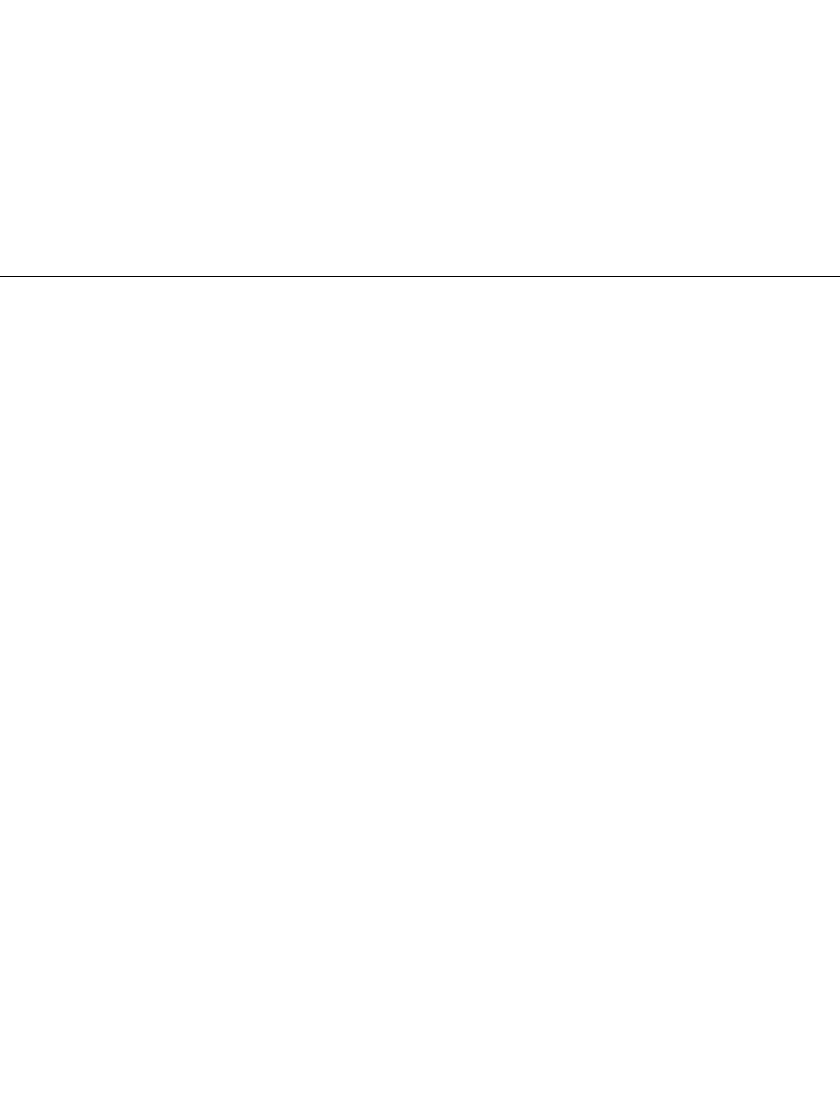
LITHIUM-ION BATTERIES 35.85
35.7.5 Conclusions: Polymer Li-ion Batteries
Polymer Li-ion batteries offer specific performance comparable to cylindrical and prismatic
Li-ion batteries within a unique, thin form factor. In addition to providing a thin form factor,
the batteries offer many properties desirable for commercial applications including good rate
capability, low self-discharge, long storage stability and the ability to safely sustain physical
or electrical abuse. These products are now being produced in high volume and are being
used in increasing quantities in cell phones and PDAs.
35.8 THIN-FILM, SOLID-STATE Li-ION BATTERIES
A specialized type of Li-ion battery developed for semi-conductor and printed circuit board
(PCB) applications are thin-film, solid-state devices. These batteries which employ ceramic
negative, solid electrolyte and positive electrode materials, can sustain high temperatures
(250
⬚C), and can be fabricated by high volume manufacturing techniques on silicon wafers
which are viable as on-chip or on-board power sources for microelectronics.
97,98
Batteries of
this type can be very small, 0.04 cm
⫻ 0.04 cm ⫻ 2.0
m. For microelectronics applications,
all components must survive solder re-flow conditions, nominally 250
⬚C in air or nitrogen
for 10 minutes. Cells with liquid or polymer electrolytes cannot sustain these conditions
because of the volatility or thermal stability of organic components. Further, cells that employ
lithium metal also fail as solder re-flow conditions exceed the melting point of lithium
(180.5
⬚C).
A schematic drawing of a thin-film, solid-state Li-ion cell is shown in Fig. 35.106. These
cells are fabricated by sequential layer deposition of the cell components using rf magnetron
sputtering, except for the metallic current collector components which are deposited by DC
magnetron sputtering. The deposition conditions for LiCoO
2
99
and lithium phosphorous ox-
ynitride (LiPON) electrolyte are reported in the literature.
98
The cells are fabricated on a
substrate, typically alumina, quartz, soda-lime glass, or silicon. Positive current collectors of
gold or platinum (0.1
mto0.3
m), over a layer of cobalt (0.01
m to 0.05
m, to
improve adhesion), have been used. Cells using either LiCoO
2
or LiMn
2
O
4
positive electrode
materials have been fabricated. The positive electrode layer of laboratory test cells is typically
0.05
mto5
m thick and 0.04 cm
2
to 25 cm
2
in area, depending on the capacity required
by the application. The electrolyte layer, LiPON, is typically 0.7
mto2
m thick.
Cells with and without negative electrode materials have been fabricated.
100
In cells with
a negative electrode material, SiSn
0.87
O
1.20
N
1.72
(SiTON), SnN
x
, InN
x
or Zn
3
N
2
have been
used. To accommodate the difference in volumetric capacity of positive and negative elec-
trode materials, the thickness of the negative electrode is typically 7% of the positive elec-
trode. Negative current collectors of copper, titanium, or titanium nitride (0.1
mto0.3
m)
are typical. To enhance the hermeticity of the cell, protective overlayers of LiPON (1
m)
or parylene (6
m) and titanium or aluminum (0.1
m) have been used.
Alternatively, the negative electrode materials may be omitted. A schematic diagram of
this type of cell prior to and after initial charge is illustrated in Fig. 35.107. In these cells,
lithium metal is plated onto the negative current collector when the cell is charged. The
lithium plating-stripping process is efficient with this technology. Thus cells with a negative
electrode material are typically engineered to oversaturate the negative electrode material, or
the negative electrode material is omitted completely.