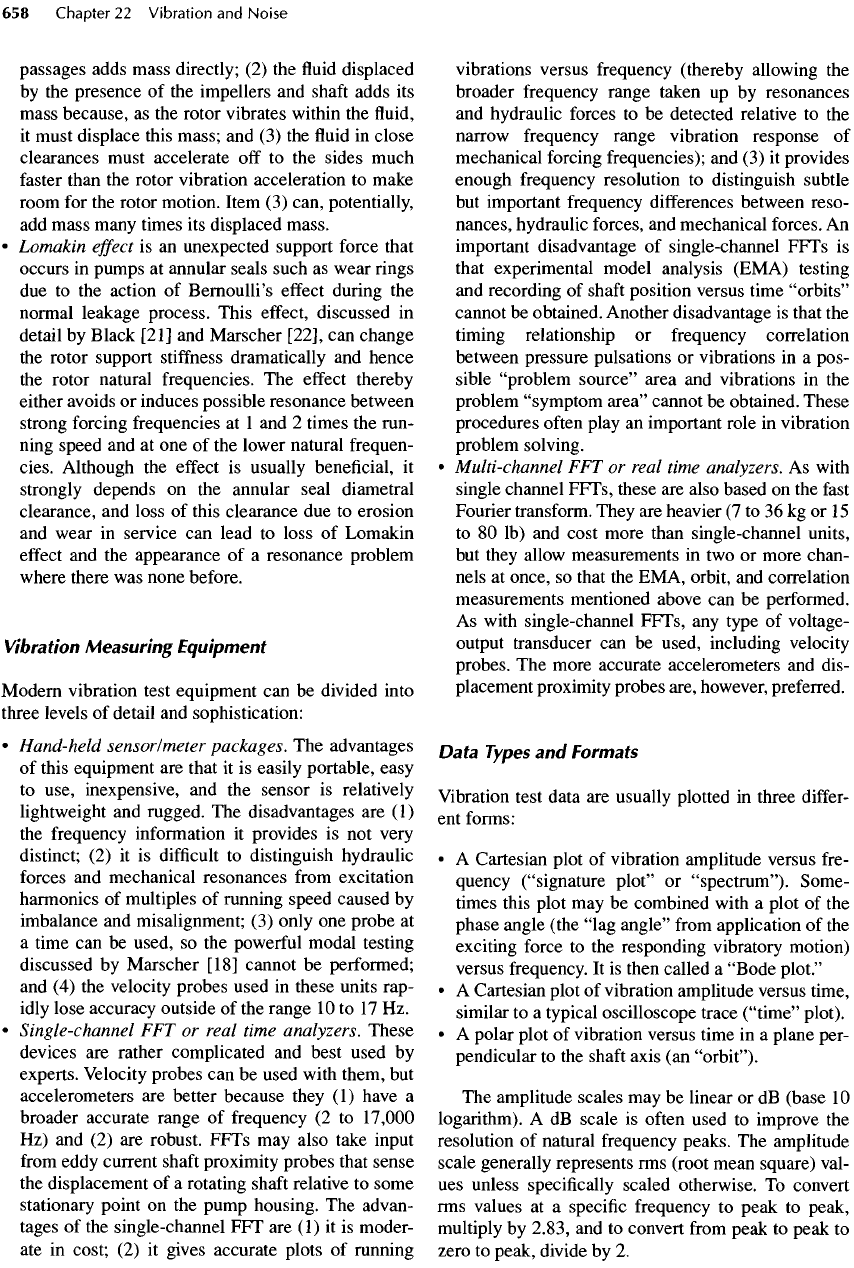
passages adds mass directly;
(2) the fluid
displaced
by
the
presence
of the
impellers
and
shaft
adds
its
mass because,
as the
rotor vibrates within
the fluid,
it
must displace this mass;
and (3) the fluid in
close
clearances must accelerate
off to the
sides much
faster
than
the
rotor vibration acceleration
to
make
room
for the
rotor motion. Item
(3)
can, potentially,
add
mass many times
its
displaced
mass.
•
Lomakin
effect
is an
unexpected support force that
occurs
in
pumps
at
annular seals such
as
wear rings
due to the
action
of
Bernoulli's
effect
during
the
normal leakage process. This
effect,
discussed
in
detail
by
Black
[21]
and
Marscher [22],
can
change
the
rotor support
stiffness
dramatically
and
hence
the
rotor natural frequencies.
