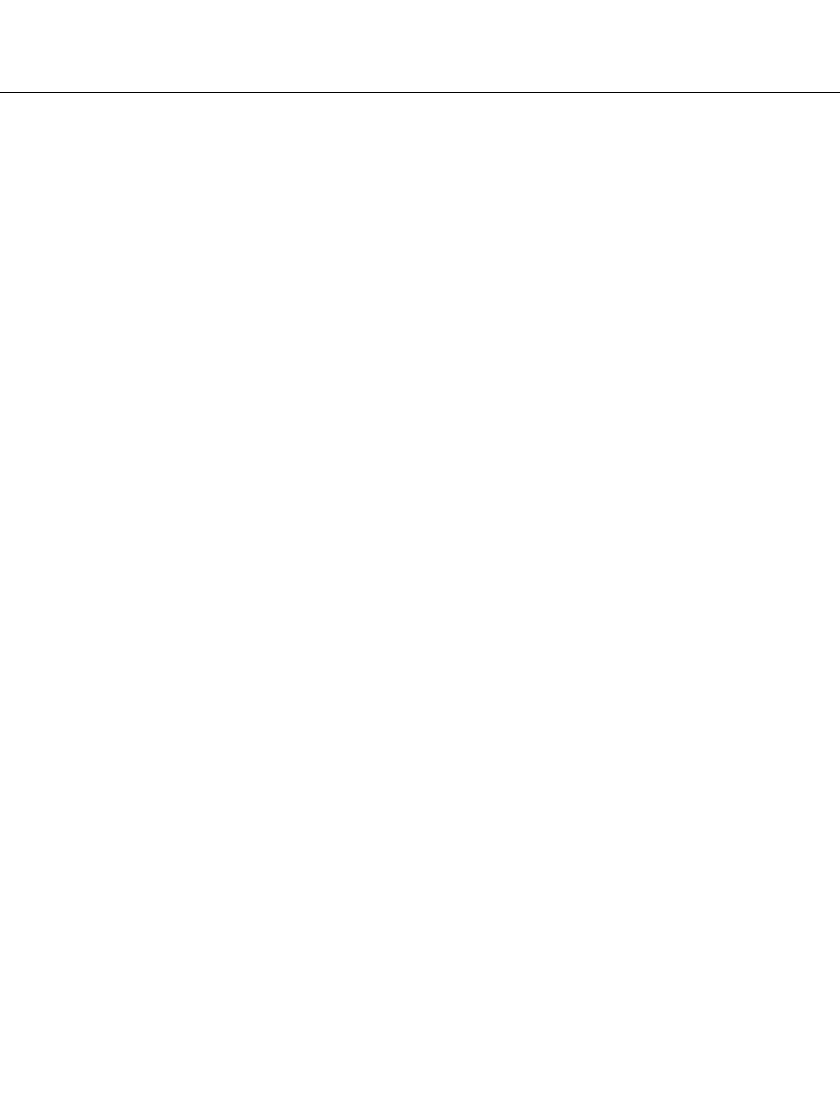
LITHIUM-ION BATTERIES 35.31
35.3 CONSTRUCTION OF CYLINDRICAL AND PRISMATIC Li-ION
CELLS AND BATTERIES
Cylindrical and prismatic Li-ion batteries have been developed. Wound designs are typical
in small cells (
⬍4 Ah); however in large cell designs, prismatic configurations with flat plate
construction are more common. For prismatic Li-ion batteries two cell design types are
practiced, flat mandrel wound pseudo-prismatic designs and flat-plate true prismatic designs.
Since Li-ion cells are fabricated in the discharged state, they must be charged before use.
35.3.1 Construction of Wound Li-ion Cells
The construction of a cylindrical wound Li-ion cell is illustrated in Fig. 35.30. The fabrication
of wound prismatic cells is similar to cylindrical versions except that a flat mandrel is used
instead of a cylindrical mandrel. A schematic diagram of a wound prismatic cell is shown
in Fig. 35.31. The construction consists of a positive and negative electrode separated by a
16
mto25
m thick microporous polyethylene or polypropylene separator. Positive elec-
trodes consist of 10
mto25
m Al foil coated with the active material to a total thickness
typically
⬃180
m. Negative electrodes are typically 10
mto20
m Cu foil coated with
a carbonaceous active material to a total thickness
⬃200
m. The thin coatings and separator
are required because of the low conductivity of non-aqueous electrolytes,
⬃10 mS /cm,
88
and
slow Li
⫹
diffusion in the positive and negative electrode materials, about ⬃10
⫺
10
m
2
s
⫺
1
.
Typically a single tab at the end of the wind is used to connect the current collectors to their
respective terminals. The case, commonly used as the negative terminal, is typically Ni-
plated steel. When used as the positive terminal, the case is typically aluminum. Most com-
mercially available cells utilize a header that incorporates disconnect devices, activated by
pressure or temperature, such as a PTC device, and a safety vent. One design is illustrated
in Fig. 35.32. These devices can limit cell performance at high rates, i.e. in a typical 18650
cell, 12 A discharge results in disconnect after 20 seconds once the temperature of the
disconnect device reaches 70
⬚C due to resistive heating. The header-can seal is typically
formed through a crimp.
In a typical 18650 cell, the positive current collector is coated on both sides with 12 g
of LiCoO
2
resulting in an electrode thickness of ⬃7.0 mil. Typically 6.5 g of carbon is used
on the negative electrode and the positive to negative ratio is such that the carbon negative
is utilized at a maximum of 270 mAh /g, 10% less than the capacity typical for MCMB
carbon and 100 mAh/g less than the theoretical capacity of carbon, (372 mAh/g).
89
The
mass distribution for the components in two 18650 products is illustrated in Fig. 35.33.
For specialized applications, such as for satellites, larger cylindrical cells have been de-
veloped. The ‘‘25 Ah’’ cells developed by Blue Star Advanced Technology, are depicted in
Fig. 35.34. These products utilize a LiCoO
2
based positive and a graphite negative. As shown,
the header incorporates two glass-to-metal seal terminals, a rupture disk and a fill port. The
mass of the major components of one cell is described in Table 35.10. As indicated, the cell
container accounts for 14% of the mass while the electrodes and the electrolyte account for
81% of the cell mass. This cell delivers 121 Wh /kg and 280 Wh /L, slightly less than the
lower aspect ‘‘25 Ah Design II’’ cell which offers 125 Wh/ Kg and 265 Wh/L.