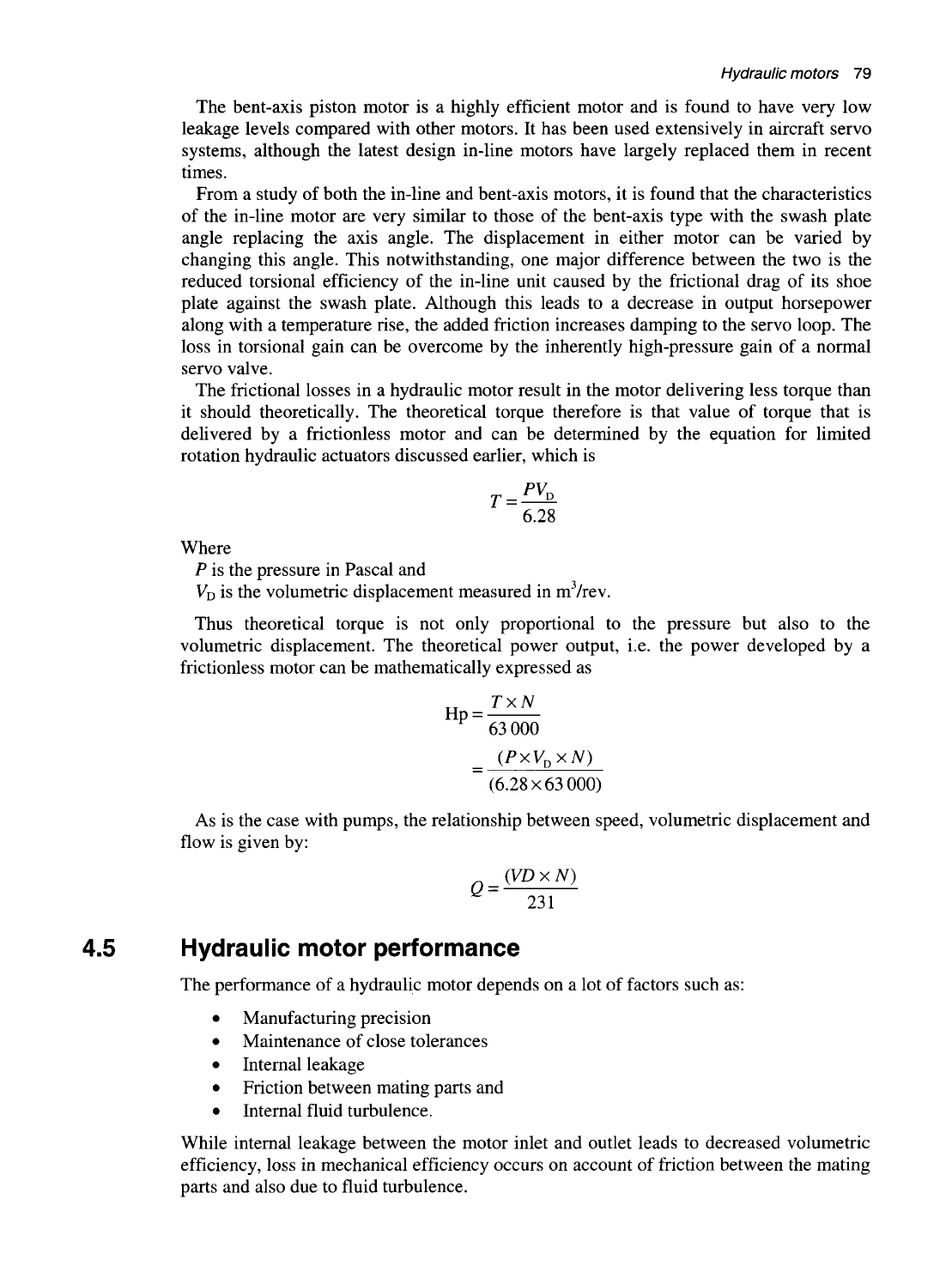
Hydraulic motors
79
The bent-axis piston motor is a highly efficient motor and is found to have very low
leakage levels compared with other motors. It has been used extensively in aircraft servo
systems, although the latest design in-line motors have largely replaced them in recent
times.
From a study of both the in-line and bent-axis motors, it is found that the characteristics
of the in-line motor are very similar to those of the bent-axis type with the swash plate
angle replacing the axis angle. The displacement in either motor can be varied by
changing this angle. This notwithstanding, one major difference between the two is the
reduced torsional efficiency of the in-line unit caused by the frictional drag of its shoe
plate against the swash plate. Although this leads to a decrease in output horsepower
along with a temperature rise, the added friction increases damping to the servo loop. The
loss in torsional gain can be overcome by the inherently high-pressure gain of a normal
servo valve.
The frictional losses in a hydraulic motor result in the motor delivering less torque than
it should theoretically. The theoretical torque therefore is that value of torque that is
delivered by a frictionless motor and can be determined by the equation for limited
rotation hydraulic actuators discussed earlier, which is
6.28
Where
P is the pressure in Pascal and
VD
is the volumetric displacement measured in mVrev.
Thus theoretical torque is not only proportional to the pressure but also to the
volumetric displacement. The theoretical power output, i.e. the power developed by a
frictionless motor can be mathematically expressed as
Hp =
63
000
(PxV^xN)
"(6.28x63 000)
As is the case with pumps, the relationship between speed, volumetric displacement and
flow is given by:
(VDxN)
231
4.5 Hydraulic motor performance
The performance of a hydraulic motor depends on a lot of factors such as:
• Manufacturing precision
• Maintenance of close tolerances
• Internal leakage
• Friction between mating parts and
• Internal fluid turbulence.
While internal leakage between the motor inlet and outlet leads to decreased volumetric
efficiency, loss in mechanical efficiency occurs on account of friction between the mating
parts and also due to fluid turbulence.