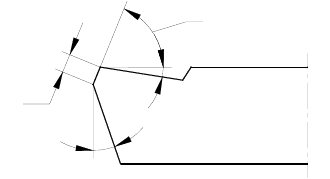
5.5. Вибрации при резании
В процессе резания в системе СПИД (станок – приспособление – инстру-
мент – деталь) при определенных условиях возникают вибрации – периодиче-
ские колебательные движения.
Вибрации при резании являются вредным явлением, так как они увеличи-
вают износ режущих инструментов, особенно твердосплавных и керамических,
снижают долговечность металлорежущих станков. При вибрации возникает
утомляющий работающих шум и ухудшается качество
обработанной поверхно-
сти. Вибрации могут значительно увеличивать напряжения в деталях станка. В
ряде случаев вибрации могут привести к снижению производительности, так
как в целях их устранения приходится работать с заниженными режимами ре-
зания.
Вибрации в горизонтальной плоскости, в направлении действия силы F
у
,
совершаются в основном за счет колебаний обрабатываемой детали, а в верти-
кальной плоскости, в направлении действия силы Р - за счет колебаний резца.
Обрабатываемая деталь и резец могут также одновременно совершать колеба-
ния в двух плоскостях. Обработанная поверхность при работе с вибрациями
представляет собой волнистую поверхность.
Вибрации бывают двух видов: вынужденные –
от внешней периодически
действующей возмущающей силы; автоколебания, совершающиеся без дейст-
вия внешней периодически возмущающейся силы.
Причинами вынужденных колебаний системы СПИД являются: неуравно-
вешенность вращающихся частей станка, приспособлений, заготовки и инстру-
мента; дефекты передач станка; колебания близко расположенного оборудова-
ния; условия резания (неравномерный припуск, прерывистый характер резания
и т.д.)
Методы борьбы
с вынужденными колебаниями сводятся к балансировке
инструмента и заготовок; виброизоляции фундаментов станков; применению
виброопор и т.д., т.е. к устранению причин, вызывающих возмущающую силу.
Основными причинами автоколебаний являются: образование нароста на
передней поверхности инструмента и периодический его срыв, приводящие к
изменению силы Р
z
; неравномерное упрочнение срезаемого слоя по его толщи-
не; вибрационные следы предыдущих рабочих ходов; изменение силы трения
на рабочих поверхностях инструмента; изменение площади среза или измене-
ние углов инструмента в процессе резания, или того и другого вместе.
Опытами установлено, что при работе с относительно низкими скоростями
резания возникают низкочастотные вибрации (до 1
кГп), при работе с высоки-
ми скоростями резания – высокочастотные (жл 6 кГп). Частота первых колеба-
ний близка к частоте собственных колебаний обрабатываемой детали, а частота
вторых колебаний близка к частоте собственных колебаний резца.
Исследования показали, что низкочастотные вибрации не влияют на стой-
кость как быстрорежущих, так и твердосплавных резцов. Высокочастотные
вибрации оказывают
значительное влияние на стойкость твердосплавных рез-
цов, которая может снизиться в 5 раз. Это объясняется ударным приложением
силы резания, вызывающей мелкие выкрашивания твердого сплава.
Основные способы повышения устойчивости процесса резания, устра-
няющие или уменьшающие вибрации, следующие.
Правильный выбор параметров системы СПИД (жесткости, сопротивле-
ния и массы), для чего применяются демпфирующие прокладки,
легкие па-
троны, короткие и жесткие инструменты.
Использование рациональных схем обработки, обеспечивающих макси-
мальное использование динамических свойств системы СПИД. Например,
вертикальное фрезерование обеспечивает более спокойные условия резания,
чем горизонтальное.
Правильный выбор геометрических элементов режущей части инструмен-
тов и режимов резания. (Увеличение скорости резания приводит сначала к
увеличению, а затем к уменьшению
автоколебаний, уменьшает автоколеба-
ния. Увеличение глубины резания снижает вибрации).
Наложение на инструмент звуковых и ультразвуковых искусственных ко-
лебаний в направлении движения подачи (осевых колебаний) или главного
движения (тангенциальных колебаний).
Применение специальных виброгасителей. При низкочастотных вибраци-
ях применяют резцы с виброгасящей фаской (рис. 28).
γ
γ =−85°
Φ
α
f
Рис.28. Резец с виброгасящей фаской ƒ
5.6. Качество обработанной поверхности
Качество обработанной поверхности во многом определяет эксплуатаци-
онные свойства деталей машин (коррозионную стойкость, износостойкость,
усталостную прочность и др.).