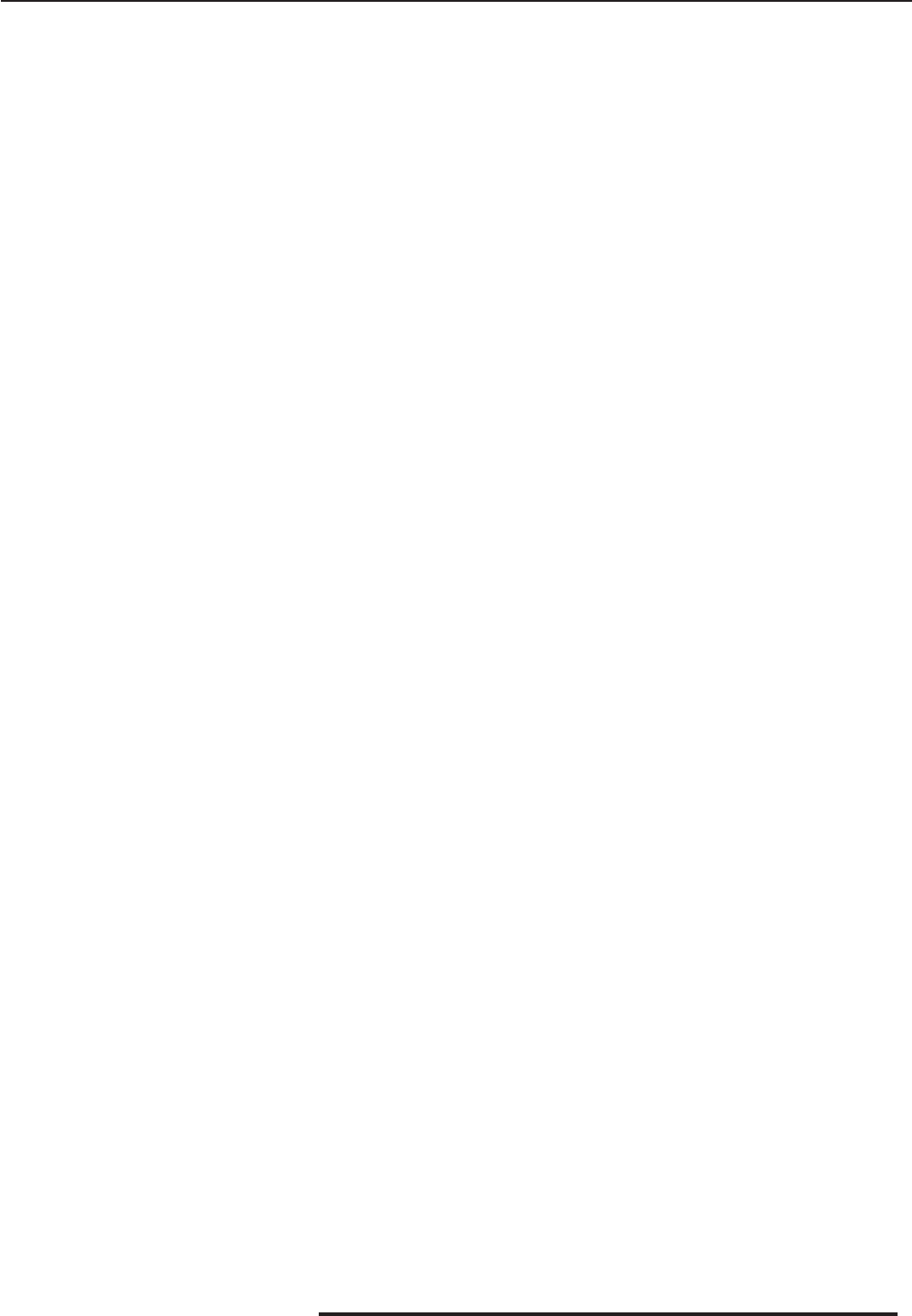
I l%2 ++30#(7%1* ? ( #.0-.03$- ? /0.,;8+%--.12</2010
2
70
СТАЛЕПЛАВИЛЬНОЕ ПРОИЗВОДСТВО
ностью соответствуют техническим условиям и сер-
тификатным данным. Указанные дефекты выявляют-
ся при коррозионных испытаниях и считаются бра-
ковочным признаком. Очевидно, что присутствие
КАНВ в таких сталях недопустимо, а это связано с
технологией и ее исполнением. Проблема КАНВ ре-
шается при использовании комплексных модификато-
ров, включающих кальций и редкоземельные метал-
лы (РЗ
М). Проведенные на одном из предприятий ис-
следования показали, что при расходе проволоки с на-
полнением комплексным модификатором (РЗМ 12 %,
Са 12 %, Si 45 %) 0,04–0,06 кг/т по РЗМ, общая за-
грязненность трубной стали (сталь 20 СА) неметал-
лическими включениями снижается в 1,5–2,0 раза, за-
грязненность по сульфидам в 2,0–3,0 раза, при этом
КАНВ практически не наблюдаются. Проведенные
в да
льнейшем исследования с расходом проволоки
0,15–0,20 кг/т по РЗМ показали, что стали с системой
легирования Fe-Cr (13ХФА), модифицированные це-
рием и лантаном (содержание Се в готовом металле
составляет 0,0050–0,0060 %, La – 0,0015–0,0040 %)
являются устойчивыми к бактериальной коррозии,
т.к. адгезионные свойства сульфатредуцирующих
бактерий уменьшаются в результате модификации
формы и размеров включений. Плотность биопленки
на опытных образцах мет
алла труб в 2–3 раза мень-
ше, чем на металле плавок, модифицированных толь-
ко Са, водородные трещины и блистиринги на образ-
цах отсутствуют, скорость общей коррозии составля-
ет 0,5 мм/год, пороговое напряжение 80 % от порога
текучести.
