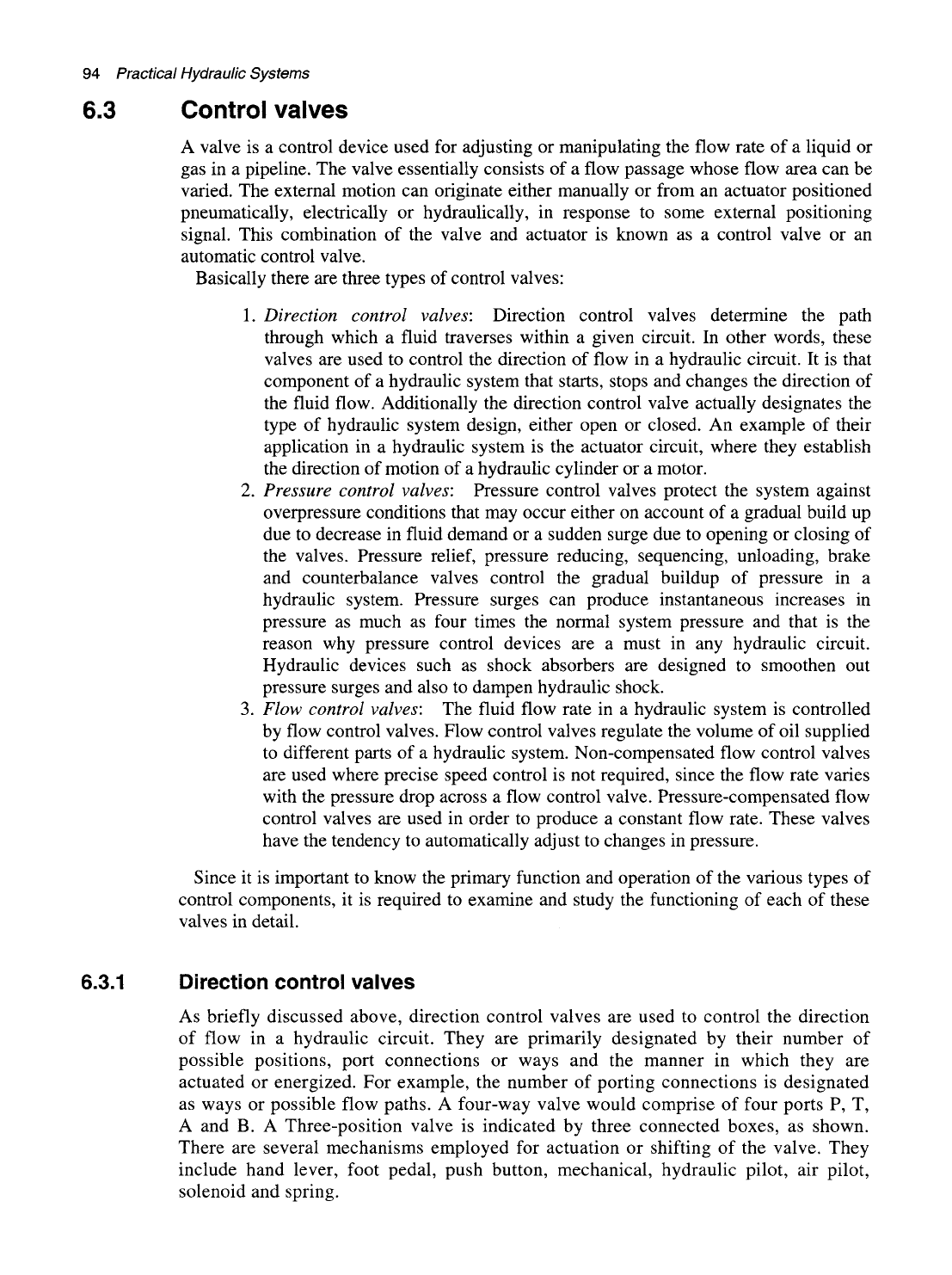
94
Practical Hydraulic Systems
6.3 Control valves
A valve is a control device used for adjusting or manipulating the flow rate of a liquid or
gas in a pipeline. The valve essentially consists of a flow passage whose flow area can be
varied. The external motion can originate either manually or from an actuator positioned
pneumatically, electrically or hydraulically, in response to some external positioning
signal. This combination of the valve and actuator is known as a control valve or an
automatic control valve.
Basically there are three types of control valves:
1.
Direction control valves: Direction control valves determine the path
through which a fluid traverses within a given circuit. In other words, these
valves are used to control the direction of flow in a hydraulic circuit. It is that
component of a hydraulic system that starts, stops and changes the direction of
the fluid flow. Additionally the direction control valve actually designates the
type of hydraulic system design, either open or closed. An example of their
application in a hydraulic system is the actuator circuit, where they establish
the direction of motion of a hydraulic cylinder or a motor.
2.
Pressure control valves: Pressure control valves protect the system against
overpressure conditions that may occur either on account of a gradual build up
due to decrease in fluid demand or a sudden surge due to opening or closing of
the valves. Pressure
reUef,
pressure reducing, sequencing, unloading, brake
and counterbalance valves control the gradual buildup of pressure in a
hydraulic system. Pressure surges can produce instantaneous increases in
pressure as much as four times the normal system pressure and that is the
reason why pressure control devices are a must in any hydraulic circuit.
Hydraulic devices such as shock absorbers are designed to smoothen out
pressure surges and also to dampen hydraulic shock.
3.
Flow control valves: The fluid flow rate in a hydraulic system is controlled
by flow control valves. Flow control valves regulate the volume of oil supplied
to different parts of a hydraulic system. Non-compensated flow control valves
are used where precise speed control is not required, since the flow rate varies
with the pressure drop across a flow control valve. Pressure-compensated flow
control valves are used in order to produce a constant flow rate. These valves
have the tendency to automatically adjust to changes in pressure.
Since it is important to know the primary function and operation of the various types of
control components, it is required to examine and study the functioning of each of these
valves in detail.
6.3.1 Direction control valves
As briefly discussed above, direction control valves are used to control the direction
of flow in a hydraulic circuit. They are primarily designated by their number of
possible positions, port connections or ways and the manner in which they are
actuated or energized. For example, the number of porting connections is designated
as ways or possible flow paths. A four-way valve would comprise of four ports P, T,
A and B. A Three-position valve is indicated by three connected boxes, as shown.
There are several mechanisms employed for actuation or shifting of the valve. They
include hand lever, foot pedal, push button, mechanical, hydraulic pilot, air pilot,
solenoid and spring.