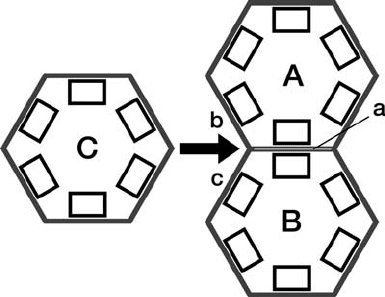
of its sides shared with one polygon (A), and another side shared with one of the sides
of the other polygon (B). This is depicted in Figure 9.18. The solution of this equation
is n ¼ 6. This proves that a manufacturing system composed of regular hexagonal cel ls
occupies the minimum floor space.
In addition to the smaller floor space that is achieved by the honeycomb
architecture, it has the advantage that new hexagonal cells can be easily integrated
into the existing honeycomb system. Integrating additional manufacturing cells scales
up the production capacity and functionality of the whole system.
The honeycomb structure has many potential applications in machining and
assembly systems. Personalized design of automobile interiors, as described in
Chapter 3, may generate many thousands of variants of auto interiors. The assembly
of each component requires specific tools, and may require different assembly times.
It is unfeasible to apply a traditional serial assembly line with so complex an assembly
program. It is also impractical to assume that personalized production can maintain
the pace of a typical line generating a throughput of one car every 50–60 seconds.
Floor space will also be a premium in personalize production with so many
components being offered.
If the new personalized production paradigm becomes a reality, Ford’s serial
moving assembly line (invented in 1913) must be replaced by a new approach. A new
conceptual system for final assembly of personalized auto interiors is depicted in
Figure 9.19. In this system, each small square represents a station where a particular
component is being assembled. Each car moves in a route that fits the combination of
components that have to be installed. Popular components will require more than one
assembly station.
Now, 100 years after the invention of the moving assembly line, and with enabling
advances in information technology, and under changing global imperatives, new
approaches to assembly need to be developed. We offer this new conceptual system,
and other non-serial assembly systems will certainly be developed in the future. In any
case, because of the unpredictable demands of the global manufacturing revolution
Figure 9.18 From all regular polygons with n > 4 only the hexagon (n ¼ 6) can fit
between two joint polygons, A and B, such that it has two shared sides b and c.
HEXAGONAL RMS CONFIGURATIONS 249