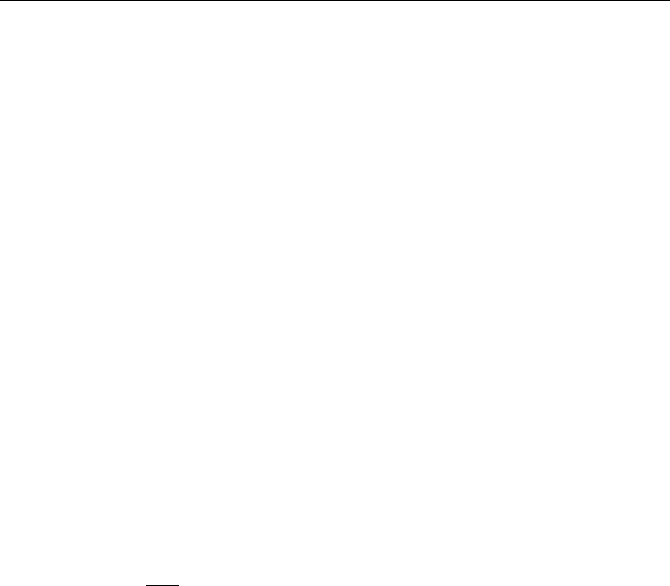
5 Hologram Simulation of Aluminum Reduction Cells
is the “Joule heat”. It can be solved from the Laplace equation of electrical
conduction, i.e. Eq. 5.3.
Eq. 5.52 and the electrical conduction equation can be solved with the implicit
finite difference format after the discretization. For a selected slice, except that the
collector bar is treated as a three-dimensional part, others are all regarded as
two-dimensional. The boundary conditions are the same as stated in Section 5.4.1.
The solving and analysis of the unsteady heat conduction equation are based on
“heat balance self-checking method”(Zuo, 1996). The procedure is:
a) According to the static analytic method, to determine a basic heat balance of
the aluminum cell under a given melt temperature.
b) Supposing that a disturbance will bring the heat to increase
0
QΔ in one
time step and make the melt temperature increase to WQTT /
001
Δ+= (W is the
“water equivalent” of the melt). Under these conditions, the electric field and
temperature field at next moment can be analyzed.
c) To estimate the volume of melted ledge, meanwhile, check the heat balance
and the melt temperature, then start the calculation of next time step.
Melting or freezing of the ledge will result in changes of its edge position,
which can be determined by the “moving boundary method”(You,1997). Take the
melting of the ledge as an example. When disturbances starts and the calculated
temperature of the boundary node exceeds
f
T , the extra enthalpy
Δ was
considered to melt the ledge in the control volume around the node. The melted
volume is
λ
H
G
Δ
=Δ
. With the melted volume, a new position of the ledge can
be decided. After several time steps, if the entire ledge in control volume of this
node all melts, the boundary should move to the next node in next step of the
computation. The same computation should be carried out at each node. After
several time steps (which is set as the simulation time in the programme), the
results of the freeze profile of the cell can be obtained and displayed on a
WINDOWS interface. For the process that the ledge freezes and gets thicker, the
computation is the same only the boundary moves in a reverse direction.
As the computation goes on, error will accumulate, thus result in a distortion of
the simulation results. It can be solved by periodically correcting the basic heat
balance offline with the measured electrolyze temperature and freeze profile. Or it
can be done by online correction with the cell wall temperatures (Zhou et al., 1998).
5.5.3
Technical scheme of the dynamic simulation and function
of the software system
According to above principles and models, in reference (Mei et al.,1998), the author
put forward a technical scheme of the dynamic simulation (as shown in Fig. 5.26).
The software system consists of six function modules, i.e., analysis of cell
conditions, dynamic simulation, examination and correction of static parameters,