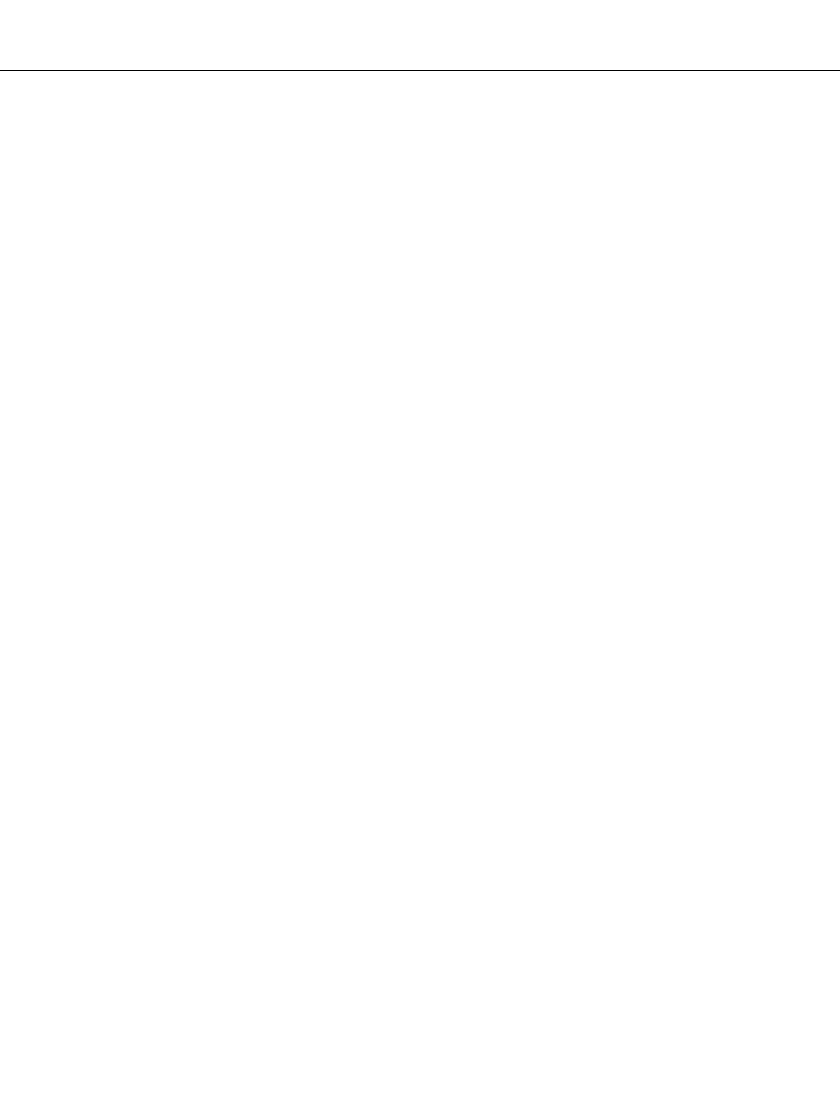
INDUSTRIAL AND AEROSPACE NICKEL-CADMIUM BATTERIES 26.15
26.6 FIBER NICKEL-CADMIUM (FNC) BATTERY TECHNOLOGY
26.6.1 FNC Electrode Technology
An ideal electrode will feature the following characteristics:
•
Provide a high surface area conductive matrix to contact the active material
•
Provide sufficient porosity for high active material loading and an open structure for good
electrolyte penetration.
•
Have sufficient electrical conductivity to carry the current to the tab with minimal voltage
drop, yet will still be light
•
Fully contain the active material
•
Able to accommodate the dimensional changes during battery charge and discharge without
fatigue cracking
•
Tolerate mechanical shock and vibration
•
Chemically and thermally inert to the battery environment. Will not introduce any unde-
sirable impurities into the cell.
•
Utilize a simple process for the loading of the active material
•
Strong enough to tolerate the cell manufacturing processes
•
Versatile enough to allow manufacturing of various sizes, thickness, conductivity, and po-
rosity
•
Economical
It is in this area of plate design that the FNC technology has made a significant step
forward in comparison to older technologies. The core of the FNC technology is the three-
dimensional nickel-plated fiber matrix. The nickel coating is optimized to the expected cur-
rent density of the battery. Thus, there is no excess nickel. Electrodes of thickness ranging
from 0.5 to 10 mm targeted at ultra high (XX), high (X and H), medium (M), and low rate
(L) designs are fabricated in a common process. The nickel fibers are very compact with
one cubic centimeter of electrode volume nominally containing 300 meters of conducting
filament. This current collecting matrix is 90% porous, allowing excellent utilization of the
active material. The result is improved low temperature performance, a lower charge coef-
ficient, and significantly higher power capability (see Fig. 26.1a).
The structure is highly porous and thus allows for high loading of active materials as
well as excellent penetration of electrolyte. No conductive dilutents like graphite or iron are
required. Yet, due to the very high surface area of the fibers, the contact between the current
carrying fiber matrix and the paste is very good. Because of this, losses are low, resulting
in improved efficiency. The paste is loaded into the electrodes mechanically, and no impu-
rities are introduced in the process. Active material (nickel hydroxide in the positive plate
and cadmium hydroxide in the negative) is mechanically imbedded directly into the fiber
plate. The pure active material contributes to longer life, lower self discharge and a more
consistent and reliable product (see Fig. 26.1b). Consequently, a high surface area plate
capable of high current loads and very long life has been realized.
The processes and cell design associated with FNC technology have resulted in improved
battery performance. Improved charging efficiency has reduced the gassing on overcharge,
and with it, the frequency of water topping for the vented cells. The design of the FNC plate
allows elastic expansion and contraction during charge and discharge, eliminating one of the
main causes of nickel cadmium plate degradation. This plate flexibility also provides in-
creased shock and vibration tolerances. The flexibility of the electrode structure eliminates
mechanical cracks and associated plate degradation resulting in increased battery life.