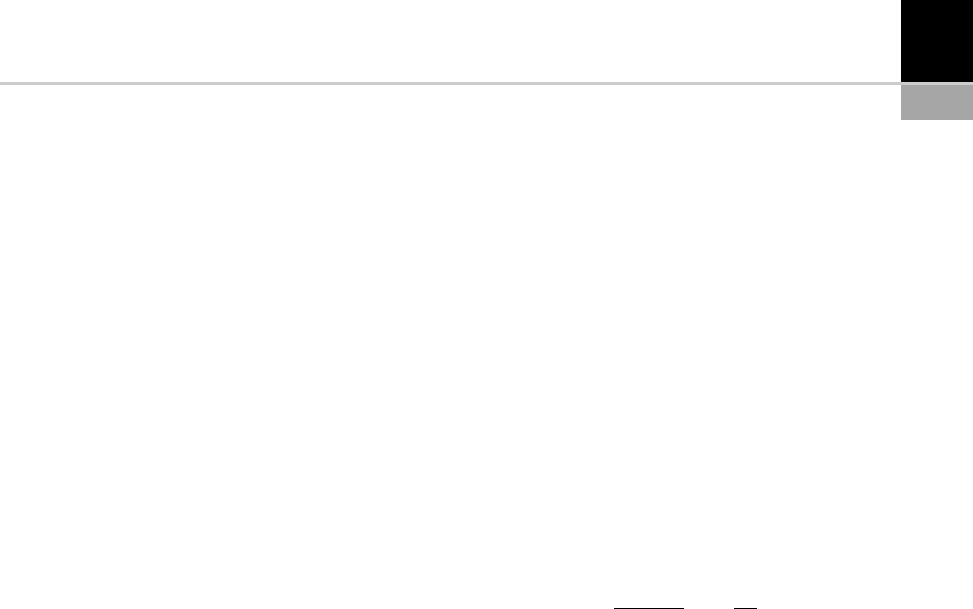
Process Parameters and Influences
Polymer suppliers and converters must deal with a
growing market demand for low cost ‘deposited
film/substrate’ complexes which still offer high
performance properties. Manufacturers, polymer
and substrate suppliers, and converters must
work together to reach these objectives. Various
studies have enabled improving polymer perfor-
mance while at the same time optimizing process
parameters. For example, in the packaging indus-
try, several complexes such as aluminum/polyeth-
ylene, paper/PE, etc., are used with low density
polyethylene (LDPE) without a binder layer.
These various structures are produced using
extrusion coating. Good adhesion between the
LDPE and the substrate is clearly vital. However,
the adhesive strength is generally very weak
between the substrate and the LDPE, due to the
lack of polar or reactive functions in LDPEs. Like-
wise, following the extrusion coating process, the
complexes alu/LDPE, paper/LDPE, etc., maintain
the sealing properties of polyethylene.
Example: Adhesive Properties of an Aluminum/
LDPE Structure. For adhe sion to occur between
LDPE and the aluminum foil, the LDPE has to
oxid ize during the extrusion process . This func-
tionaliz ation of the LDPE primarily occurs dur-
ing the molten polymer’s dwell time between the
die’s opening and the point of contact with the
substrate, i.e. in the air gap. Adhesion between
the LDPE and the substrate is affected by several
factors, whi ch can be categorized into three
groups: extrusion parameters (melt temperature,
air gap, etc.), polymer parameters (melt index,
density, etc.) and substrate parameters (type, sur-
face roughness, etc.). Over the last 20 years, the
practical problem of ensuring good adhesion
between the LDPE and various substrates during
extrusion coating has been the subject of much
interest, both from a technical and a scientific
poin t of view [1–7]. Whereas some parameters
(corona treatment, ozone, post-treatment, etc .)
generally increase adhesion, it is difficult to draw
a single conclusion for process parameters overall,
but most authors agree that interactions do exist
between these parameters. The main process
parameters with the greatest effect on adhesion
between the polymer and the substrate are: tem-
perature of the molten polymer, thickness of the
film deposited, pressure of the rollers, extrusion
speed, and air gap.
It is very difficult to separate the last two para-
meters: increasing the substrate speed effectively
reduces the dwel l time (d
t
) in the air gap and LDPE
oxidation becomes difficult, resulting in poor
adhesion. If the air gap is increased, the dwell time
d
t
(or freeze time t
f
) and LDPE oxidation will also
increase, but the LDPE will cool and its viscosity
will increase, reducing its wettability relative to
the substrate’s roughness. This in turn reduces
mechanical adhesion. These two phenomena con-
flict with one another; hence the need for a com-
promise. According to most authors, line speed
and air gap can be expressed as a single parameter,
that of freeze time t
f
:
t
f
¼
H
V
t
V
0
Ln
V
t
V
0
where V
t
= line speed, V
0
= material through P
and H = air gap.
Figure 15-2 illustrates the interactions between
the process parameters and the polymer, which
lead to changes in adhesive strength. At low tem-
peratures (T =285
C), the adhesive strength (F
p
)
of the LDPE increases with dwell time, attaining a
maximum value then falling. This increased adhe-
sion is correlated with an increase in the LDPE’s
carboxylic functions and, as a result, in its surface
energy (Y
p
). The drop in adhesion at high t
f
values
is related to cooling of the LDPE, which becomes
more viscous on contact with the substrate; as
a result, the LDPE does not mold as well to
the substrate’s surface. At high temperatures
(T =315
C), adhesion of the LDPE is very strong
despite short dwell times. This adhesion
decreases with high t
f
values. Oxidation of the
LDPE becomes excessive and initiates its degra-
dation, resulting in a high number of ruptured
chains and a drop in its surface energy ( Y
p
). This
leads to a layer with poor cohesion at the s urface
of the LDPE film, in turn provoking the drop
in adhesion.
CHAPTER 15 Polymer Thin Films – Processes, Parameters and Property Control 243