The
effect
thereby
either avoids
or
induces possible resonance between
strong forcing frequencies
at 1 and 2
times
the
run-
ning
speed
and at one of the
lower natural
frequen-
cies. Although
the
effect
is
usually beneficial,
it
strongly depends
on the
annular seal diametral
clearance,
and
loss
of
this clearance
due to
erosion
and
wear
in
service
can
lead
to
loss
of
Lomakin
effect
and the
appearance
of a
resonance problem
where there
was
none before.
Vibration Measuring
Equipment
Modern vibration test equipment
can be
divided into
three levels
of
detail
and
sophistication:
•
Hand-held
sensor/meter
packages.
The
advantages
of
this equipment
are
that
it is
easily portable, easy
to
use, inexpensive,
and the
sensor
is
relatively
lightweight
and
rugged.
The
disadvantages
are (1)
the
frequency
information
it
provides
is not
very
distinct;
(2) it is
difficult
to
distinguish hydraulic
forces
and
mechanical resonances
from
excitation
harmonics
of
multiples
of
running speed caused
by
imbalance
and
misalignment;
(3)
only
one
probe
at
a
time
can be
used,
so the
powerful
modal testing
discussed
by
Marscher [18] cannot
be
performed;
and
(4) the
velocity probes used
in
these units rap-
idly lose accuracy outside
of the
range
10 to 17 Hz.
•
Single-channel
FFT or
real
time analyzers. These
devices
are
rather complicated
and
best used
by
experts. Velocity probes
can be
used with them,
but
accelerometers
are
better because they
(1)
have
a
broader accurate range
of
frequency
(2 to
17,000
Hz)
and (2) are
robust.
FFTs
may
also take input
from
eddy current
shaft
proximity probes that sense
the
displacement
of a
rotating
shaft
relative
to
some
stationary point
on the
pump housing.
The
advan-
tages
of the
single-channel
FFT are (1) it is
moder-
ate in
cost;
(2) it
gives accurate plots
of
running
vibrations versus frequency (thereby allowing
the
broader
frequency
range taken
up by
resonances
and
hydraulic forces
to be
detected
relative
to the
narrow frequency range vibration response
of
mechanical forcing frequencies);
and (3) it
provides
enough frequency resolution
to
distinguish subtle
but
important
frequency
differences
between reso-
nances,
hydraulic forces,
and
mechanical
forces.
An
important disadvantage
of
single-channel
FFTs
is
that
experimental model analysis (EMA) testing
and
recording
of
shaft
position versus time
"orbits"
cannot
be
obtained. Another disadvantage
is
that
the
timing
relationship
or
frequency correlation
between pressure pulsations
or
vibrations
in a
pos-
sible
"problem
source" area
and
vibrations
in the
problem "symptom
area"
cannot
be
obtained. These
procedures
often
play
an
important role
in
vibration
problem solving.
•
Multi-channel
FFT or
real
time analyzers.
As
with
single channel
FFTs,
these
are
also based
on the
fast
Fourier transform. They
are
heavier
(7 to 36 kg or 15
to
80
Ib)
and
cost more than single-channel units,
but
they allow measurements
in two or
more chan-
nels
at
once,
so
that
the
EMA, orbit,
and
correlation
measurements mentioned above
can be
performed.
As
with single-channel
FFTs,
any
type
of
voltage-
output
transducer
can be
used, including velocity
probes.
The
more accurate accelerometers
and
dis-
placement proximity probes are, however, preferred.
Data
Types
and
Formats
Vibration test data
are
usually plotted
in
three
differ-
ent
forms:
• A
Cartesian plot
of
vibration amplitude versus fre-
quency ("signature
plot"
or
"spectrum").
Some-
times this plot
may be
combined with
a
plot
of the
phase angle (the "lag
angle"
from
application
of the
exciting force
to the
responding vibratory motion)
versus frequency.
It is
then called
a
"Bode
plot."
• A
Cartesian plot
of
vibration amplitude versus time,
similar
to a
typical oscilloscope trace
("time"
plot).
• A
polar plot
of
vibration versus time
in a
plane per-
pendicular
to the
shaft
axis
(an
"orbit").
The
amplitude scales
may be
linear
or dB
(base
10
logarithm).
A dB
scale
is
often
used
to
improve
the
resolution
of
natural
frequency
peaks.
The
amplitude
scale generally represents
rms
(root mean square) val-
ues
unless specifically
scaled
otherwise.
To
convert
rms
values
at a
specific
frequency
to
peak
to
peak,
multiply
by
2.83,
and to
convert
from
peak
to
peak
to
zero
to
peak, divide
by 2.