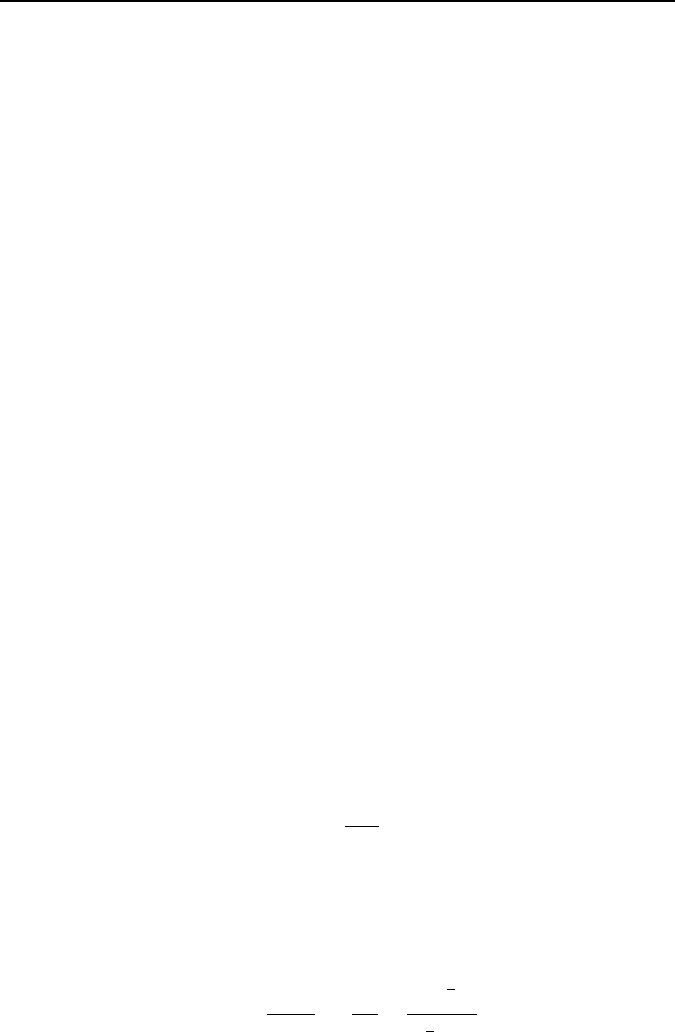
5 Surface Integrity of Machined Surfaces 157
through plastic deformation. Burnishing is used to improve surface finish, control
tolerance, increase surface hardness, and induce compressive residual stresses in
order to improve fatigue life. Turned, bored and milled surfaces with roughnesses
between 2 and 5
μm are suitable for burnishing because they have uniform as-
perities. When the initial surface roughness is R
a
=
1.5−2.0
μm, it is reduced down to
0.05−0.3(0.5)
μm (Figure 5.16(b)) by single or multipass operations and the bearing
length ratio t
p
30 can approach 30−50%, as shown in Figure 5.16(b). Part dimen-
sional accuracies can often be controlled within ±5
μm with proper part preparation.
5.2.6 Grinding Operations
Grinding is often used to produce parts with fine surface finishes and tight toler-
ances. As can be seen in Figure 5.4 ground surfaces with 0.1
μm R
a
roughness and
IT6(5) dimension tolerance are achievable. Typical grinding operations are used to
produce surface finish of 1.6−0.1
μm R
a
that corresponds to IT (8-5) ISO tolerance.
The surface profile contains randomly distributed irregularities and texture lays
depend on the grinding method used (they are parallel in cylindrical grinding, ra-
dial in face grinding, concentric in cup grinding). Figures 5.17 and 5.18 present
exemplary surface topographies and optical images of ground surfaces under de-
fined operation conditions, along with sets of appropriate 3D roughness parameters
and characteristic surface features.
When the wheel is dressed frequently so the wheel wear is not a significant
variable, the ground surface finish depends primarily on the grinding conditions,
wheel type and wheel dressing method. In particular, smoother surface finishes are
usually obtained with fine-grained wheels; as the wheel grit size increases, the
effective spacing of cutting edges decreases, so the roughness peaks are more
closely spaced and thus shorter. Also, a smoother finish is usually obtained if the
wheel hardness increases. Finally, it should be noted that the ground surface finish
deteriorates markedly if chatter occurs.
A number of equations for the geometric roughness in grinding have been
proposed [6]. For example, the theoretical R
a
value in cylindrical plunge grinding
can be estimated by the equation
x
v
av
RR
⎥
⎦
⎤
⎢
⎣
⎡
=
s
w
1at
, (5.6)
where: v
w
is the workpiece velocity, v
s
is the wheel velocity, a is the depth of cut
during the spark-out phase, and R
1
is empirical coefficient and exponent x=0.15−0.6.
On the other hand, this roughness parameter in cylindrical grinding can be
calculated as follows:
0.13
bm
6
1
eq
3
1
'
n
3.0
fd
d
5.0
fd
3at
HRC
2
VD
F
v
av
KR
⎟
⎟
⎠
⎞
⎜
⎜
⎝
⎛
⎟
⎠
⎞
⎜
⎝
⎛
=
ρ
, (5.7)
where: K
3
is a constant that considers wheel characteristic, 2
ρ
(d
g
) is the grain
diameter, v
fd
is feed during wheel dressing, a
d
is the depth of cut during the spark-