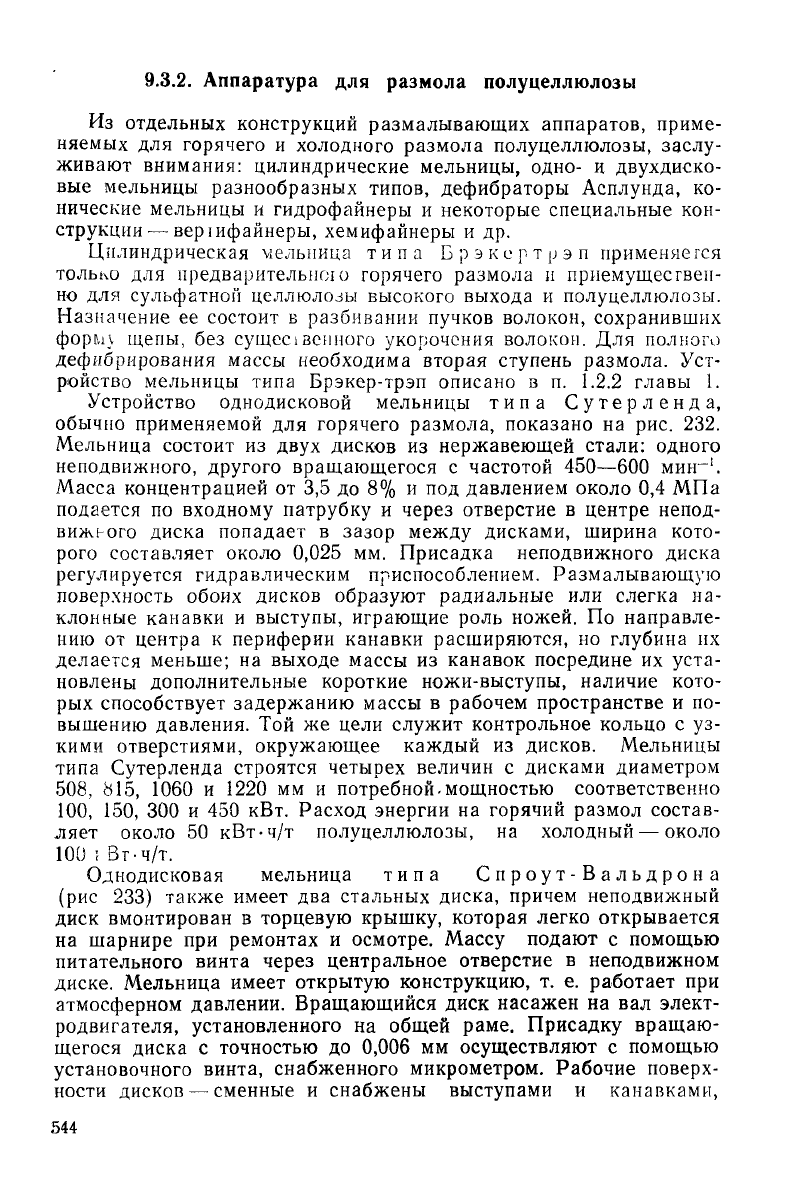
9.3.2.
Аппаратура
для
размола
полуцеллюлозы
Из
отдельных
конструкций размалывающих аппаратов, приме-
няемых
для
горячего
и
холодного размола полуцеллюлозы, заслу-
живают
внимания:
цилиндрические мельницы, одно-
и
двухдиско-
вые
мельницы разнообразных типов,
дефибраторы
Асплунда,
ко-
нические
мельницы
и
гидрофайнеры
и
некоторые специальные кон-
струкции—
вер!ифайнеры,
хемифайнеры
и др.
Цилиндрическая
мельница
типа
Б
р
экер
т
рэп
применяется
только
для
предварительною горячего размола
и
приемущесгвеи-
но
для
сульфатной целлюлозы высокого выхода
и
полуцеллюлозы.
Назначение
ее
состоит
в
разбивании
пучков волокон, сохранивших
форм>
щепы,
без
сущес1венного
укорочения
волокон.
Для
полного
дефибрирования массы необходима
вторая
ступень
размола.
Уст-
ройство мельницы
типа
Брэкер-трэп описано
в
п.
1.2.2 главы
1.
Устройство
однодисковой
мельницы типа
Сутерленда,
обычно
применяемой
для
горячего размола, показано
на
рис. 232.
Мельница
состоит
из
двух
дисков
из
нержавеющей
стали:
одного
неподвижного,
другого вращающегося
с
частотой
450—600
мин-
1
.
Масса концентрацией
от 3,5 до 8% и под
давлением около
0,4 МПа
подается
по
входному патрубку
и
через
отверстие
в
центре непод-
вижюго
диска попадает
в
зазор
между
дисками, ширина кото-
рого составляет около
0,025
мм.
Присадка неподвижного диска
регулируется гидравлическим приспособлением. Размалывающую
поверхность обоих дисков
образуют
радиальные
или
слегка
на-
клонные
канавки
и
выступы, играющие роль ножей.
По
направле-
нию
от
центра
к
периферии канавки расширяются,
но
глубина
их
делается меньше;
на
выходе массы
из
канавок посредине
их
уста-
новлены
дополнительные короткие ножи-выступы, наличие кото-
рых
способствует задержанию массы
в
рабочем пространстве
и по-
вышению давления.
Той же
цели служит контрольное кольцо
с уз-
кими
отверстиями, окружающее каждый
из
дисков. Мельницы
типа Сутерленда строятся четырех величин
с
дисками диаметром
508,
815,
1060
и
1220
мм и
потребной.мощностью
соответственно
100, 150,
300 и 450
кВт.
Расход
энергии
на
горячий размол состав-
ляет
около
50
кВт-ч/т
полуцеллюлозы,
на
холодный
—
около
100
;
Вт-ч/т.
Однодисковая мельница типа Спроут-Вальдрона
(рис
233) также имеет
два
стальных диска, причем неподвижный
диск вмонтирован
в
торцевую
крышку, которая
легко
открывается
на
шарнире
при
ремонтах
и
осмотре.
Массу
подают
с
помощью
питательного винта через центральное
отверстие
в
неподвижном
диске.
Мельница имеет открытую конструкцию,
т. е.
работает
при
атмосферном давлении. Вращающийся
диск
насажен
на вал
элект-
родвигателя, установленного
на
общей
раме.
Присадку вращаю-
щегося диска
с
точностью
до
0,006
мм
осуществляют
с
помощью
установочного винта, снабженного микрометром.
Рабочие
поверх-
ности
дисков
—
сменные
и
снабжены выступами
и
канавками,
544