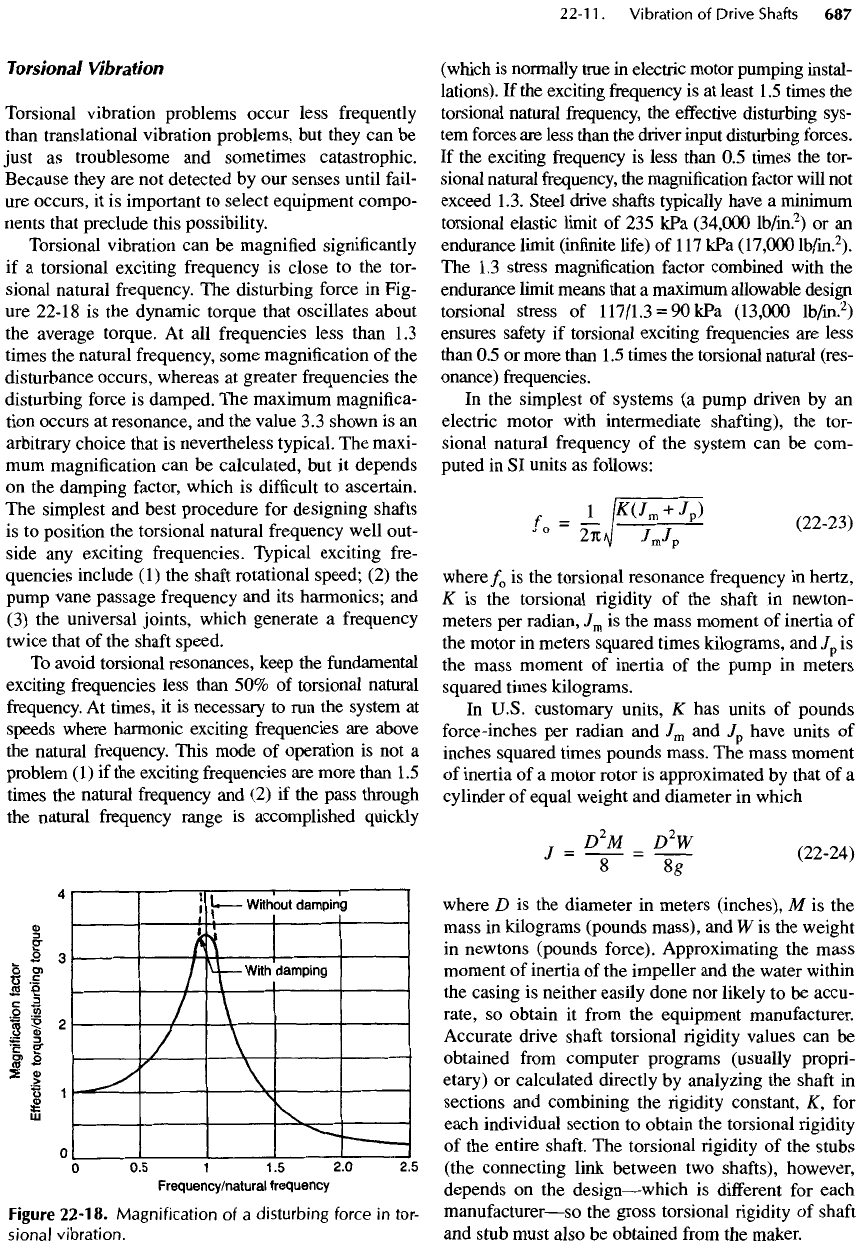
Torsional
Vibration
Torsional vibration problems occur less frequently
than
translational vibration problems,
but
they
can be
just
as
troublesome
and
sometimes catastrophic.
Because they
are not
detected
by our
senses until
fail-
ure
occurs,
it is
important
to
select
equipment
compo-
nents that preclude this possibility.
Torsional vibration
can be
magnified significantly
if
a
torsional exciting frequency
is
close
to the
tor-
sional natural frequency.
The
disturbing force
in
Fig-
ure
22-18
is the
dynamic torque that oscillates about
the
average torque.
At all
frequencies less than
1.3
times
the
natural frequency, some magnification
of the
disturbance
occurs,
whereas
at
greater
frequencies
the
disturbing force
is
damped.
