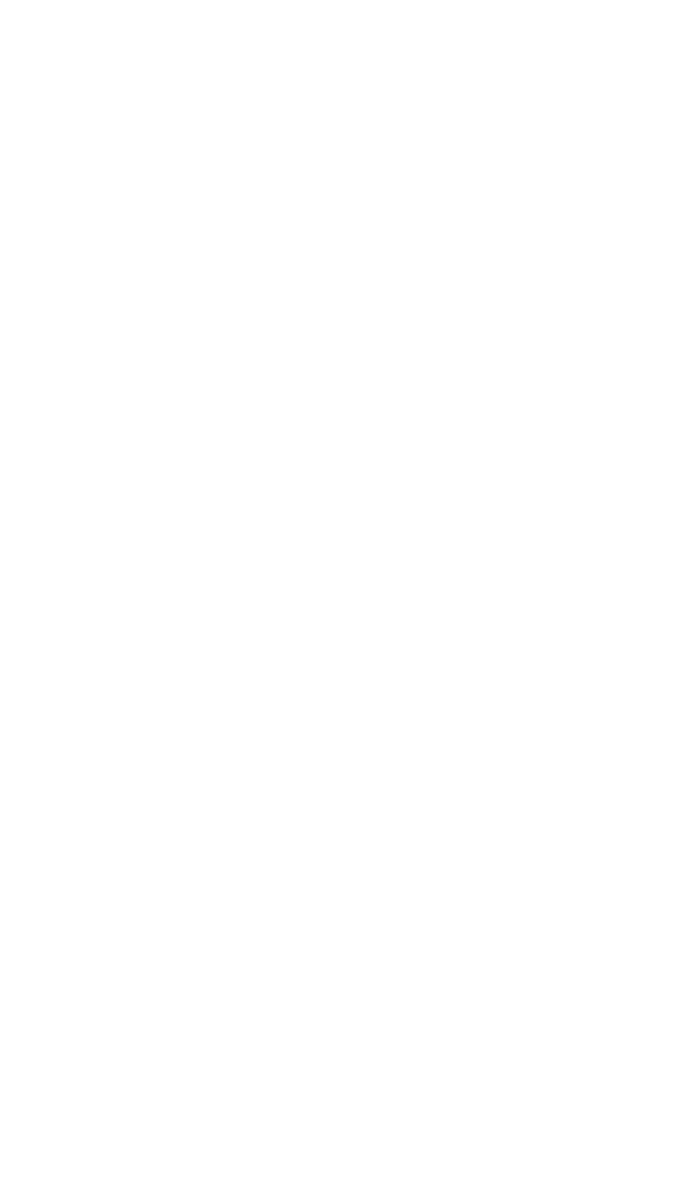
422 OVERVIEW OF CERAMIC MATERIALS
encountered in a simply shaped billet of material. This is an important point of
which a design engineer specifying a ceramic component needs to be constantly
mindful.
3 BRITTLENESS AND BRITTLE MATERIALS DESIGN
Even when ceramics are selected for other than mechanical applications, in most
cases some level of strength and structural integrity are required. It is therefore
necessary to briefly discuss the issue of brittleness and how one designs with
brittle materials before proceeding to discuss applications and the various ce-
ramic and glass materials families and their properties.
The main issues in designing with a brittle material are that a very large
scatter in strength (under tensile stress), a lack of capacity for mitigating stress
concentrations via plastic flow, and relatively low energy absorption prior to
failure dominate the mechanical behavior. Each of these issues is a result of the
presence of one or more flaw distribution within or at the surface of the ceramic
material and/or the general lack of plastic flow available in ceramics. As a
consequence, ceramic and glass components that are subjected to tensile stresses
are not designed using a single valued strength (deterministic design) as com-
monly done with metals. Rather, ceramic components are designed to a specified
probability of failure (probabilistic design) that is set at acceptably low values.
The statistics of failure of brittle materials whose strength is determined by a
population of varying sized flaws is similar to modeling the statistics of a chain
failing via its weakest link. The statistics utilized are known as Weibull statistics.
A Weibull probability of failure distribution is characterized by two parameters,
the characteristic stress and the Weibull modulus.
7
Computer programs for in-
corporating Weibull statistical distributions into finite-element design codes have
been developed that facilitate the design of ceramic components optimized for
low probabilities of failure.
8
The effectiveness of such probabilistic design meth-
odology has been demonstrated by the reliable performance of ceramics in many
highly stressed structural applications, such as bearings, cutting tools, turbo-
charger rotors, missile guidance domes, and hip prosthesis.
Flaws (strength-limiting features) can be intrinsic or extrinsic to the material
and processing route by which a test specimen or a component is made. Intrinsic
strength-limiting flaws are generally a consequence of the processing route and
may include features such as pores, aggregations of pores, large grains, agglom-
erates, and shrinkage cracks. While best processing practices will eliminate or
reduce the size and frequency of many of these flaws, it is inevitable that some
will still persist. Extrinsic flaws can arise from unintended foreign material en-
tering the process stream, i.e., small pieces of debris from the grinding media
or damage (cracks) introduced in machining a part to final dimensions. Exposure
to a service environment may bring new flaw populations into existence, i.e.,
oxidation pits on the surface of nonoxide ceramics exposed to high temperatures
or may cause existing flaws to grow larger as in the case of static fatigue of
glass. In general, one can have several flaw populations present in a component
at any time, and the characteristics of each population may change with time.
As a consequence of these constantly changing flaw populations, at the present
time the state of the art in life prediction of ceramic components for use in
extreme environments significantly lags the state of the art in component design.