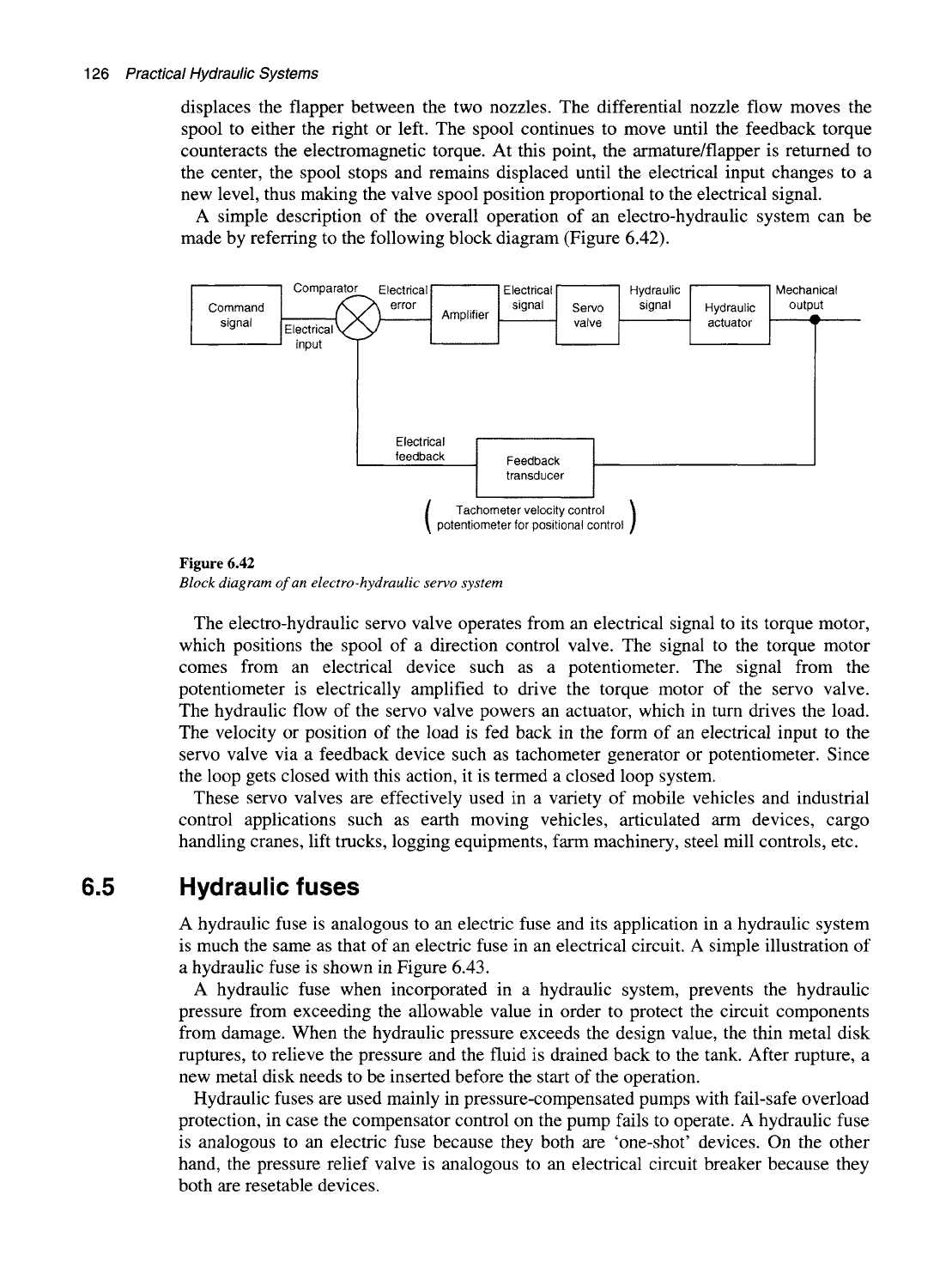
126 Practical Hydraulic Systems
displaces the flapper between the two nozzles. The differential nozzle flow moves the
spool to either the right or left. The spool continues to move until the feedback torque
counteracts the electromagnetic torque. At this point, the armature/flapper is returned to
the center, the spool stops and remains displaced until the electrical input changes to a
new level, thus making the valve spool position proportional to the electrical signal.
A simple description of the overall operation of an electro-hydraulic system can be
made by referring to the following block diagram (Figure 6.42).
Command
signal
Comparator^ Electrical
error
Electrical
input
Amplifier
Electrical
signal
Servo
valve
Hydraulic
signal
Hydraulic
actuator
Mechanical
output
f
Electrical
feedback
Feedback
transducer
Tachometer velocity control
potentiometer for positional control
Figure 6.42
Block diagram of an electro-hydraulic servo system
The electro-hydraulic servo valve operates from an electrical signal to its torque motor,
which positions the spool of a direction control valve. The signal to the torque motor
comes from an electrical device such as a potentiometer. The signal from the
potentiometer is electrically amplified to drive the torque motor of the servo valve.
The hydraulic flow of the servo valve powers an actuator, which in turn drives the load.
The velocity or position of the load is fed back in the form of an electrical input to the
servo valve via a feedback device such as tachometer generator or potentiometer. Since
the loop gets closed with this action, it is termed a closed loop system.
These servo valves are effectively used in a variety of mobile vehicles and industrial
control applications such as earth moving vehicles, articulated arm devices, cargo
handling cranes, lift trucks, logging equipments, farm machinery, steel mill controls, etc.
6.5 Hydraulic fuses
A hydraulic fuse is analogous to an electric fuse and its application in a hydraulic system
is much the same as that of an electric fuse in an electrical circuit. A simple illustration of
a hydraulic fuse is shown in Figure 6.43.
A hydraulic fuse when incorporated in a hydraulic system, prevents the hydraulic
pressure from exceeding the allowable value in order to protect the circuit components
from damage. When the hydraulic pressure exceeds the design value, the thin metal disk
ruptures, to relieve the pressure and the fluid is drained back to the tank. After rupture, a
new metal disk needs to be inserted before the start of the operation.
Hydraulic fuses are used mainly in pressure-compensated pumps with fail-safe overload
protection, in case the compensator control on the pump fails to operate. A hydraulic fuse
is analogous to an electric fuse because they both are 'one-shot' devices. On the other
hand, the pressure relief valve is analogous to an electrical circuit breaker because they
both are resetable devices.