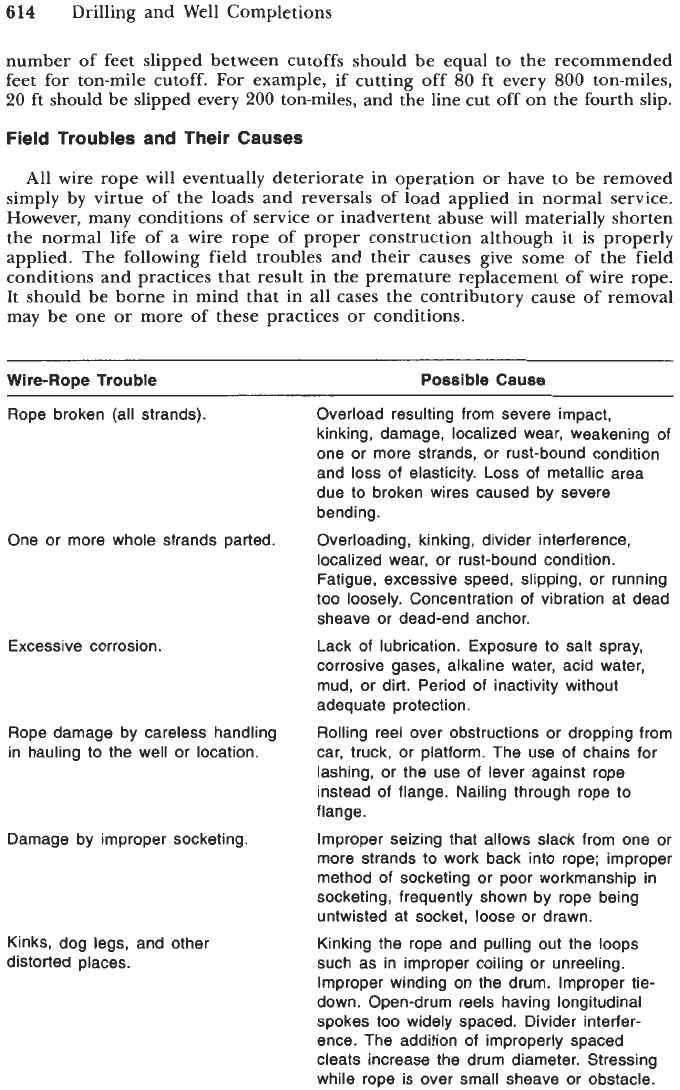
614
Drilling and Well Completions
number of feet slipped between cutoffs should be equal to the recommended
feet for ton-mile cutoff. For example,
if
cutting off
80
ft every
800
ton-miles,
20
ft
should be slipped every
200
ton-miles, and the line cut off
on
the fourth slip.
Field Troubles and Their Causes
All wire rope will eventually deteriorate in operation or have to be removed
simply by virtue of the loads and reversals of load applied in normal service.
However, many conditions of service or inadvertent abuse will materially shorten
the normal life of a wire rope of proper construction although it is properly
applied. The following field troubles and their causes give some of the field
conditions and practices that result in the premature replacement of wire rope.
It should be borne in mind that in all cases the contributory cause of removal
may be one or more of these practices
or
conditions.
Wire-Rope Trouble Possible Cause
Rope broken (all strands).
One or more whole strands parted.
Excessive corrosion.
Rope damage by careless handling
in hauling to the well or location.
Damage by improper socketing.
Kinks, dog legs, and other
distorted places.
Overload resulting from severe impact,
kinking, damage, localized wear, weakening of
one or more strands, or rust-bound condition
and
loss
of elasticity. Loss
of
metallic area
due to broken wires caused by severe
bending.
Overloading, kinking, divider interference,
localized wear, or rust-bound condition.
Fatigue, excessive speed, slipping, or running
too loosely. Concentration of vibration at dead
sheave or dead-end anchor.
Lack of lubrication. Exposure to salt spray,
corrosive gases, alkaline water, acid water,
mud, or dirt. Period
of
inactivity without
adequate protection.
Rolling reel over obstructions or dropping from
car, truck, or platform. The use
of
chains for
lashing, or the use of lever against rope
instead of flange. Nailing through rope to
flange.
Improper seizing that allows slack from one or
more strands to work back into rope; improper
method of socketing or poor workmanship in
socketing, frequently shown by rope being
untwisted at socket, loose or drawn.
Kinking the rope and pulling out the loops
such as in improper coiling or unreeling.
Improper winding on the drum. Improper tie-
down. Open-drum reels having longitudinal
spokes too widely spaced. Divider interfer-
ence. The addition of improperly spaced
cleats increase the drum diameter. Stressing
while rope is over small sheave or obstacle.