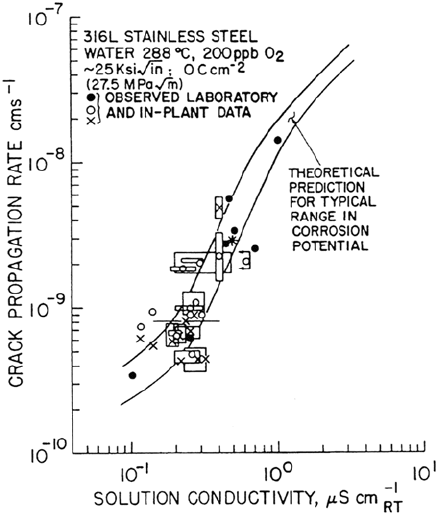
These formulations can become more complicated, e.g., for complex stress
fields adjacent to welds. Examination of Eq. (13) indicates that, at time zero, there
is an assumed intrinsic initiating defect, a
i
; in the following analyses for “smooth”
stainless steel components, a value of 50 μm has been used [2,10].
Equation (13), in conjunction with the variation in stress intensity as a crack
grows through a residual stress field adjacent to a weld, provides a prediction of the
effects of, e.g., (a) water purity on the crack depth–operating time for stainless steel
piping and (b) a range in residual stress on the predicted range of crack depths in a
piping system (Fig. 18). A range in actual system conditions inherently leads to a
predicted range in cracking response, as illustrated in Figure 19 for the theoretical
relationships between the coolant purity and the operating time required for a crack
to penetrate 25% of the wall thickness in a welded type 304 stainless steel pipe. These
theoretical relationships are shown for typical ranges in carbon contents (i.e., EPR
values) and in residual stress profiles. Figure 19 shows that the observed data
lie within the theoretical bounds. Thus, with this proven prediction capability,
quantitative decisions can be made about the future behavior for proposed
modifications in environment, material, or stress (Fig. 20).
Similar predictions can be made for the effect of irradiation on the
intergranular cracking susceptibility of stainless steel components in the reactor
core [114]. The prediction methodology developed for unirradiated conditions was
modified to account for the effect of fast neutron and gamma irradiation on (a)
Corrosion in Nuclear Systems 625
Figure 15 Observed and predicted relationships between the crack propagation rate and
solution conductivity for type 316L stainless steel under constant load (25 ksi √
—
in) in water
containing 200 ppm oxygen. (From Ref. 1).
Copyright © 2002 Marcel Dekker, Inc.