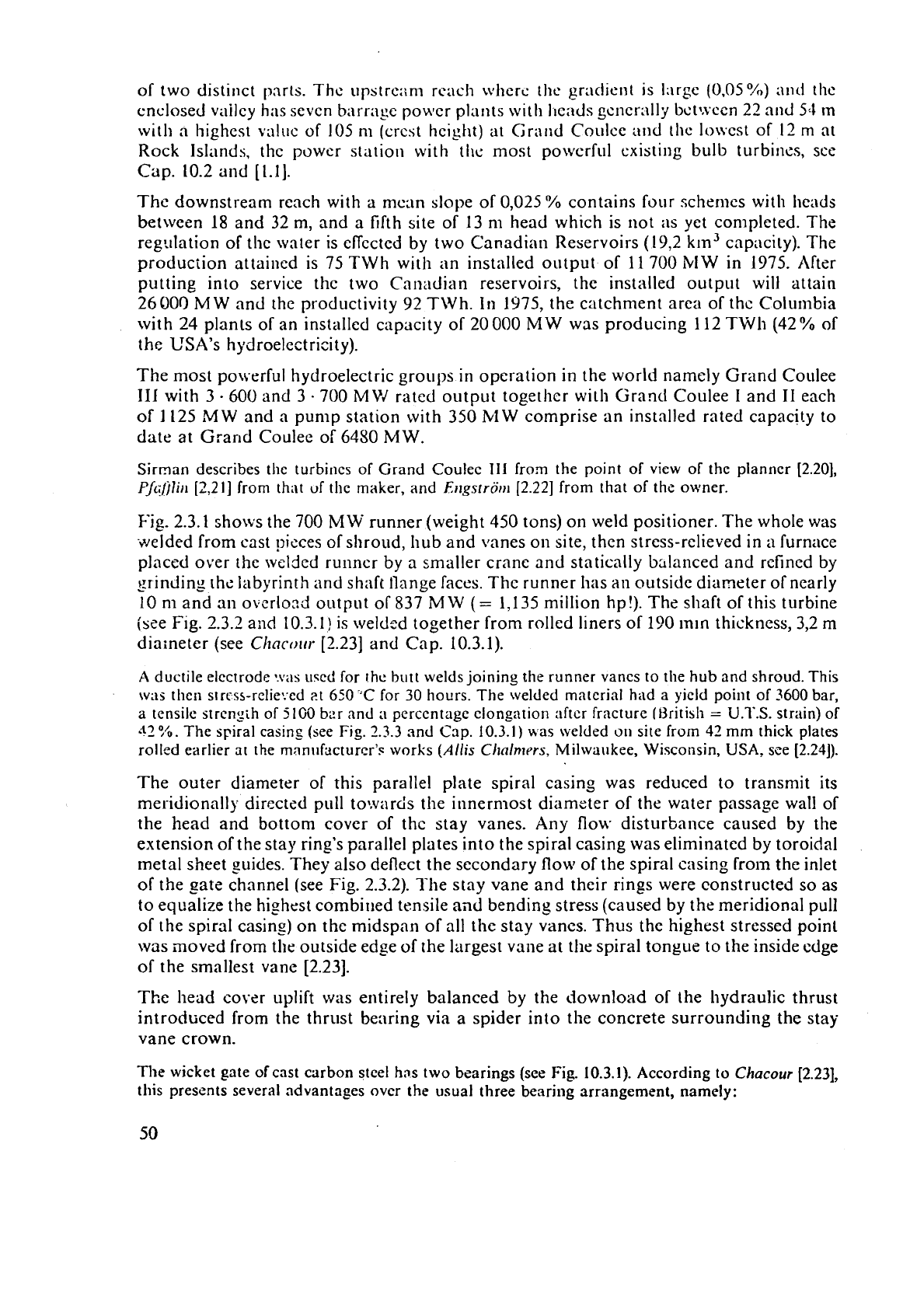
of two disti~lct parts. Tho upstrc;in~ rcach wllcrc tlic gradient is large (0,0544,)
and
thc
cnclosed vailey has scvcn b;irr-n~e power plants with hc;lds gcncrnlly but1,vccn 22 and
5.1
In
with a highest v;lluc of 105
m
(crcst hcight) at Gra~ld Coulce and thc lolvest of 12
m
at
Rock Islands,
the power station with the most powerful existing bulb turbines, sce
Cap. 10.2 and
(1.11.
