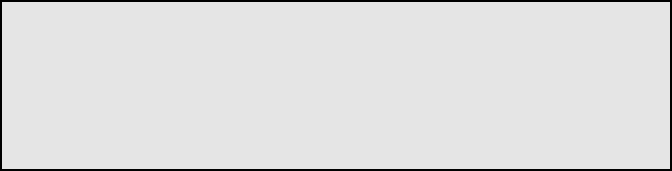
positions even when the electrical power is disconnected. This design solves the
challenge of holding non-ferrous (e.g., aluminum) parts directly to a magnetic chuck.
The hydraulic power source holding the part is contained in the fixture base, which
eliminates the need for hydraulic feed lines and makes this reconfigurable fixture
practical.
We close with a prac tical example of a reconfigurable tool, provided by one of our
students.
“In our plant we utilize (in 2005) a Production Adaptive Assembly System (PAAS) tool,
which would be considered a reconfigurable assembly machine. Its concept is to be a
reconfigurable fixturing system. It is basically a miniature robot that holds parts in proper
location while they get welded together. They provide the benefit of being able to build
different styles at different dimensional locations (i.e., customization). These modules
appear about the size of round kitchen trashcan, and have a computer control that allows
them to be moved in three axes. ” B. J. Baker
8.5 RECONFIGURABLE INSPECTION MACHINES
The in-process RIM represents a new class of inspection equipment that allows in-
line measurements of machined parts. The machine deploys a non-contact mea-
surement system of electro-optical sensors whose location and number are
reconfigurable according to the part that is being measured (within its part family).
During the inspection process these sensors are fixed and the part moves along an
axis-of-motion (or vice versa—fixed part and moving sensors) examining the
features that are in the sensor range. The RIM rapidly supplies information about
the dimensional accuracy and surface quality of each part, and instantly transmits
feedback for rapid diagnosis and correction of the manufacturing process. The RIM
is applicable to medium- or high-volume production of a whole family of parts, and
has a superior advantage where regular sw itchovers among parts within a family are
the practice.
Current Practice: In contrast, current practice in large- or medium-production
machining plants involves the use of CMMs for parts inspection. The CMM is
a computer-controlled part measurement method utilizing a single mechanical
contact probe that moves around the part taking targeted measurements while the
part is stationary. It can take up to several hours to complete the inspection of a single,
complex part specimen, and so the inspection process is done off-line, usually in
a special inspection room. During this inspection, many faulty parts might be
produced on the still-operating production line. For example, at a typical rate of
two parts per minute over a 2-hour inspection interval, 120 bad parts may be produced
before the error is detected.
220 RECONFIGURABLE MACHINES