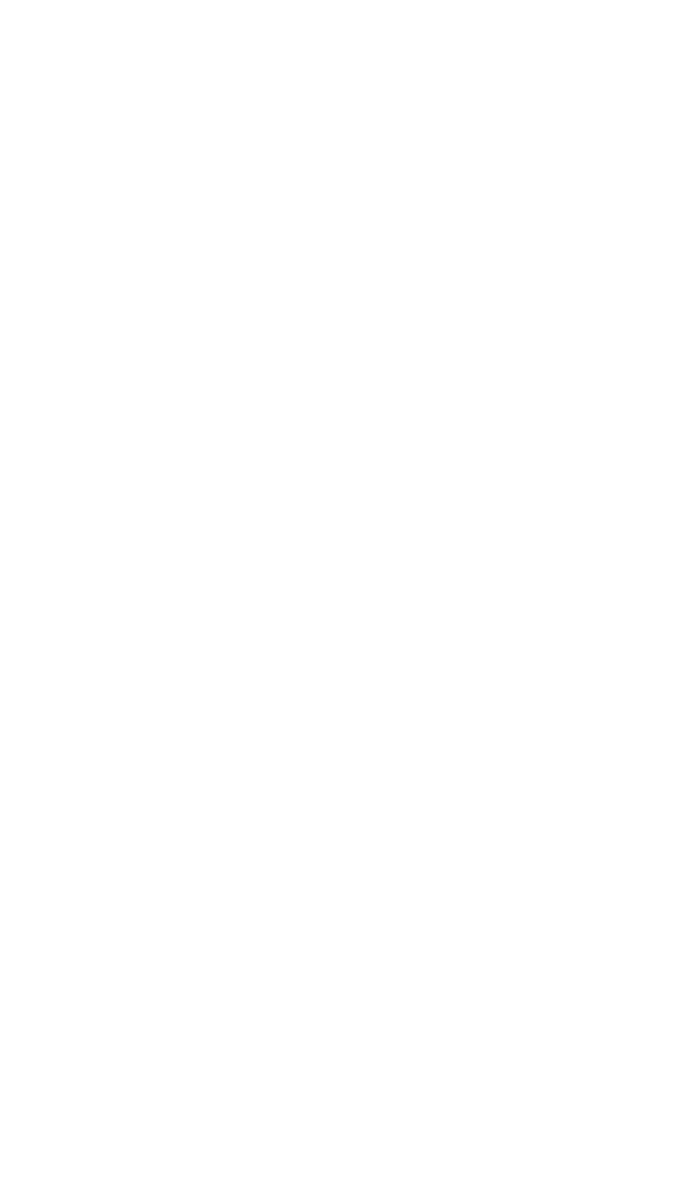
478 MANAGING MATERIALS DATA
CAE input and output data.
5
‘‘Simulation data management’’ is vital to the in-
tegration of CAE into the product development process. The benefits are anal-
ogous to those of materials data management systems and include:
●
Improved access to authorized data sources
●
Higher throughput for analysts and designers, resulting in faster and more
reliable engineering decisions
●
Fewer simulation errors, increased repeatability of simulation methods,
with full traceability
●
Enhanced collaboration between design and simulation, within the enter-
prise and throughout the supply chain
The Internet, or World Wide Web, has been credited with the substantially
increased market for PDM-type systems. Being universal, inexpensive, accessi-
ble, and hardware-independent, web-enabled PDM formed a prototype for web-
enabled materials data management systems. Even in organizations where the
databases are not fully integrated, and legacy systems remain, web enablement
allows the data from multiple sources to be displayed on the screen at the same
time. This includes not only data from the PDM system but from the shop floor,
parts management systems, purchasing, finance, shipping, and legacy systems
as well. Once accessed, a web interface, with the look and feel of standard
reporting mechanisms, can be used to generate reports by simply printing the
screen. Most companies find that establishing a workable web browser interface
as a front end to their PDM system is quite simple, requiring minimal program-
ming expertise and technical support.
6
While the Internet provides access from or to vastly different sources, the
Intranet has enabled organizations to distribute materials information from a
centralized location to all its satellite offices and divisions. This bourgeoning
expertise has facilitated the distributed ‘‘build-design’’ teams in many global
enterprises that support the ‘‘design anywhere, build anywhere’’ business model.
As use and acceptance of these systems expand, additional applications have
surfaced in the area of business-to-business collaboration. The power of the
Internet allows companies to readily transact with each other and access each
other’s information, making collaboration a reality. The first wave of Internet
collaboration was in the supply chain, as companies worked with customers,
suppliers, and intermediaries to manage inventories. By simplifying transactions
and sharing information, companies continue to drive down costs, cut cycle
times, and reduce inventories. The cutting edge of supply-chain collaboration is
moving upstream from there. Intermediaries and suppliers are now doing col-
laborative planning and forecasting, creating a shared vision of what customers
will eventually buy, so that the right product can be in the right place at the
right time. Companies are also collaborating on product development. Instead
of a system maker and a component supplier developing their products separately
and then trying to make them fit, they use a shared design database to develop
everything together from the outset. In some industries, competitors are stan-
dardizing on common parts and practices by sharing information over the Inter-
net. Companies must be prepared to work with others—not out of a sense of