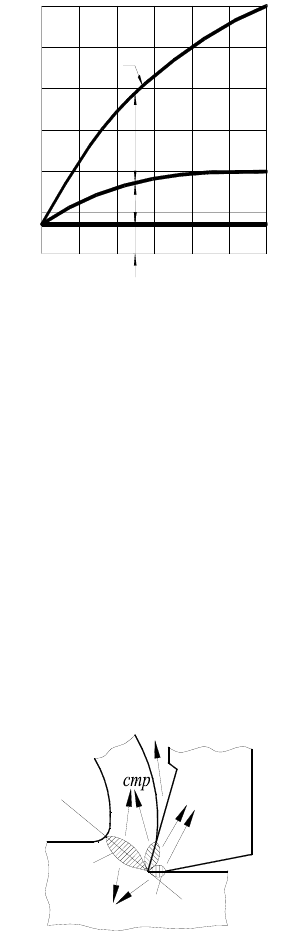
5.7.Тепловые явления при резании металлов
Механическая энергия, расходуемая на процесс резания, в основном пре-
вращается в теплоту, а многие экономические и технические проблемы меха-
нической обработки вызваны прямо или косвенно этим тепловым воздействи-
ем. Стоимость механической обработки в значительной степени зависит от
скорости съема металла и может быть уменьшена за счет увеличения скорости
резания и
подачи (независимо или совместно), верхний предел которых обу-
словлен резким снижением стойкости инструмента. Это обстоятельство не яв-
ляется основным ограничением при резании сплавов алюминия и магния, при
обработке которых возникает проблема удаления большого количества быстро
сходящей стружки, что может ограничить скорость съема металла При обра-
ботке стали и чугуна, а также
никелевых сплавов, имеющих более высокую
температуру плавления, инструменты нагреваются до высоких температур с
увеличением скорости съема, и при превышении определенной критической
скорости наступает их быстрое разрушение под воздействием напряжений и
температуры.
Ограничения, налагаемые возникающей при резании температурой, явля-
лись стимулом для разработки инструментальных материалов за последние 80
лет. Однако проблемы остались
и даже при современных инструментальных
материалах скорости резания ограничены.
Поэтому важно оценить факторы, влияющие на тепловыделение, распреде-
ление теплоты и распределение температуры в инструментах, стружке и заго-
товке вблизи режущей кромки.
Теплообразование оказывает двойное воздействие на резание. С одной сто-
роны, интенсивное тепловыделение облегчает деформирование материала сре-
заемого слоя, способствует образованию
промежуточного (окисленного) слоя
на контактных поверхностях стружки и заготовки, что приводит к уменьшению
износа инструмента, увеличению его стойкости, повышению качества обрабо-
танной поверхности и производительности. С другой стороны, повышение тем-
пературы в зоне резания до 800…1000
о
С может привести к отпуску материала
инструмента и разупрочнить резец, что приводит к его интенсивному изнаши-
ванию. Кроме того, теплота может стать причиной изменения действительных
размеров детали вследствие увеличения размеров инструмента до 0,03…0,04
мм.
Тепловыми явлениями при резании необходимо управлять так, чтобы вы-
деляющаяся теплота облегчала резание, но при этом не снижала
стойкость ин-
струментов и точность обработки, имеющих особое значение при работе стан-
ков-автоматов и полуавтоматов с ЧПУ.
Почти вся механическая энергия при резании переходит в тепловую и толь-
ко небольшая часть накапливается в поверхностном слое заготовки в виде по-
тенциальной энергии искаженной решетки материала (рис. 31).
00,2 0,60,4
100
200
h, мм
0, 8 1,0
300
400
500
600
с
d
f
e
Рис.31. Распренделение работы резания при обработке штамповых сталей для горячего
деформирования ( σ
b
= 800 Мпа ) в зависимости от толщины стружки: υ = 100 м/мин t = 4,25 мм,
α = 5˚, γ = 10˚; с – общая работа; d – работа упруго-пластических деформаций; e – работа трения
по первой поверхности; f – работа трения по задней поверхности
Источниками теплоты при резании являются пластическое деформирова-
ние в зоне стружкообразования, трение стружки о переднюю поверхность ин-
струмента и трение поверхности резания и обработанной поверхности о зад-
ние поверхности лезвия инструмента (рис. 32). Теплообразованием за счет
упругих деформаций и размельчением стружки обычно пренебрегают ввиду
их незначительности (менее 1%).
Уравнение теплового баланса можно
предоставить следующим образом:
Q
D
Q
тп
+ Q
тз
= Q
и
+ Q
окр
+ Q
3
+ Q
стр
,
Где Q
D –
количество теплоты, выделяющееся при пластическом деформи-
ровании обрабатываемого материала; Q
тп
– количество теплоты, выделяющее-
ся при трении стружки о переднюю поверхность резца; Q
тз
– количество теп-
лоты, выделяющееся при трении задних поверхностей резца от заготовку; Q
и
–
количество теплоты, уходящей в инструмент; Q
окр
, Q
3
, Q
стр
– количество теп-
лоты, передаваемой окружающей среде, заготовка и стружка, соответственно.
0
0
Q
σ
Q
з
тз
Q
и
Q
Q
окр
Q
Рис.32. Схема распределения теплоты при резании