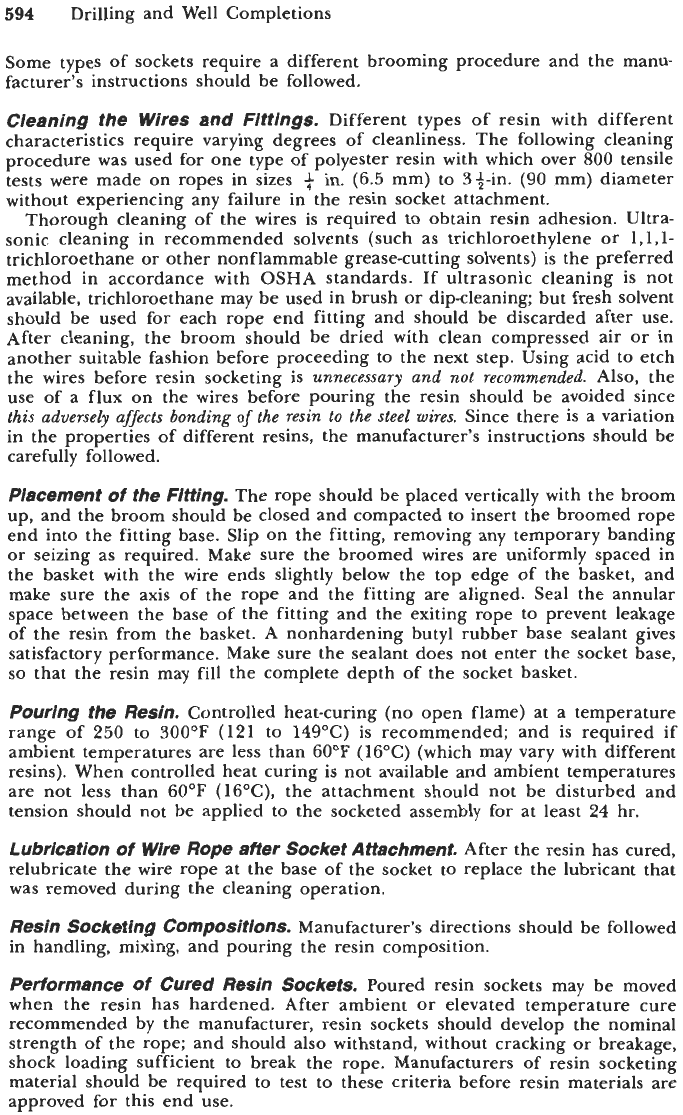
594
Drilling and Well Completions
Some types of sockets require a different brooming procedure and the manu-
facturer's instructions should be followed.
Cleaning the Wires and Fittings.
Different types of resin with different
characteristics require varying degrees of cleanliness. The following cleaning
procedure was used for one type of polyester resin with which over
800
tensile
tests were made on ropes in sizes
+
in.
(6.5
mm) to 34-in.
(90
mm) diameter
without experiencing any failure in the resin socket attachment.
Thorough cleaning of the wires is required to obtain resin adhesion. Ultra-
sonic cleaning in recommended solvents (such as trichloroethylene or l,l,l-
trichloroethane or other nonflammable grease-cutting solvents) is the preferred
method in accordance with
OSHA
standards. If ultrasonic cleaning is not
available, trichloroethane may be used in brush or dip-cleaning; but fresh solvent
should be used for each rope end fitting and should be discarded after use.
After cleaning, the broom should be dried with clean compressed air or in
another suitable fashion before proceeding to the next step. Using acid to etch
the wires before resin socketing is
unnecessary and
not
recommended.
Also, the
use of a
flux
on
the wires before pouring the resin should be avoided since
this adversely affects bonding of the resin to the steel wires.
Since there is a variation
in the properties of different resins, the manufacturer's instructions should be
carefully followed.
Placement
of
the Flttlng.
The rope should be placed vertically with the broom
up, and the broom should be closed and compacted to insert the broomed rope
end into the fitting base. Slip on the fitting, removing any temporary banding
or seizing as required. Make sure the broomed wires are uniformly spaced in
the basket with the wire ends slightly below the top edge of the basket, and
make sure the axis of the rope and the fitting are aligned. Seal the annular
space between the base of the fitting and the exiting rope to prevent leakage
of the resin from the basket.
A
nonhardening butyl rubber base sealant gives
satisfactory performance. Make sure the sealant does not enter the socket base,
so
that the resin may fill the complete depth of the socket basket.
Pouring the Resin.
Controlled heat-curing (no open flame) at
a
temperature
range of
250
to 300°F (121 to 149°C) is recommended; and is required if
ambient temperatures are less than 60°F (16°C) (which may vary with different
resins). When controlled heat curing is not available and ambient temperatures
are not less than 60°F (16"C), the attachment should not be disturbed and
tension should not be applied to the socketed assembly for at least
24
hr.
Lubricatlon
Of
Wire Rope
after
Socket Attachment.
After the resin has cured,
relubricate the wire rope at the base of the socket
to
replace the lubricant that
was removed during the cleaning operation.
Resin Socketing COmpOSitiOnS.
Manufacturer's directions should be followed
in handling, mixing, and pouring the resin composition.
Performance
of
Cured Resin Sockets.
Poured resin sockets may be moved
when the resin has hardened. After ambient or elevated temperature cure
recommended by the manufacturer, resin sockets should develop the nominal
strength of the rope; and should also withstand, without cracking
or
breakage,
shock loading sufficient to break the rope. Manufacturers of resin socketing
material should be required to test to these criteria before resin materials are
approved for this end use.