходы па-
дают на конвейер 7, который в этот момент переключается на
обратный ход и выводит отходы в патрубок S. Во время уда-
ления отходов прекращается движение кип.
В работах М. И. Равского показано, что поверхность отбора
волокнистого материала кипы в процессе воздействия разрых-
ляющих барабанов деформируется. Первоначально она плос-
кая, затем приобретает сложную форму. Изменяются глубина
погружения колков в волокнистую массу, условия захвата
клочков, масса отделяемых клочков и наблюдается нерайно;
мерность выходящего из машины потока волокон.
Принимая поверхность отбора кипы за прогнувшуюся плос-
кость, лежащую на двух опорах, можно определить длину
скольжения Вс (рис. 1.3) колка разрыхляющего барабана по
кипе. Если й —величина провисания кипы, А — расстояние от
оси вращения барабана до под1|^рживающей£ешетки. 7? — мак-
симальный радиус разр1ыхляющ^ш]1^Щ^ана,
Ро
=
= aTccos[{A—h)/Rl Тогда длина скШжЙУ^ si® Ро. Чем
больше длина скольжен ilSSI^fi^inmf (колка) по
кипе, тем больше захвать вающая cfogp^^:^. Захватывающая
способность колка nponoj хданальна щоизведению чифа воло-
кон, которые могут встре'^РЙЙувИвутеЗгаЙВДФШШ'? в кипе,
17
ШБЛкОТ^чД