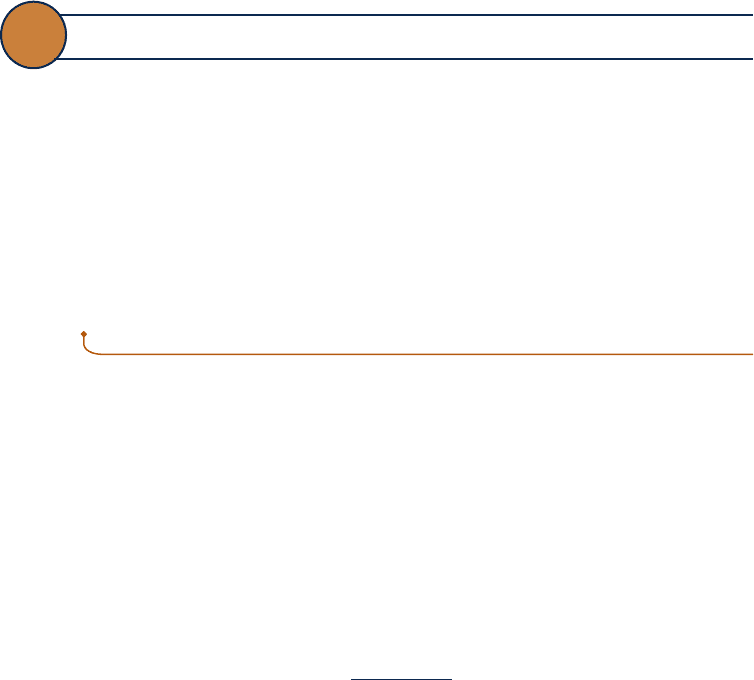
from state 3 to state 4 at temperature T
H
, and constant-volume cooling from state 4
to state 1 to complete the cycle.
A regenerator whose effectiveness is 100% allows the heat rejected during Process
4–1 to provide the heat input in Process 2–3. Accordingly, all the heat added to the
working fluid externally takes place in the isothermal process 3–4 and all the heat
rejected to the surroundings occurs in the isothermal process 1–2.
It can be concluded, therefore, that the thermal efficiency of the Stirling cycle is
given by the same expression as for the Carnot and Ericsson cycles. Since all three
cycles are reversible, we can imagine them as being executed in various ways, includ-
ing use of gas turbines and piston–cylinder engines. In each embodiment, however,
practical issues prevent it from actually being realized.
STIRLING ENGINE. The Ericsson and Stirling cycles are principally of theoreti-
cal interest as examples of cycles that exhibit the same thermal efficiency as the
Carnot cycle. However, a practical engine of the piston–cylinder type that operates
on a closed regenerative cycle having features in common with the Stirling cycle has
been under study for years. This engine is known as a Stirling engine. The Stirling
engine offers the opportunity for high efficiency together with reduced emissions
from combustion products because combustion takes place externally and not within
the cylinder as for internal combustion engines. In the Stirling engine, energy is trans-
ferred to the working fluid from products of combustion, which are kept separate. It
is an external combustion engine.
Stirling engine
9.9 Gas Turbine–Based Combined Cycles
In this section, gas turbine–based combined cycles are considered for power genera-
tion. Cogeneration, including district heating, is also considered. These discussions
complement those of Sec. 8.5, where vapor power system performing similar functions
are introduced.
The present applications build on recognizing that the exhaust gas temperature of
a simple gas turbine is typically well above ambient temperature and thus hot gas
exiting the turbine has significant thermodynamic utility that might be harnessed
economically. This observation provides the basis for the regenerative gas turbine
cycle introduced in Sec. 9.7 and for the current applications.
9.9.1
Combined Gas Turbine–Vapor Power Cycle
A combined cycle couples two power cycles such that the energy discharged by heat
transfer from one cycle is used partly or wholly as the heat input for the other cycle.
This is illustrated by the combined cycle involving gas and vapor power turbines shown
in Fig. 9.22. The gas and vapor power cycles are combined using an interconnecting
heat-recovery steam generator that serves as the boiler for the vapor power cycle.
The combined cycle has the gas turbine’s high average temperature of heat addi-
tion and the vapor cycle’s low average temperature of heat rejection, and thus a
thermal efficiency greater than either cycle would have individually. For many appli-
cations combined cycles are a good choice, and they are increasingly being used
worldwide for electric power generation.
With reference to Fig. 9.22, the thermal efficiency of the combined cycle is
h 5
W
#
gas
1 W
#
vap
Q
#
in
(9.28)
where W
#
gas
is the net power developed by the gas turbine and W
#
vap
is the net power
developed by the vapor cycle. Q
#
in
denotes the total rate of heat transfer to the com-
bined cycle, including additional heat transfer, if any, to superheat the vapor entering
9.9 Gas Turbine–Based Combined Cycles 537
c09GasPowerSystems.indd Page 537 7/19/10 9:51:06 AM users-133 c09GasPowerSystems.indd Page 537 7/19/10 9:51:06 AM users-133 /Users/users-133/Desktop/Ramakant_04.05.09/WB00113_R1:JWCL170/New/Users/users-133/Desktop/Ramakant_04.05.09/WB00113_R1:JWCL170/New