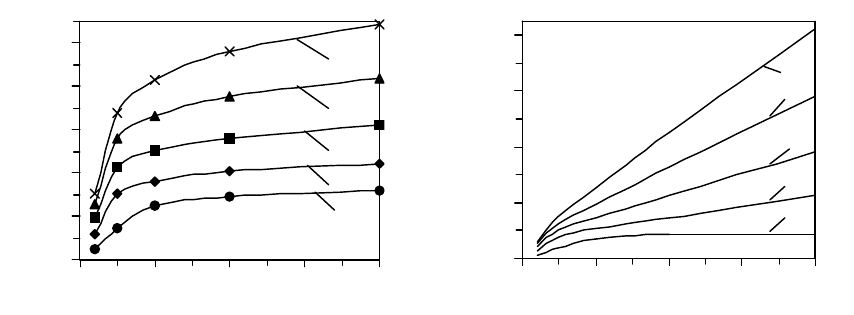
62
0
2
4
6
8
10
0 0,1 0,2 0,3 0,4
n
Dy·10
8
4
a)
0
4
8
12
16
0 0,1 0,2 0,3 0,4
n
Dх·10
7
2
3
б)
Рис. 13. Зависимости коэффициентов D
y
и D
x
от скорости вращения
червяка: а) глубина канала(мм): 1 – 5, 2 – 10, 3 – 15, 4 – 20, 5 – 25;
б) ширина канала(мм): 1 - 5, 2 – 10, 3 – 15, 4 – 20, 5 – 25
Реакционная смесь, состоящая из раствора мономеров с
растворённым в нём инициатором, непрерывно подавалась в экструдер с
помощью перистальтического насоса. Образцы экструдата собирались в
стеклянные бюксы и охлаждались для остановки реакции. Конверсия
определялась по остаточному содержанию непрореагировавшего мономера
титрованием. Через отверстие пробоотборника в средней части экструдера
также отбирались пробы реакционной массы. Варьировались
производительность экструдера и температура теплоносителя в рубашке
охлаждения.
В лабораторном экструдере валы не охлаждались, поэтому при
моделировании в уравнении (19) член, учитывающий перенос теплоты
вдоль оси х, не учитывался. Принималось, что перенос теплоты через
стенку вала (дно канала) отсутствует. Это обстоятельство имеет
следствием изменение граничного условия при у=0 на ∂t(y,τ)/∂y=0.
На рис. 14 приводится сопоставление опытных данных (точки) с
результатами моделирования (сплошные линии). Значения температуры и
конверсии реакционной массы, использованные в качестве начальных
условий при решении уравнений модели, были определены
экспериментально. Начальное значение температуры реакционной массы
оказалось близким к температуре теплоносителя. Это объясняется её
нагревом во входном штуцере вследствие малой скорости течения.
Опытные данные удовлетворительно коррелируются с расчётными.
Увеличение производительности экструдера приводит к снижению
степени конверсии экструдата. Разность максимальной и средней по
глубине канала температур, прогнозируемая по математической модели,
составляет в среднем около 5
о
С и повышается в направлении к выходу из
экструдера. Увеличение скорости полимеризации и рост температуры