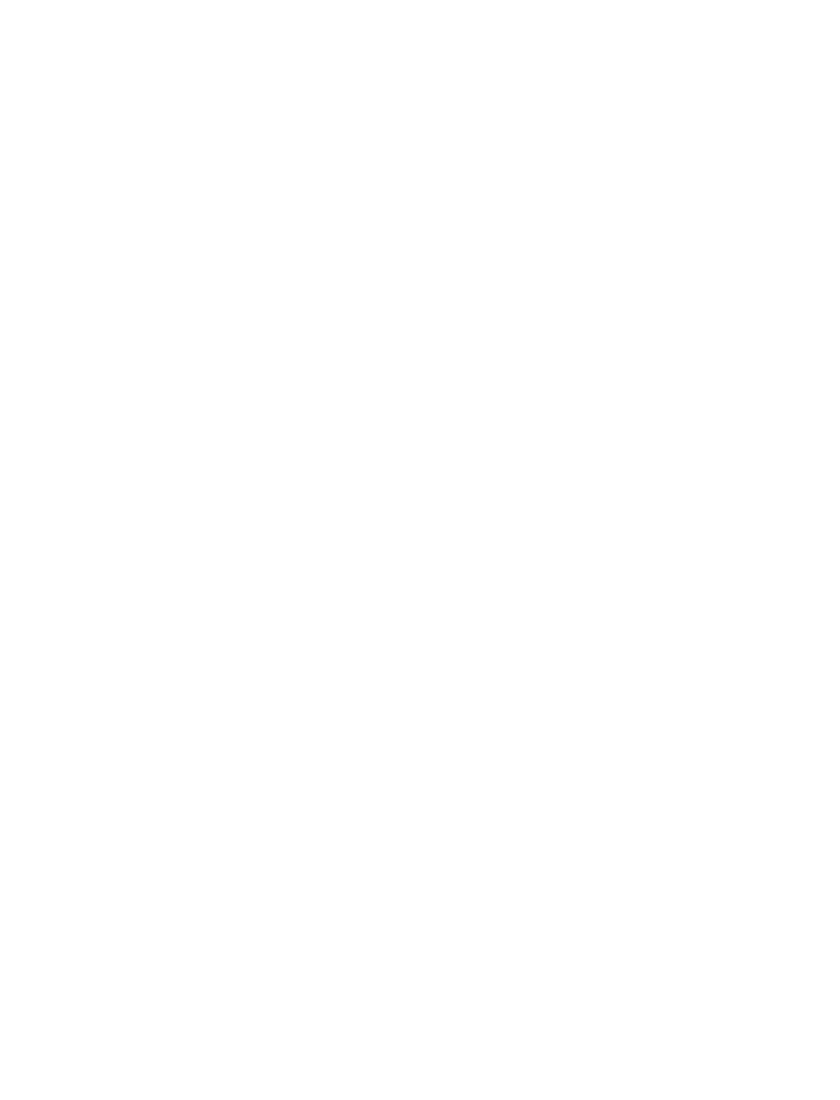
VENTED SINTERED-PLATE NICKEL-CADMIUM BATTERIES 27.21
Evaluation of cell-to-battery case leakage current, part of objective 3, when the battery
is first received for maintenance will determine the electrical need for cell cleanup as well
as the presence of cracked or leaking cell cases. This procedure may be conveniently carried
out by the simple expedient of completing a circuit from each cell terminal to the battery
case with a fused ammeter. A significant amount of leakage current through the ammeter to
the case from anywhere in the cell electric circuit indicates the presence of a conductive
path, through potassium hydroxide, on the external surfaces of the cell cases. Such a con-
ductive path may result from spewing of the electrolyte during overcharge, which may in-
dicate either overfilling or the existence of a cracked or leaky cell case. Isolation of the exact
cause can be accomplished by determining the leakage ‘‘nodal’’ point in the cell string by
repeating the measurements after physical cleanup of the battery.
Detection of the failure of the gas barrier, a very important part of objective 3, may be
reliably and conveniently accomplished by extending the C /10 charge to 24 h. This over-
charge will indicate accurately the failure of the gas barrier by either or both of two principal
measurements near the end of that overcharge. First, the overcharge gassing rate is extremely
sensitive to gas barrier condition and gas recombination. When measured with a simple ball
flowmeter, the 24-h gas rate will be less than 80% of normal if the barrier has failed sig-
nificantly in the cell. The normal value is 11 ml /min for each ampere of the C /10 overcharge
rate. The second indicator of gas barrier failure will be a 24-h overcharge voltage of less
than 1.5 V if the cell is being charged in a 23
⬚C ambient. Some downward adjustment of
this voltage criterion may be made at the rate of 4 m V/
⬚C if the battery is being charged
in a higher ambient temperature.
27.6.2 Mechanical Maintenance
The replenishment of water in the electrolyte to return the electrolyte to the level recom-
mended, objective 5, is the most important routine mechanical procedure employed during
battery reconditioning. It is best accomplished near the end of the 24 hours of the C/ 10 rate
charge by replenishing with deionized water until the electrolyte reaches the recommended
level for a battery in overcharge. A record of the amount of water usage in each cell should
be maintained and compared with the battery manufacturer’s statement of reserve electrolyte
level in each cell. If the total water usage between maintenance fillings, after deducting the
amount used during the maintenance procedure, exceeds the reserve available in that cell
design, the maintenance interval must be shortened to prevent plate dry-out during use and
resultant cell failure. Note that the 24-h C/10 reconditioning procedure will itself use ap-
proximately 0.4 ml of water for each Ampere-hour of rated capacity during the 24-h recon-
ditioning period. For example, 12 mL of water would be used during the reconditioning
period for a 30-Ah rated cell, and this must be subtracted from the amount added to deter-
mine the amount actually used in service. It should also be noted that a cell with a damaged
gas barrier may use less water.
That point in the maintenance procedure, following the thorough short-circuiting of each
cell, may be utilized to perform physical maintenance. Cells may only be replaced while in
the discharged state. Cleanup generally consists of a thorough rinsing with clear water fol-
lowed by warm-air drying of the battery. This will dissolve and remove any accumulation
of potassium hydroxide and carbonates from the outside of the cell jars. Vent caps should
also be washed in warm de-ionized water, warm water forced through the vent, and then
dried with warm air. This is safely accomplished only with the cells in the completely
discharged state. Replacement of any cells not found defective until the conclusion of the
C/ 10 overcharge requires discharging the cells a second time.
Other typical hardware problems include, loose terminal nuts—indicated by burns or
arcing on intercell links; terminal seal failure—various heavy deposits around cell terminal,
remove all hardware and the O-ring; vent failure—various heavy deposits on or around the
vent valve, the valve may have been installed improperly or the vent sleeve or O-ring has