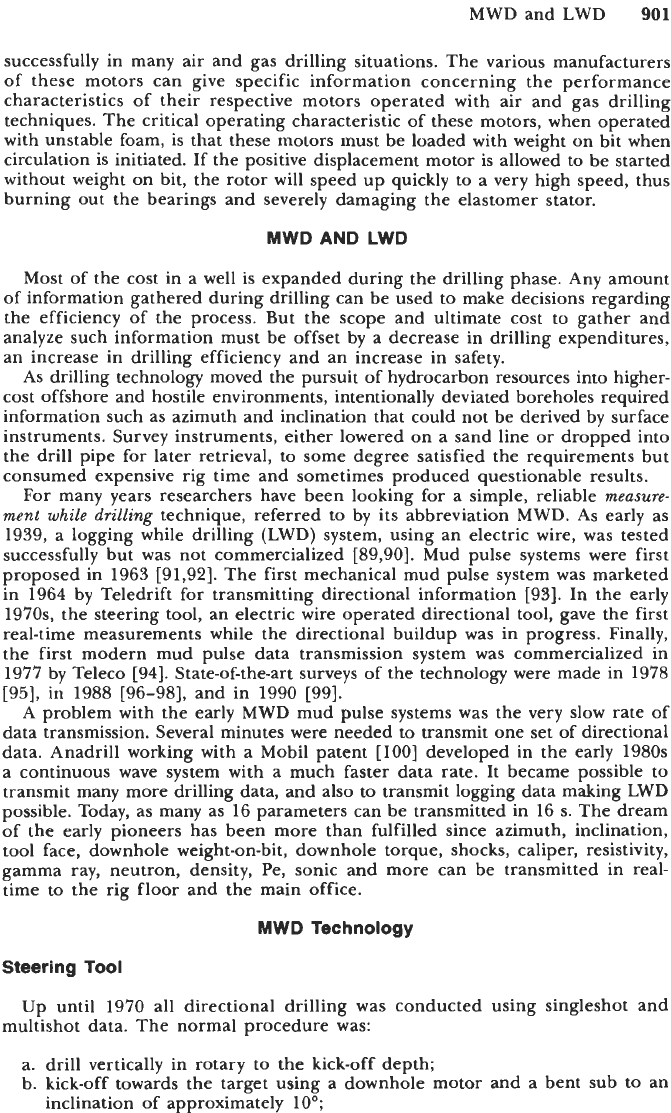
MWD and LWD
901
successfully in many air and gas drilling situations. The various manufacturers
of
these motors can give specific information concerning the performance
characteristics of their respective motors operated with air and gas drilling
techniques. The critical operating characteristic of these motors, when operated
with unstable foam, is that these motors must be loaded with weight on bit when
circulation is initiated. If the positive displacement motor is allowed to be started
without weight on bit, the rotor will speed up quickly to a very high speed, thus
burning out the bearings and severely damaging the elastomer stator.
MWD AND LWD
Most of the cost in a well is expanded during the drilling phase. Any amount
of information gathered during drilling can be used to make decisions regarding
the efficiency of the process. But the scope and ultimate cost to gather and
analyze such information must be offset by a decrease in drilling expenditures,
an increase in drilling efficiency and an increase in safety.
As drilling technology moved the pursuit of hydrocarbon resources into higher-
cost offshore and hostile environments, intentionally deviated boreholes required
information such as azimuth and inclination that could not be derived by surface
instruments. Survey instruments, either lowered on a sand line or dropped into
the drill pipe for later retrieval, to some degree satisfied the requirements but
consumed expensive rig time and sometimes produced questionable results.
For many years researchers have been looking for a simple, reliable
measure-
ment while drilling
technique, referred to by its abbreviation MWD. As early as
1939, a logging while drilling (LWD) system, using an electric wire, was tested
successfully but was not commercialized [89,90]. Mud pulse systems were first
proposed in 1963 [91,92]. The first mechanical mud pulse system was marketed
in 1964 by Teledrift for transmitting directional information [93]. In the early
1970s, the steering tool, an electric wire operated directional tool, gave the first
real-time measurements while the directional buildup was in progress. Finally,
the first modern mud pulse data transmission system was commercialized in
1977 by Teleco [94]. State-of-the-art surveys of the technology were made in 1978
[95], in 1988 [96-981, and in 1990 [99].
A
problem with the early MWD mud pulse systems was the very slow rate of
data transmission. Several minutes were needed to transmit one set of directional
data. Anadrill working with a Mobil patent [loo] developed in the early 1980s
a continuous wave system with a much faster data rate. It became possible to
transmit many more drilling data, and also to transmit logging data making LWD
possible. Today, as many as 16 parameters can be transmitted in 16
s.
The dream
of the early pioneers has been more than fulfilled since azimuth, inclination,
tool face, downhole weight-on-bit, downhole torque, shocks, caliper, resistivity,
gamma ray, neutron, density, Pe, sonic and more can be transmitted in real-
time to the rig floor and the main office.
MWD Technology
Steering
Tool
Up until 1970 all directional drilling was conducted using singleshot and
multishot data. The normal procedure was:
a. drill vertically in rotary to the kick-off depth;
b. kick-off towards the target using a downhole motor and a bent sub to an
inclination of approximately 10';