В настоящее время технология производства ста-
лей с повышенными требованиями по обрабатыва-
емости (с нормированным со
держанием S) уже не
мыслится без использования кальцийсодержащих и
серосодержащих порошковых проволок. Технология
получения таких сталей, как правило, предусматрива-
ет первоначальное проведение десульфурации жид-
кой стали до содержания S 0,015–0,020 %, затем об-
работку кальцийсодержащей проволокой в два этапа
(первый для рафинирования, второй для модифици-
рования) и после этого легирование металла S из про-
волоки до заданног
о содержания. На РУП «БМЗ» та-
кая технология обеспечивает полное модифицирова-
ние и глобуляризацию неметаллических включений
перед легированием металла S, что приводит к зна-
чительному снижению загрязненности металла неме-
таллическими включениями, снижению поверхност-
ных дефектов, обеспечению разливаемости стали при
высоком содержании S и Al и сокращению брака бо-
лее чем в два раза, при эт
ом такие результаты достиг-
нуты при регламентированной интенсивности подачи
как Ca, так и S. Усвоение S из проволоки стабильное
и составляет 75–85 %.
Широко используется внепечное легирование ста-
ли Nb и V, несмотря на довольно высокое усвоение
этих элементов из кусковых ферросплавов (85–93 %).
В порошковой проволоке усвоение основных элемен-
тов составляет практически 100 %. Экономическая
эффективность достигается за счет гарантиров
ан-
ного получения заданного содержания элементов на
нижнем пределе нормативных требований и, соответ-
ственно, снижения норм расхода материалов.
Одним из перспективных направлений современ-
ной металлургии является микролегирование ста-
ли химически активными элементами, оказывающи-
ми эффективное влияние на формирование в сталях
структурного состояния, улучшающего комплекс по-
требительских свойств. Наряду с V, Nb, Ti, Mо в прак-
тик
е микролегирования широко применяется B. При
этом содержание B для различных марок стали и це-
лей должно строго регламентироваться, особенно по
верхнему пределу, что достигается вводом этого эле-
мента порошковой проволокой. Эта технология уже
длительное время используется, например, на Мол-
давском и Белорусском заводах, отработаны режи-
мы микролегирования металла B с остаточным ег
о
содержанием 0,001–0,008 % на сталях разных ма-
рок с различным содержанием Mn, Si и C в преде-
лах 0,04–0,45 %. Доказано положительное влияние B
на физико-механические и эксплуатационные харак-
теристики проката, катанки, проволоки и проволоч-
ных изделий. При этом достигается стабильно высо-
кое усвоение B в пределах 75,3–94,3 % в зависимости
от окисленности стали (α
о
= 3–10 ppm).
Незаменимым средством корректировки содер-
жания C в узких заданных пределах является порош-
ковая проволока с углеродсодержащим наполните-
лем. Степень усвоения C при корректировке его со-
держания на 0,02 или 0,03 % соответственно 92,4–100
и 93,5–100 % [2].
К настоящему времени на металлургических
предприятиях при использовании порошковой про-
волоки получены убедительные доказательства эф-
фективности новой технологии в возможности влия-
ния на к
ачество металла, снижения затрат при произ-
водстве стали и повышении конкурентоспособности
металлопродукции. Порошковая проволока не имеет
ограничений по составу и состоянию наполнителей и
в этом заложен большой потенциал этой технологии
и ее перспективность.
Библиографический список
1. Дюдкин Д.А., Кисиленко В.В. Особенности
усвоения кальция из порошковой проволоки с
комплексным наполнителем СК40 // Ме
талл и ли-
тье Украины. – 2009. – № 1-2. – С. 20–23.
2. Дюдкин Д.А., Кисиленко В.В., Павлюченков
И.А., Болотов В.Ю. Прецизионная обработка ме-
таллургических расплавов. – М.: Теплотехник,
2007. – 424 с.
3. Дюдкин Д.А., Кисиленко В.В. // Патент України
на корисну модель № 44822. Дріт для обробки
рідких металів кальцієм. – Бюл. № 19. – 2009.
4. Гасик Л.Н., Игна
тьев В.С., Гасик М.И. Структу-
ра и качество промышленных ферросплавов и ли-
гатур. – К.: Техніка, 1975. – 151 с.
5. Каблуковский А.Ф., Зинченко С.Д., Никулин
А.Н. и др. Внепечная обработка стали порошковой
проволокой. – М.: Металлургиздат, 2006. – 288 с.