The
maximum magnifica-
tion occurs
at
resonance,
and the
value
3.3
shown
is an
arbitrary
choice that
is
nevertheless typical.
The
maxi-
mum
magnification
can be
calculated,
but it
depends
on the
damping factor, which
is
difficult
to
ascertain.
The
simplest
and
best procedure
for
designing
shafts
is
to
position
the
torsional natural frequency well
out-
side
any
exciting frequencies. Typical exciting
fre-
quencies include
(1) the
shaft
rotational
speed;
(2) the
pump
vane passage frequency
and its
harmonics;
and
(3) the
universal joints, which generate
a
frequency
twice
that
of the
shaft
speed.
To
avoid torsional resonances, keep
the
fundamental
exciting
frequencies less than
50% of
torsional natural
frequency.
At
times,
it is
necessary
to run the
system
at
speeds where harmonic exciting frequencies
are
above
the
natural frequency. This mode
of
operation
is not a
problem
(1) if the
exciting frequencies
are
more than
1.5
times
the
natural
frequency
and (2) if the
pass through
the
natural
frequency
range
is
accomplished quickly
Figure
22-18.
Magnification
of a
disturbing
force
in
tor-
sional
vibration.
(which
is
normally true
in
electric motor pumping instal-
lations).
If the
exciting
frequency
is at
least
1.5
times
the
torsional natural frequency,
the
effective
disturbing
sys-
tem
forces
are
less than
the
driver input disturbing forces.
If
the
exciting frequency
is
less than
0.5
times
the
tor-
sional
natural frequency,
the
magnification
factor
will
not
exceed
1.3.
Steel
drive shafts typically have
a
minimum
torsional elastic limit
of 235
kPa
(34,000
lb/in.
2
)
or an
endurance
limit (infinite
life)
of
1
17
kPa
(17,000
lb/in.
2
).
The 1.3
stress magnification
factor
combined with
the
endurance limit means that
a
maximum allowable design
torsional stress
of
117/1.3
=
9OkPa
(13,000
lb/in.
2
)
ensures
safety
if
torsional exciting frequencies
are
less
than
0.5 or
more than
1.5
times
the
torsional natural
(res-
onance) frequencies.
In the
simplest
of
systems
(a
pump driven
by an
electric
motor with intermediate shafting),
the
tor-
sional natural frequency
of the
system
can be
com-
puted
in SI
units
as
follows:
=
J
_/w
m+
/
P
)
/0
1K>1
J
m
j
p
(2223)
where
/
0
is the
torsional resonance frequency
in
hertz,
K
is the
torsional
rigidity of the
shaft
in
newton-
meters
per
radian,
J
m
is the
mass moment
of
inertia
of
the
motor
in
meters squared times kilograms,
and/
p
is
the
mass moment
of
inertia
of the
pump
in
meters
squared times kilograms.
In
U.S.
customary units,
K has
units
of
pounds
force-inches
per
radian
and
J
m
and
/
p
have units
of
inches
squared times pounds mass.
The
mass moment
of
inertia
of a
motor rotor
is
approximated
by
that
of a
cylinder
of
equal weight
and
diameter
in
which
'
-
1"
-
f
where
D is the
diameter
in
meters (inches),
M is the
mass
in
kilograms (pounds mass),
and W is the
weight
in
newtons (pounds force). Approximating
the
mass
moment
of
inertia
of the
impeller
and the
water within
the
casing
is
neither easily done
nor
likely
to be
accu-
rate,
so
obtain
it
from
the
equipment manufacturer.
Accurate drive
shaft
torsional
rigidity
values
can be
obtained
from
computer
programs
(usually
propri-
etary)
or
calculated directly
by
analyzing
the
shaft
in
sections
and
combining
the
rigidity constant,
K,
for
each individual
section
to
obtain
the
torsional
rigidity
of
the
entire
shaft.
The
torsional
rigidity
of the
stubs
(the
connecting link between
two
shafts),
however,
depends
on the
design
—
which
is
different
for
each
manufacturer
—
so
the
gross torsional
rigidity of
shaft
and
stub must
also
be
obtained
from
the
maker.