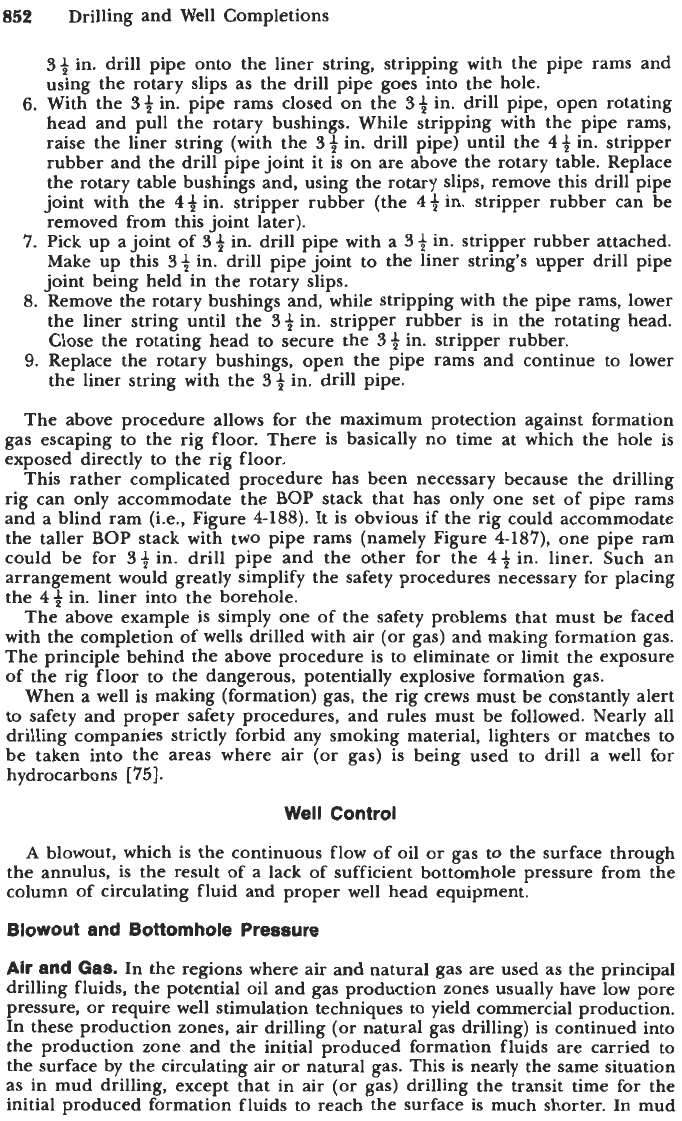
854
Drilling and Well Completions
33
in. drill pipe onto the liner string, stripping with the pipe rams and
using the rotary slips as the drill pipe goes into the hole.
6.
With the
33
in. pipe rams closed on the
33
in. drill pipe, open rotating
head and pull the rotary bushings. While stripping with the pipe rams,
raise
the
liner string (with the
3
+
in. drill pipe) until the 4
+
in. stripper
rubber and the drill pipe joint it
is
on
are
above the rotary table. Replace
the rotary table bushings and, using the rotary slips, remove this drill pipe
joint with the 43 in. stripper rubber (the 43 in. stripper rubber can be
removed from this joint later).
7. Pick up a joint of
34
in. drill pipe with a
34
in. stripper rubber attached.
Make up this
34
in. drill pipe joint to the liner string’s upper drill pipe
joint being held in the rotary slips.
8.
Remove the rotary bushings and, while stripping with the pipe rams, lower
the liner string until the
33
in. stripper rubber is in the rotating head.
Close the rotating head to secure the
33
in. stripper rubber.
9.
Replace the rotary bushings, open the pipe rams and continue to lower
the liner string with the
33
in. drill pipe.
The above procedure allows for the maximum protection against formation
gas escaping to the rig floor. There is basically no time at which the hole is
exposed directly to the rig floor.
This rather complicated procedure has been necessary because the drilling
rig can only accommodate the BOP stack that has only one set of pipe rams
and a blind ram (i.e., Figure
4-188).
It is obvious if the rig could accommodate
the taller BOP stack with two pipe rams (namely Figure 4-187), one pipe ram
could be for
33
in. drill pipe and the other for the
44
in. liner. Such an
arrangement would greatly simplify the safety procedures necessary for placing
the
44
in. liner into the borehole.
The above example is simply one of the safety problems that must be faced
with the completion of wells drilled with
air
(or
gas) and making formation gas.
The principle behind the above procedure is to eliminate or limit the exposure
of the rig floor to the dangerous, potentially explosive formation gas.
When
a
well is making (formation) gas, the rig crews must be constantly alert
to safety and proper safety procedures, and rules must be followed. Nearly all
drilling companies strictly forbid any smoking material, lighters
or
matches
to
be taken into the areas where air
(or
gas) is being used
to
drill a well for
hydrocarbons [75].
Well
Control
A
blowout, which is the continuous flow of oil
or
gas to the surface through
the annulus, is the result of a lack of sufficient bottomhole pressure from the
column of circulating fluid and proper well head equipment.
Blowout
and
Bottomhole
Pressure
Air
and
Gas.
In the regions where
air
and
natural gas
are
used as the principal
drilling fluids, the potential oil and gas production zones usually have low pore
pressure,
or
require well stimulation techniques
to
yield commercial production.
In these production zones, air drilling
(or
natural gas drilling) is continued into
the production zone and the initial produced formation fluids are carried to
the surface by the circulating air
or
natural gas. This is nearly the same situation
as in mud drilling, except that in air
(or
gas) drilling the transit time for the
initial produced formation fluids to reach the surface is much shorter. In mud