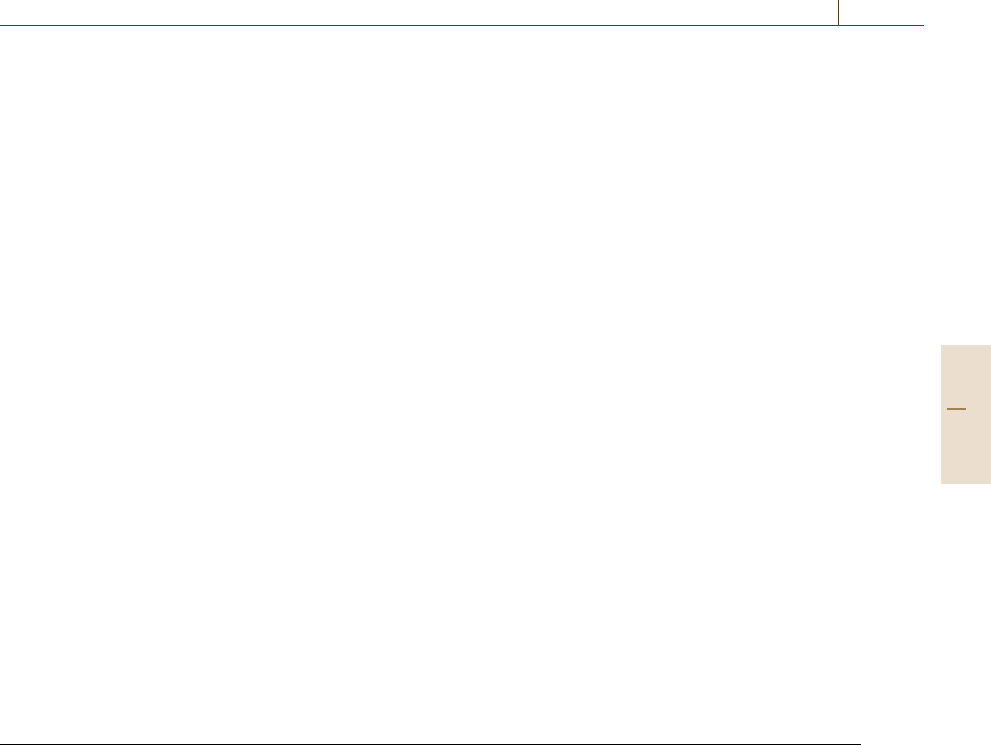
Industrial Intelligent Robots References 363
21.7 Conclusion
The intelligent robot appeared on the factory floor
at the beginning of 2000 and has vision and force
sensors. It can work unattended at night and during hol-
idays because it reduces manual preparations such as
arrangement of workpieces and/or the necessity of sys-
tem monitoring compared with the conventional robot.
Thus, the use efficiency of equipment rises, machin-
ing and assembly costs can be reduced, and the global
competitiveness of a product can be improved.
The industrial intelligent robots still have tasks
in which they cannot compete with skilled workers,
though they have a high level of skills, as has been
explained so far. The assembly task of flexible objects
such as wire-harnesses is one such task. There are sev-
eral on-going research and development activities in the
world to solve these challenges. One idea is to automate
such a task completely, and another is to do it partially.
In the latter case, robots and skilled workers work to-
gether; robots assemble mechanical parts and skilled
workers assemble flexible parts, for example. In any
case, the degree of cooperation between humans and
robots will increase in the near future.
21.8 Further Reading
•
Y. Bar-Cohen, C. Breazeal: Biologically Inspired In-
telligent Robots (SPIE Press, Bellingham 2003)
•
G.A. Bekey: Autonomous Robots: From Biologi-
cal Inspiration toImplementation and Control (MIT
Press, Cambridge 2005)
•
J.M. Holland: Designing Autonomous Mobile
Robots: Inside the Mind of an Intelligent Machine
(Newnes, Amsterdam 2003)
•
S.C. Mukhopadhyay, G.S. Gupta: Autonomous
Robots and Agents (Springer, New York 2007)
•
S.Y. Nof (Ed.): Handbook of Industrial Robotics
(Wiley, New York 1999)
•
R. Siegwart, I.R. Nourbakhsh: Introduction to Au-
tonomous Mobile Robots (MIT Press, Cambridge
2004)
•
P. Stone: Intelligent Autonomous Robotics: A Robot
Soccer Case Study (Morgan Claypool, San Rafael
2007)
References
21.1 D.E. Whitney: Historical perspective and state of
the art in robot force control, Proc. IEEE Int. Conf.
Robot. Autom. ICRA (1985)
21.2 T. Suehiro, K. Takase: Skill based manipulation
system, J. Robot. Soc. Jap. 8(5), 551–562 (1990)
21.3 M.T. Mason: Compliance and force control for com-
puter controlled manipulators, IEEE Trans. Syst.
Man Cybern. 11(6), 418–432 (1981)
21.4 N. Hogan: Impedance control, Part 1–3, Trans. ASME
J. Dyn. Syst. Meas. Control 107, 1–24 (1985)
21.5 J.J. Craig, P. Hsu, S. Sastry: Adaptive control of
mechanical manipulators, Int. J. Robot. Res. 6(2),
16–28 (1987)
21.6 B. Yao, M. Tomizuka: Adaptive coordinated control
of multiple manipulators handling a constrained
object, Proc. IEEE Conf. Robot. Autom. (1993)
21.7 S. Inaba: Assembly of robots by AI robot, Proc.
22nd IEEE IECON (Int. Conf. Ind. Electron. Control
Instrum.), Vol. 1 (1996) pp. xxxvii–xl
21.8 S. Sakakibara, A. Terada, K. Ban: An innovative
automatic assembly system where a two-armed
intelligent robot builds mini robots, Proc. 27th ISIR
(1996) pp. 937–942
21.9 S. Sakakibara: Intelligent assembly system suited
for module assembly, Proc. 30th ISR (1999) pp. 385–
390
21.10 S. Sakakibara: The role of intelligent robot in man-
ufacturing system of the 21st century, Proc. 32nd ISR
(2001)
21.11 K. Hariki, K. Yamanashi, K. Otsuka, M. Oda: In-
telligent robot cell, FANUC Tech. Rev. 16(1), 37–42
(2003)
Part C 21