The
downstream reach with a mean slope of 0,025 YO contains four schemes with heads
between
18
and 32 m, and a fifth site of 13
rn
head which is not
as
yet completed. The
regalation of
the water is effected by two Canadian Reservoirs (19,2 k1n3 capacily). The
production
attained is 75
TbVh
with an installed output of
11
700 h1W in 1975. After
putting into service
the two Canadian reservoirs, the installed output will attain
26
009
M
W
and the productivity 92 TWh. In 1975, the catchment area of thc Columbia
with 24 plants of an installed capacity of
20000 MW was producing 112
TWh
(42Y0 of
the USA's hydroelectricity).
The most
polverful hydroelectric groups in operation in the world namely Grand Coulee
111
with 3
-
600 and 3 700 MW rated output together with Grand Coulee
I
and
11
each
of
1125
MW
and a pump station with 350
MW
comprise an installed rated capaci!y to
date at Grand Coulee of 6450 MW.
Sirman describes
the
turbirics of Grand Coulee
I11
from the point of view of the planner [2.20],
PJ~~fjlir~
[2,21]
from that
uf
the maker, and
E~lgsrron~
[2.22]
from that
of
the owner.
Fig.
2.3.1 shows the 700
MW
runner (weight 450 tons) on weld positioner. The whole was
welded from cast
pieces of shroud, hub and vanes on site, then stress-relieved in
n
furnace
placed over the welded runner by
a
smaller crane and statically balanced and refined by
erindins the labyrinth and shaft flange faces. Thc runner has an outside diameter of nearly
...
10
nl and
an
overlond outpiit of 837
M
W
(=
1,135 million hp!). The shaft of this turbine
(see
Fig.
2.3.2 and 10.3.1) is welded together from rolled liners of 190
rnln
thickness, 3,2 m
diaineter (see
Chnco~rr
[2.23] and
Cap.
10.3.1).
A
ductile electrode
-.\.;is
uqed
for
the
butt welds joining the runner vanes to the hub and shroud. This
was
then strrss-relie-:ed
~.t
650'C
for 30 hours. The welded material had a yield point of 3600 bar,
a
tensile strcnrih of
5160
bzr and
n
perccntagc elongation :rftcr fracture
(Hritisli
=
U.T.S.
strain)
of
The spiral casing (see
Fig.
7.3.3
and Cap.
10.3.1)
mas
welded
on
site from
42
mm thick plates
rolled earlier
at
the man~~ftlcturcr's works
(Allis
Clralntur.~,
Milwaukee, Wisconsin,
USA,
sce
[2.24]).
The outer diameter of this parallel plate spiral casing was reduced to transmit its
meridionally directed pull townrcis the innermost diameter of the water passage wall of
the head and bottom cover of
thc stay vanes. Any flow disturbance caused by the
extension of the stay ring's parallel plates into the spiral casing was eliminated by toroidal
metal sheet guides. They also deflect the secondary flow of the spiral casing from the inlet
of the
_gate channel (see Fig. 2.3.2). The stay vane and their rings were constructed so as
to equalize the
hishest combiried tensile
sad
bending stress (caused by the meridional pull
of
the spiral casing) on the midspan of all the stay vanes. Thus the highest stressed point
was
inoved
from the outside edge of the largest vane at the spiral tongue to the inside cdge
of
the smallest vane
E2.231.
The
head cover uplift was entirely balanced
by
the download of the Ilydraulic thrust
introduced from the thrust
bewing via
a
spider into the concrete surrounding the stay
vane crown.
The wicket gate
of
cast carbon steel has two bearings (see Fig.
10.3.1).
According to
Chacour
[2.23],
this presents several advantages over the usual three bearing arrangement, namely: