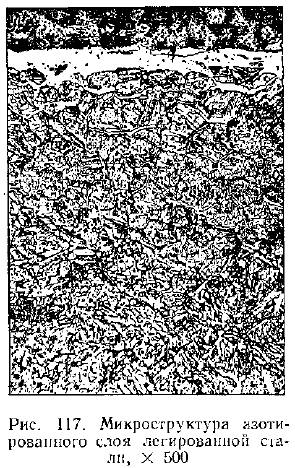
179
Для азотирования детали нагревают в специальной герметически закры-
той печи, через которую пропускают аммиак NH
3
. При нагреве аммиак разлага-
ется по реакции
2NH
3
=3H
2
+2N (атомарный)
Образующийся атомарный азот N поглощается поверхностью стали и
проникает вглубь детали.
Если главным требованием, предъявляемым к азотированному слою, яв-
ляется высокая твердость и износостойкость, то применяют сталь, содержащую
алюминий. Наиболее распространенной маркой стали является сталь 38ХМЮА.
Эта сталь кроме железа и углерода (0,35-0,42%) содержит хром (1,35-1,65%),
молибден (0,15-0,25%), алюминий (0,7-1,1 %). При азотировании такой стали
азот в поверхностном слое образует химические соединения, называемые нит-
ридами (нитриды: железа Fe
2
N, хрома CrN, молибдена MoN, алюминия AlN).
Нитриды придают поверхностному слою стали очень высокую твердость (до
HV 1200).
Процесс азотирования длится очень долго - до
90 ч, что является его основным недостатком. Тол-
щина азотированного слоя получается обычно 0,3-0,6
мм. Микроструктура азотированной специальной
стали приведена на рис. 117. На поверхности образу-
ется белый не-травящийся слой нитридов, а глубже -
сорбитообразная структура. Твердость и толщина
азотированного слоя зависят от температуры. Чем
выше температура азотирования, тем глубже слой, но
меньше твердость.
Если азотированию подвергается не вся по-
верхность детали, а только некоторые ее части, то места, не подлежащие азоти-
рованию, предохраняются от проникновения в них азота покрытием тон- ким